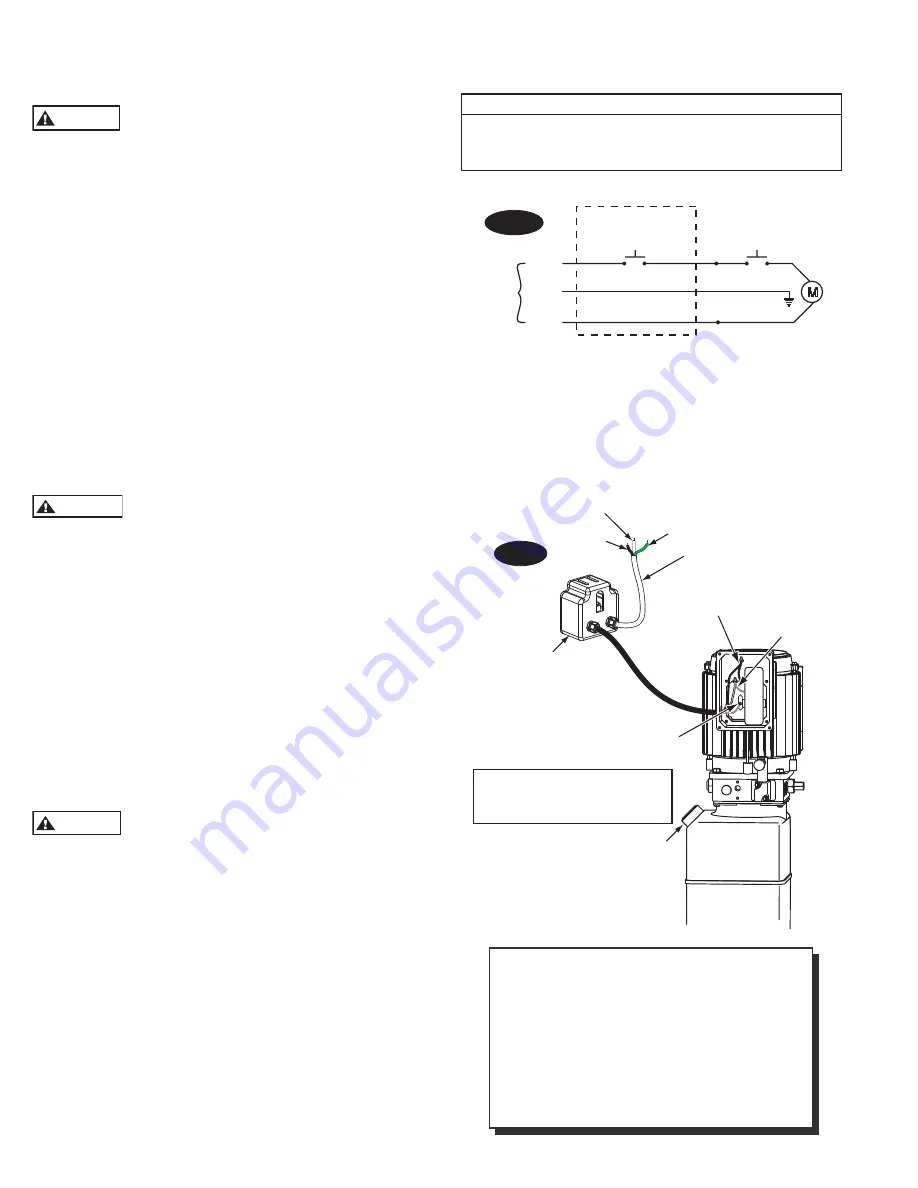
14
14. Electrical:
Have a certified electrician run appropriate
power supply to motor, Figs. 19 and 20. Size wire for 20
amp circuit. See Motor Operating Data Table.
CAUTION
Never operate the motor on line voltage less
than 208V. Motor damage may occur.
IMPORTANT:
Use separate circuit for each power unit.
Protect each circuit with time delay fuse or circuit breaker.
For single phase 208-230V, use 30 amp fuse. For wiring see
Figs. 19 and 20. All wiring must comply with NEC and all
local electrical codes.
Note:
60Hz. single phase motor
CAN NOT
be run on 50Hz.
line without a physical change in the motor.
15. Overhead switch:
Check overhead switch assembly
to assure that switch bar is depressing switch plunger
sufficiently to actuate the switch. The overhead switch is
wired normally open, see Fig. 20. Lift will not operate until
weight of switch bar is depressing switch plunger. Verify
that Power Unit stops working when switch bar is raised,
and re-starts when the bar is released.
CAUTION
When bleeding, hold a shop cloth over
bleeder screw to buffer the air and fluid while bleeder-
valve is open.
16. Oil Filling & Bleeding:
Use Dexron III ATF, or
Hydraulic Fluid that meets ISO 32 specifications. Remove
fill-breather cap, Fig. 20. Pour in (8) quarts of fluid. Start
unit, raise lift about 2 ft. Open cylinder bleeders approx. 2
turns, Fig. 13.
Close bleeders when fluid streams. Torque values for the
bleeders are 15 ft. lb. minimum and 20 ft lb. maximum. Fully
lower lift. Add more fluid until it reaches fill line on the
tank. System capacity is (14) quarts. Replace fill-breather
cap.
CAUTION
If fill-breather cap is lost or broken, order
replacement. Reservoir must be vented.
Single Phase Power Unit
MOTOR OPERATING DATA TABLE - SINGLE PHASE
LINE VOLTAGE
RUNNING MOTOR VOLTAGE RANGE
208-230V 50Hz.
197-253V
208-230V 60Hz.
197-253V
Note: 60Hz. Single phase motor CAN NOT be run on 50Hz.
line without a physical change in the motor.
Overhead Switch
Max. Voltage: 277V
Max. Current: 25A
Connect supply to wires in box.
Attach ground wire to screws
provided.
Fill Breather Cap
Attach ground wire here.
208-230V 60Hz
Single Phase
Attach black wire
to black wire.
Attach white
wire to red wire.
Black
Green
White
M
230V
60Hz
1 Ø
Black
Green
White
Overhead
Limit Switch
Up
Switch
White
Black
Black
NOTE: Assure cord used for connection
between the overhead switch and power
unit is of the type specified in:
UL201, Sections 10.1.1.3 & 10.1.1.4
(Example: SO, G, STO) Size for 25 amp
circuit. See UL 201, Section 15 for proper
wiring requirements for this connection.
Fig. 20
Fig. 19
Summary of Contents for SPO16
Page 31: ...31 Notes...