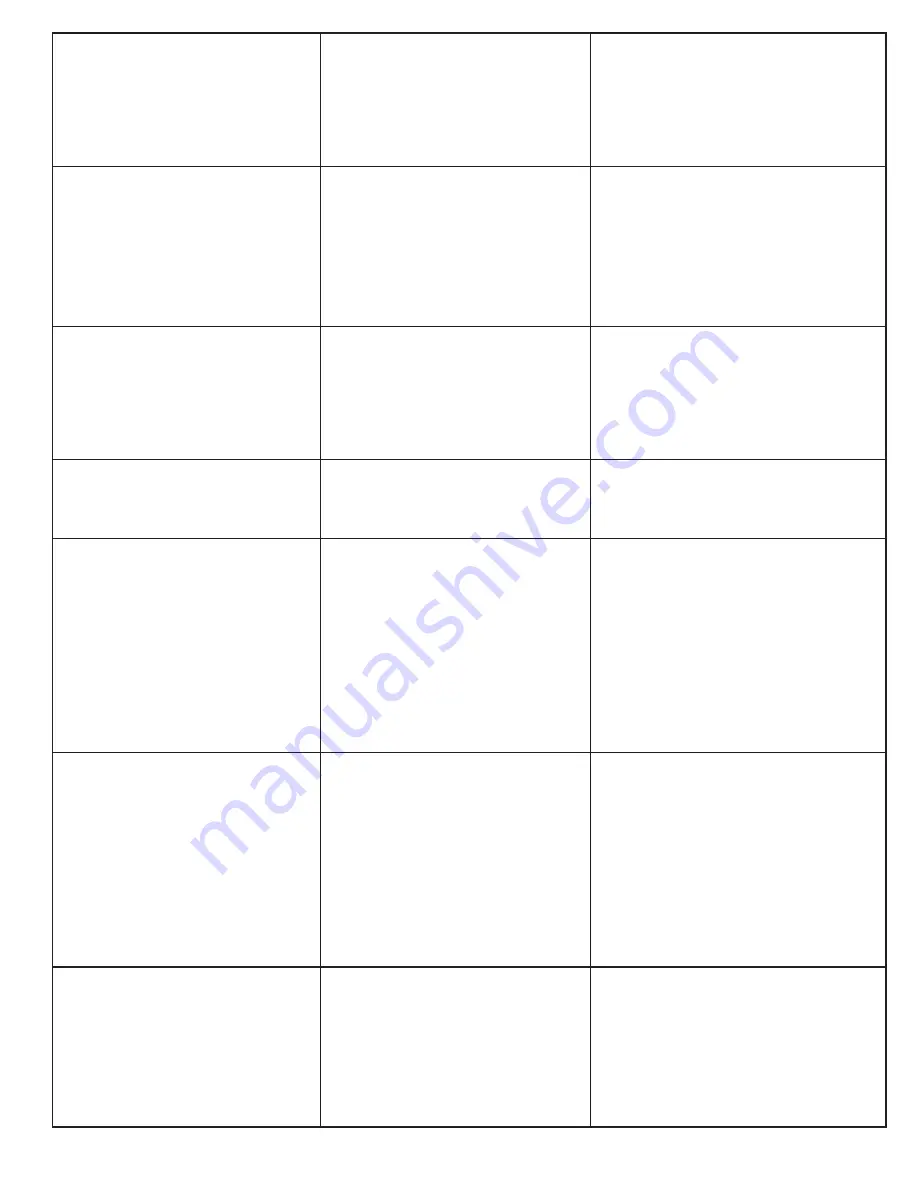
26
Hydraulic oil leaking from the
filler/breather cap.
• Air has mixed with the oil or
is being sucked in.
• Oil return line is loose.
• Hydraulic hose is damaged.
Depending on cause:
• Change oil (
→
Chapter 9.4).
• Tighten fittings on suction pipe.
• Attach return line.
• Replace hydraulic hoses.
Runways lift unevenly
(Height difference in runways).
• Cables are out of adjustment
• Lift not leveled.
• Floor is uneven.
Depending on cause:
• Correct the cable tension
(
→
Chapter 11.11 and 13.4).
• Reset and accurately level the lift.
• Place spacers/shims underneath (
Chapter 13. Commissioning).
Anchor is loose.
• Assembly fault,
for example drill holes are
too big or load capacity of
concrete floor is inadequate.
Depending on cause:
• Repair the lift.
• Re-install
(
→
Chapters 11 to 13). Follow
installation requirements.
Runways either do not lift to full
rise or they chatter during lifting.
• Hydraulic oil level too low.
Check oil level. If required bleed
the hydraulic cylinder
(
→
Assembly manual).
Runways do not lower.
• Inadequate air supply.
• Locking latches are offset.
Depending on cause:
• Check air pressure and adjust of
nece-
ssary (6 ... 8 bar).
• Check whether air lines are
leaking or crushed.
• Check locking mechanism, repair
if necessary.
Locking latches not latching or
can not be released.
• Compressed air supply inter-
rupted.
• Faulty control valve for air
supply.
• Locking mechanism is
jammed.
• Air cylinder for locking mech-
anism is dirty.
Check locking mechanism, repair if
necessary.
Lowering process stops abrup-
tly.A buzzer sounds, the control
unit is out of order.
• Cable is too slack.
• Cable broken.
Depending on cause:
• turn main switch to "OFF“ and
lock it.
• Check all cables.
Replace faulty or warped cables (
Chapter 9.6).