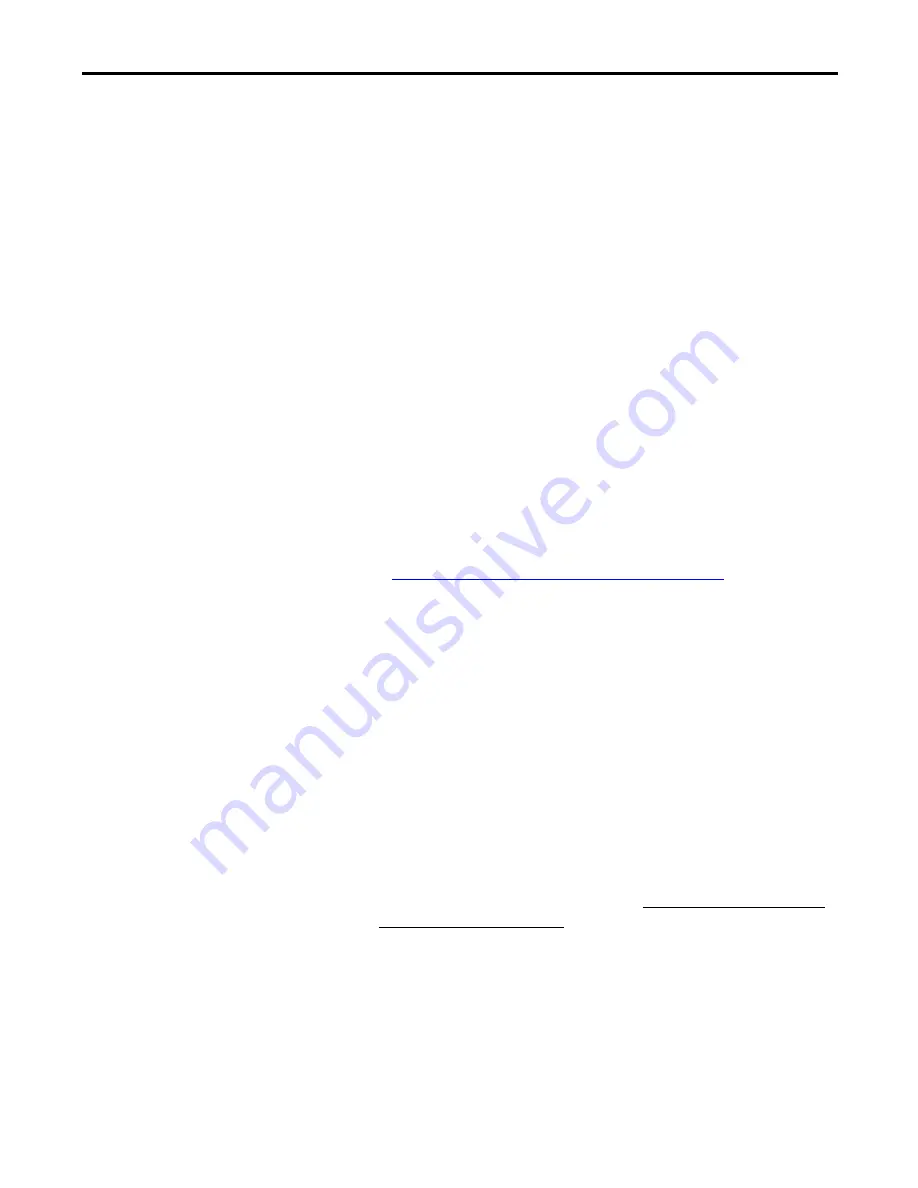
Rockwell Automation Publication 7000L-UM301F-EN-P - March 2020
405
Component Definition and Maintenance
Chapter 5
individuals involved in extinguishing the fire or anyone in close proximity should
wear a self-contained breathing apparatus to protect against any inhalation of
toxic gases.
Disposal
When disposing of the drive, it should be disassembled and separated into groups
of recyclable material as much as possible (i.e. steel, copper, plastic, wire, etc.).
These materials should then be sent to local recycling facilities. In addition, all
disposal precautions mentioned above must also be taken for those particular
materials.
Preventive Maintenance
Check List
The preventive maintenance activities on the PowerFlex 7000 Liquid-Cooled
Drive (C-Frame) can be broken down into two categories:
• Operational Maintenance
– can be completed while the drive is running.
These checks should be done periodically depending on operating
conditions; the time between maintenance should not exceed three
months.
• Annual Maintenance
– should be completed during scheduled downtime.
Tool / Parts / Information Requirements on page 410
section for a list of documentation and materials needed to properly complete the
preventive maintenance documents.
Operational Maintenance
The PowerFlex 7000 “C” frame drive uses a mixture of de-ionized water and
Glycol to cool down the devices. One of the desired qualities of this mixture is
the low conductivity; a second is the low freezing point. The latter is required in
climates where the temperature can drop below 0°C. The maintenance on the
system can be done with the drive running by closing valve # V8 and V9. They
must be re-opened when the changes are done.
The maintenance includes the following tasks:
• Changing the DI Cartridge
– The DI cartridge keeps the conductivity
low by removing positive ions from the DI water/glycol solution. It needs
to be changed whenever the conductivity warning appears. This occurs
when the conductivity increase above 1μS.
The DI cartridge cannot be
cleaned, it must be replaced.