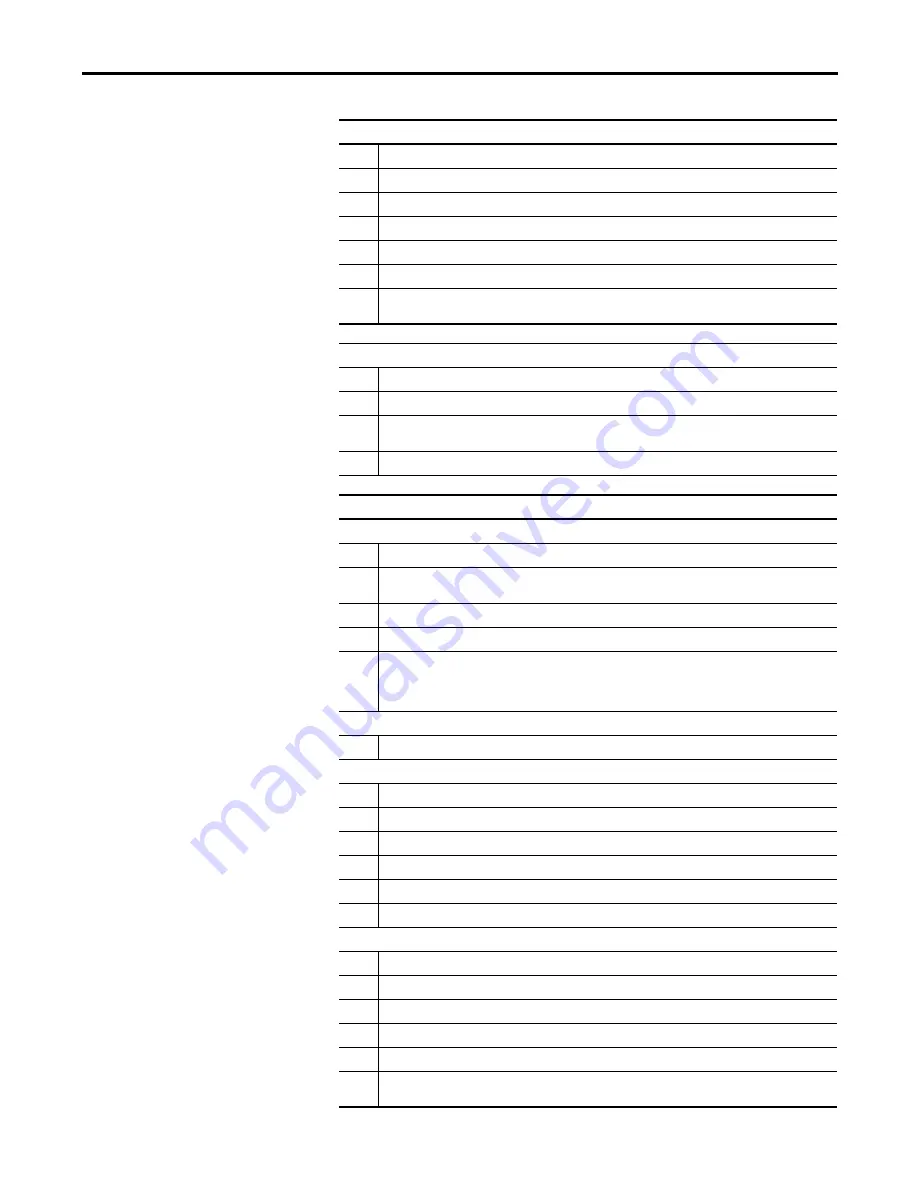
Rockwell Automation Publication 7000L-UM301F-EN-P - March 2020
181
Commissioning
Chapter 4
Service Data
Record customer name, location, date and drive ID number
Record drive nameplate data
Record motor nameplate data and compare it to the dimensional drawings
Record encoder nameplate data, if applicable
Record harmonic filter nameplate data, if applicable
Record source of control power, auxiliary cooling information, environmental conditions, drive password
Record all Dip switch settings, jumper settings and revision levels on printed circuit boards, power supplies,
communication modules and protective relays
Control Power Off Tests
Verify mechanical interlocks
Perform a resistance check on all devices and snubber circuits
Verify that the 3-phase control power coming into the control section is within specification. Most drives will
not have this option
Verify that all additional sources of low voltage power are within specification and have grounded neutrals
Control Power On Tests
Power Supply Tests
Apply control power and verify that AC voltages are within specifications
Verify the AC/DC output is 56V DC at the input of the DC/DC converter and at the input to gate driver power
supplies. Adjust if necessary
Verify the 20V output of SGCT IGDPS boards
Verify that all of the DC outputs in the DC/DC converter are at rated value
Verify that healthy lights are on for all control boards and firing boards (Use wire harness with power supply
adapter to test SCR gate driver boards or use the test power harness [part no. 80018-695-51; one for 2kV
drives, two for 3 and 4 kV drives and three for 6 kV drives] with the appropriate standard IEC line cord to test
the rectifier SGCT devices using the SPS power supply boards)
Converter Tests
Confirm that SCR and SGCT gating pulse sequence are correct for all devices
Programming the Operator Interface
Verify preliminary parameter settings
Calibrate signal conditioners
Set analog outputs
Fault masks / External faults
Analog I/O
PLC In/Out
System Tests
Perform a system test with low voltage control/test power
Prove all protection functions as desired
Verify that all emergency stop devices are functioning correctly
Calibrate the analog I/O
Verify that the drive cooling fan(s) is/are operating properly
Measure input contactor drop out time (2-cycle advance warning needed if input contactor is not part of drive
line-up)