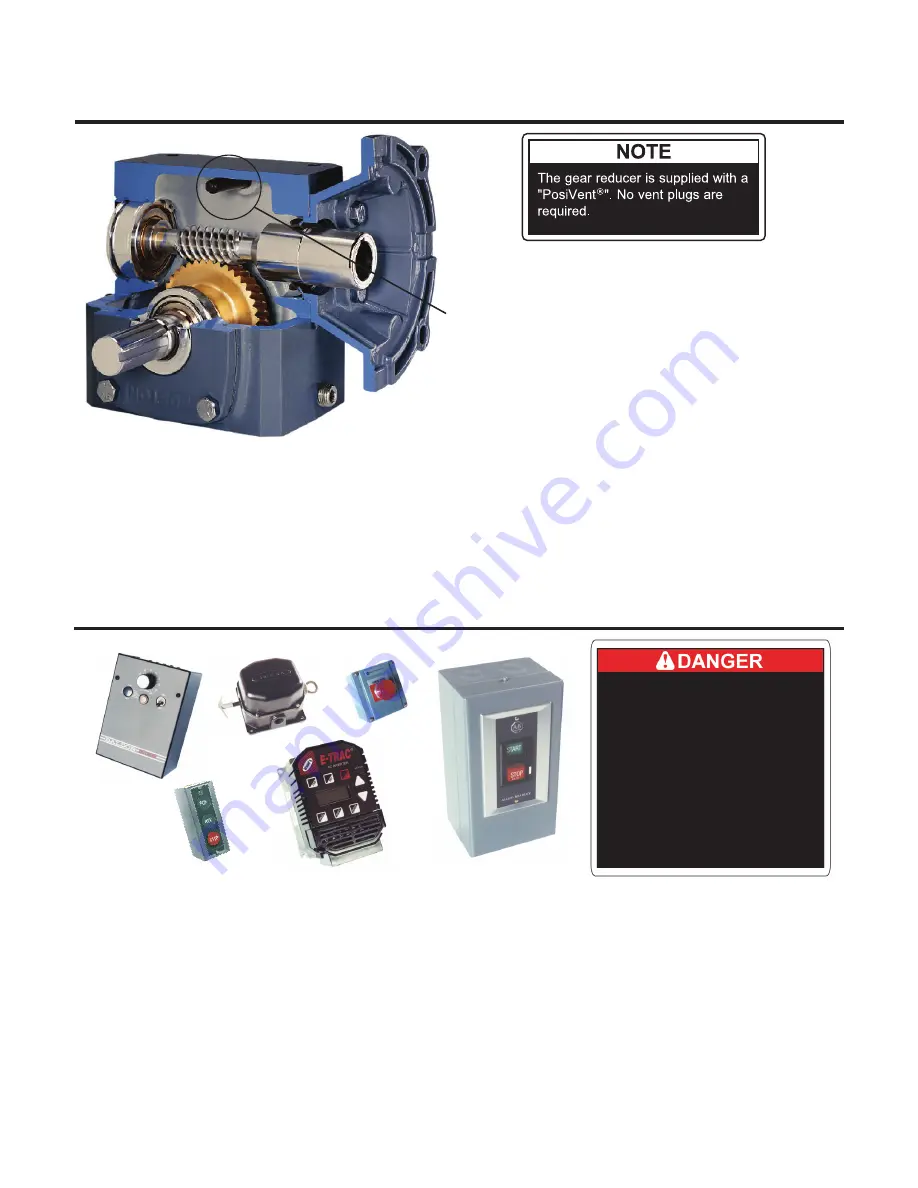
START-UP PROCEDURES
GEAR REDUCER VENT PLUG
PREPARING FOR INITIAL START-UP
Before conveyor start-up, all operators and
other personnel coming in contact with unit
must be properly trained and must have
read accompanying Tech Handbook.
Provisions must be in order to instruct all
personnel coming in contact with conveyor
on the location of emergency stops,
pull cords, etc.
A routine maintenance program should
be implemented before unit is placed into
operation so that fundamental unit compo-
nents are attended to. This maintenance
program should include an inspection
to ensure that any dangerous or hazard-
ous operating conditions are noted and
IMMEDIATELY corrected, as well as includ-
ing
electrical and mechanical unit inspections
and corrections.
Finally, when conveyor is initially started,
an immediate visual inspection should
include motor, gear reducer, belt tracking
(discussed in following section under “Belt
Tracking”) and related adjustments noted in
handbook for unit/component corrections.
WARN ALL PERSONNEL TO KEEP CLEAR OF
CONVEYOR DURING UNIT START-UP
Electrical controls must be designed by a
qualified electrical engineer to ensure that
appropriate safety features (emergency stops,
pull cords, switches, etc.) are installed on unit
for safe operation. Before conveyor start-up,
all operators and other personnel coming in
contact with unit must be properly trained
and must have read accompanying Tech
Handbook.
PosiVent
Unique design incorporates a single seam
construction. Factory filled with synthetic lubrication for
universal mounting. Lubed for life, no oil changes are
required.
To expedite the installation and start-up process, all gear red ucers are shipped filled with oil. The reducers are sealed and lubed for
life and require no oil changes.
11
Summary of Contents for 138LRC
Page 1: ......
Page 9: ...V BELT PATHS V BELT PATH FOR SPURS AND CURVES 9...
Page 17: ...MODEL 138LRC ILLUSTRATIONS FOR UNIT WITH END DRIVE SIDE MOUNT END DRIVE 17...
Page 19: ...MODEL 196LRC ILLUSTRATIONS FOR UNIT WITH END DRIVE SIDE MOUNT END DRIVE 19...
Page 21: ...MODEL 138LRCS ILLUSTRATIONS FOR UNIT WITH END DRIVE SIDE MOUNT END DRIVE 21...
Page 23: ...MODEL 196LRCS ILLUSTRATIONS FOR UNIT WITH END DRIVE SIDE MOUNT END DRIVE 23...