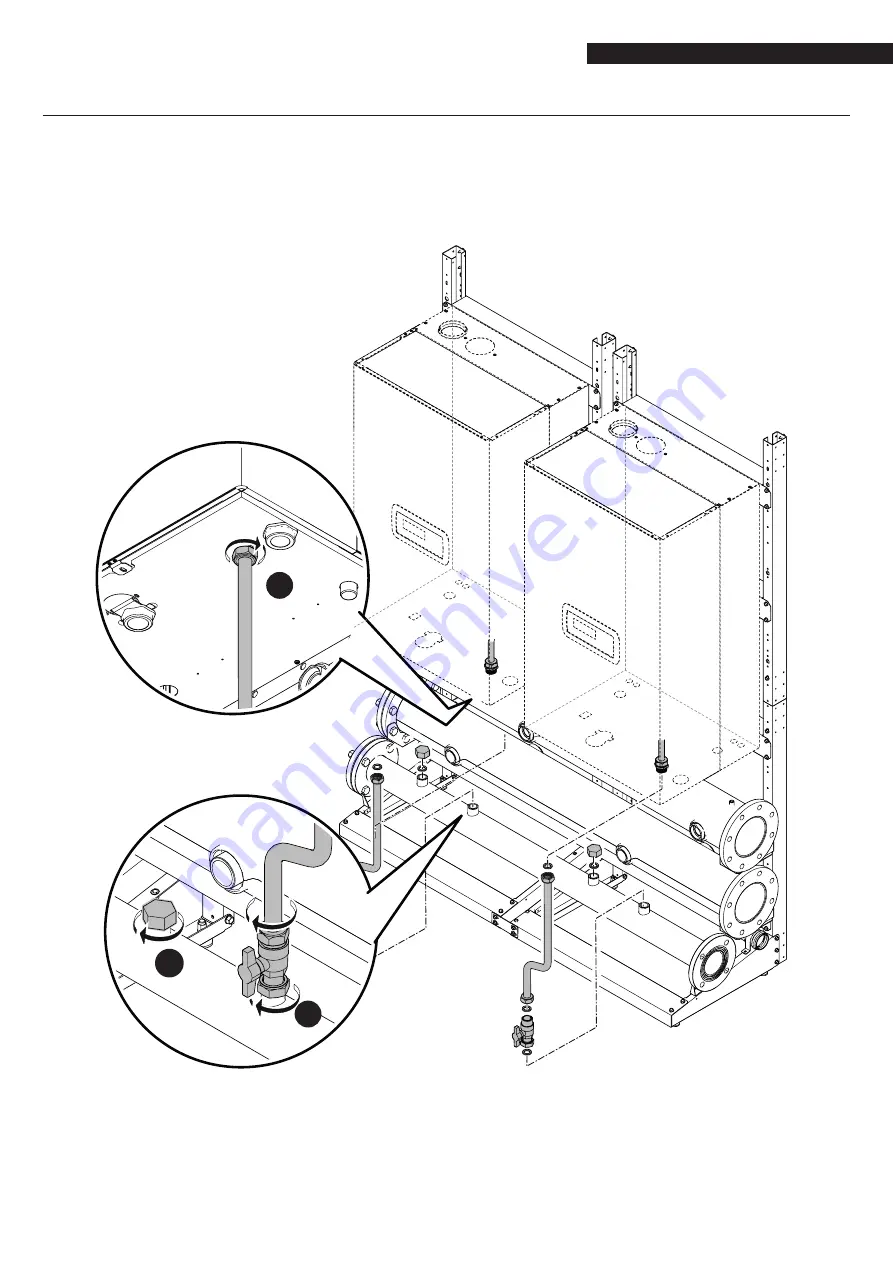
39
INSTALLATION
2.7
Positioning the GAS PIPES
CASCADE CONFIGURATION IN-LINE
Assembly of the gas pipes. Components included in code 20130658 – 20131121 – 20131122 – 20131123 – 20131124 - 20131125.
1
Install and seal the gas pipe to the thermal module.
2
Install and seal the cock to the pipe and the gas manifold.
3
Fit the plugs onto any unused coupling points ensuring tightness.
1
3
2
Summary of Contents for Condexa PRO 100
Page 32: ...32 INSTALLATION 7 Position the GAS manifold 8 Secure the GAS manifold to the frame 7 7 8...
Page 33: ...33 INSTALLATION 9 Position the manifold closing plugs from the required side 9 22mm 51mm...
Page 36: ...36 INSTALLATION 7 Position the GAS manifold 8 Secure the GAS manifold to the frame 8 8 7...
Page 37: ...37 INSTALLATION 9 Position the manifold closing plugs from the required side 9 22mm 51mm...