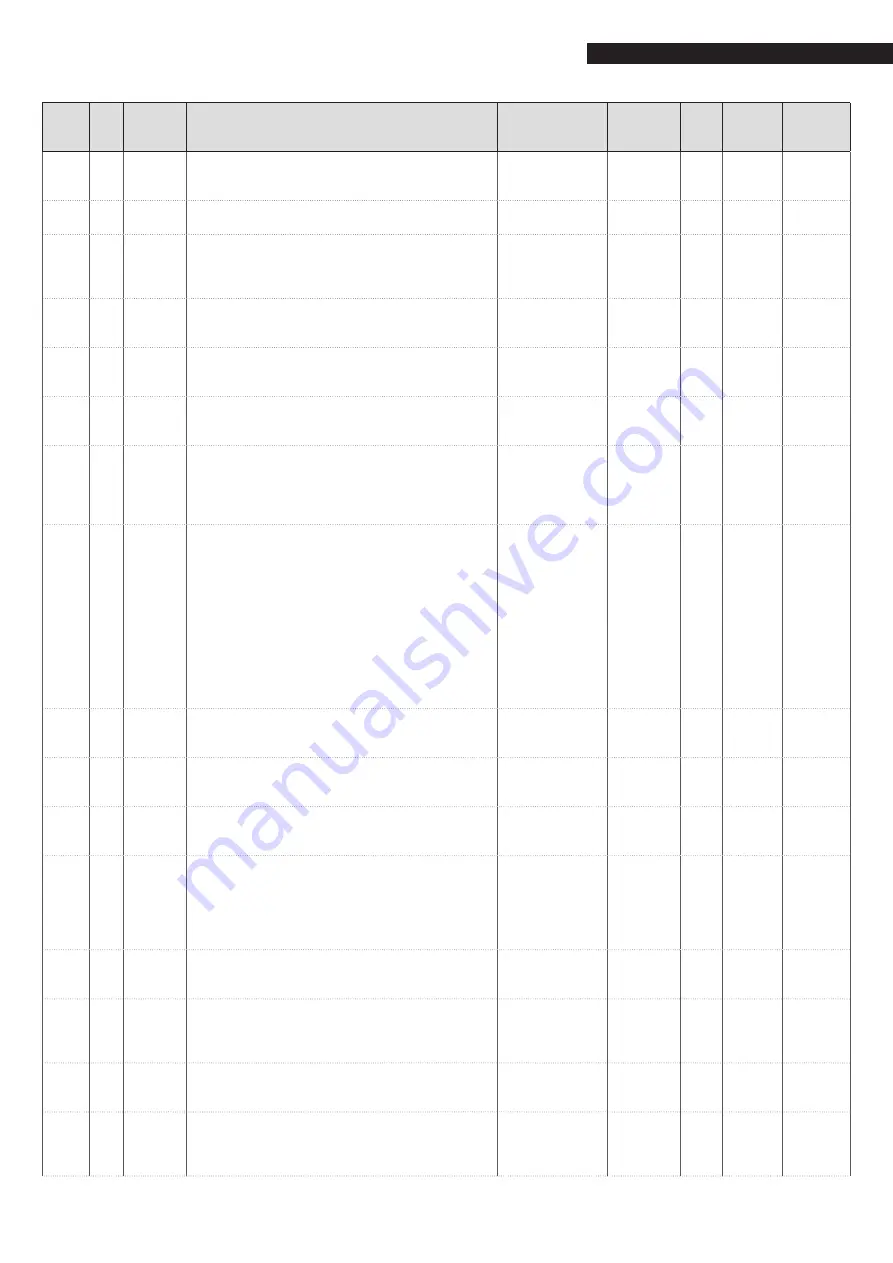
45
INSTALLATION
Menu Par.
No.
Nr. dis-
played
Display
Description
Range
Default
setting
UM
Access
type
Category
M1
129
Flow
sensor
Defines the type of flow sensor used.
Bitron, Huba:
DN8, DN10, DN15,
DN15, DN20, DN25
Huba
DN25
I
General
M1
133
Mod.
Pump dT
Defines the delta T set for the operation of the
modulating circulator.
5…40
15
°C
I
General
M1
134
Mod.
Pump
Start
Time
Defines the time in seconds from the moment the
burner is switched on to start the modulation of
the circulator and obtain the delta T specified in
Par. 133.
0…255
120
Sec.
I
General
M1
135
Mod.
Pump
Type
Defines the PWM circulator model installed.
0 = Wilo
1 = Salmson
2 = Grundfos
2 =
Grundfos
I
General
M1
136
Mod.
Pump
Mode
Defines whether the boiler's circulator operates in
modulating mode or at a set speed (as a percent-
age of maximum speed).
On/Off Modulat-
ing Fixed 20…
100%
Modulat-
ing
I
General
M1
137
Mod.
Pump
Min Pwr
Defines the percentage of speed that sets the min-
imum speed that the circulator can reach during
modulation.
0…100
30
%
I
General
M1
138
Appli-
ance
type
Value can vary depending on appliance configura-
tion based on Par. 97 and 98. This value is calculat-
ed by the board, which, based on an internal logic,
defines as a single number the settings of Par. 97
and 98.
0…255
Depends
on boiler
model
I
General
M1
139
Dair
active
Activates bleeding the system's air. To activate air
bleeding, it is necessary to switch on the boiler
and change the parameter from "No" to "Yes".
Wait for one minute. Switch off and restart. At this
stage, when it is restarted the boiler will initiate
the automatic bleeding procedure (lasting around
20 minutes). With the parameter set to "Yes", the
procedure is carried out each time the boiler is
switched off and restarted using its master switch.
The value must be set to "No" if you do not wish to
initiate the bleeding procedure when the thermal
module is switched on.
Yes, No
No
I
General
M1
140
Mini-
mum
Flow
Defines the flow rate below which the boiler is
switched off. The value varies depending on the
model.
0.0…100
Depends
on boiler
model
l/min
I
General
M1
107
Anti-Le-
gionella
day
Sets the weekday on which the anti-Legionella
procedure is carried out.
Sun…Sat.
Sun
Day
I
DHW
M1
108
Anti-Le-
gionella
Hour
Sets the time of the day during which the anti-Le-
gionella procedure is carried out.
0…23
0
Hour
I
DHW
M2
72
Permit
Emer-
gency
Mode
Activates the emergency mode. This mode comes
on when communication between Managing and
the primary circuit's probe is lost. In this event,
if Par. 72 is set to "Yes", the cascade is initiated,
working to the fixed set-point determined by Par.
74.
Yes/No
Yes
U
Cascade
M2
74
Emer-
gency
Set-point
Set-point active in emergency mode.
20…65
70
°C
I
Cascade
M2
75
Delay
Per Start
Next
Mod.
Defines the stand-by time in seconds to restart the
subsequent cascade module in normal start mode.
5…255
120
Sec.
I
Cascade
M2
76
Delay Per
Stop Next
Mod.
Defines the stand-by time in seconds to switch off
the last cascade module on in normal Off mode.
5…255
30
Sec.
I
Cascade
M2
142
Delay
Quick
Start
Next
Defines the stand-by time in seconds to restart the
next cascade module in quick start mode.
5…255
60
Sec.
I
Cascade