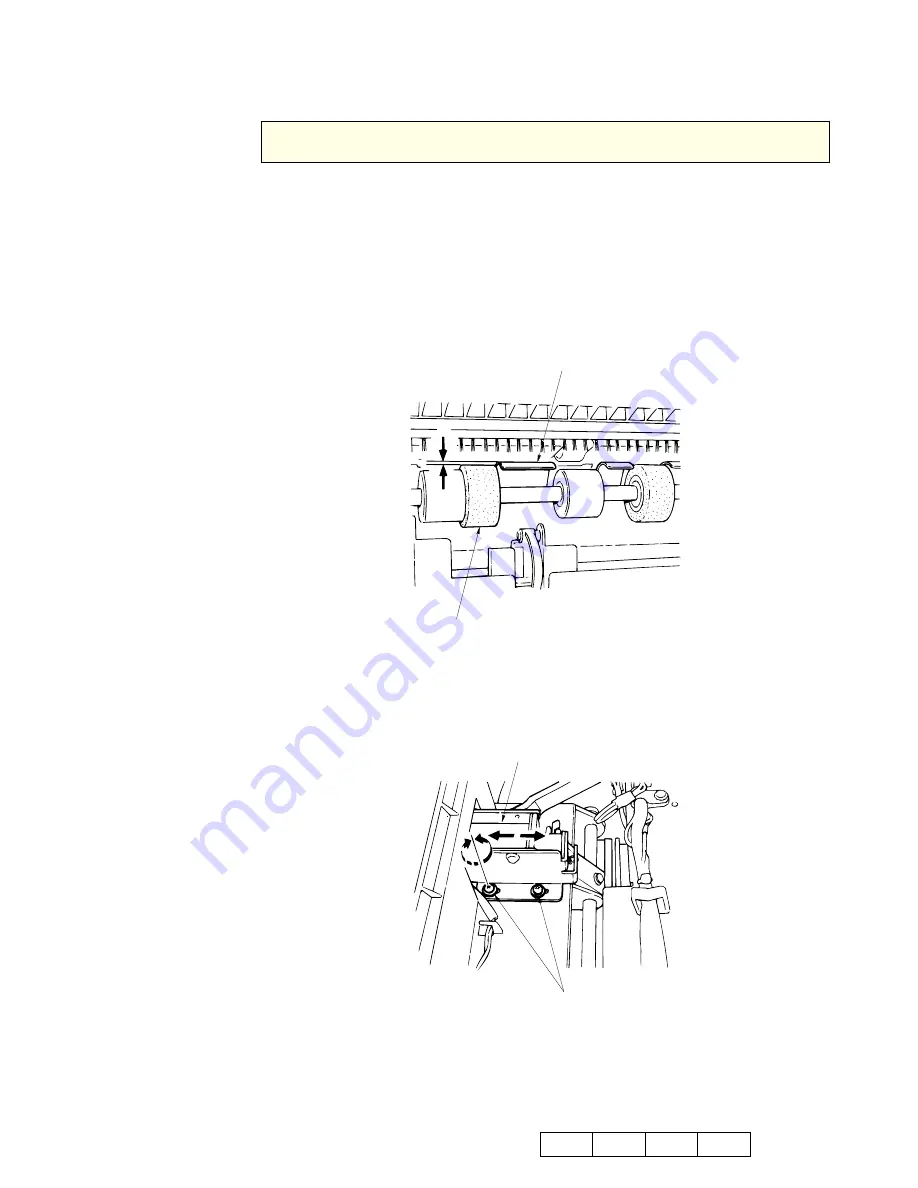
6-38
DDP70 Finisher Maintenance Manual
M M
L
0 0
6.7.7. Adjusting the Paper Exit Opening Lower Guide Plate
Applicable jigs and tools:
⊕
Screwdriver.
[Disassembling Procedures]
1. Remove the Rear Cover and the Top Cover.
(Refer to item 6.1.1 on page 6-1)
[Adjustment Procedures]
1. When the Paper Exit Opening Solenoid (SD4) is OFF, check whether the value of
the Lower Guide Plate is greater than that of the Paper Exit Roller.
Figure 6-64. Adjustment of the Paper Exit Opening Lower Guide Plate
2. Loosen the two Solenoid Bracket
⊕
screws then move and adjust the Solenoid.
3. Tighten the Solenoid Bracket
⊕
screws.
Figure 6-65. Adjustment of the Paper Exit Opening Lower Guide Plate
[Assembling Procedures]
1. Reinstall the Rear Cover and the Top Cover by reversing the procedure above.
CAUTION:
Be sure to turn OFF the MAIN AC POWER prior to performing the maintenance.
LOWER GUIDE PLATE
PAPER EXIT ROLLER
A
A = 1.5 mm minimum
BRACKET/SOLENOID
⊕
SCREWS
Summary of Contents for DDP70
Page 1: ...Standard Finisher Maintenance Manual 2005 Ricoh Printing Systems Ltd May 2005 N901402...
Page 4: ...i DDP70 Finisher Maintenance Manual Copyright 2005 Ricoh Printing Systems Ltd N901402...
Page 5: ...ii DDP70 Finisher Maintenance Manual...
Page 6: ...i Revisions Page Rev Machine Rev Page No Contents Date 00 First Edition May 2005...
Page 7: ...ii...
Page 8: ...Safety iii Safety Safety in Operation...
Page 9: ...iv DDP70 Finisher Maintenance Manual...
Page 13: ...iv DDP70 Finisher Maintenance Manual...
Page 17: ...1 4 DDP70 Finisher Maintenance Manual M M L 0 0...
Page 19: ...2 2 DDP70 Finisher Maintenance Manual M M L 0 0...
Page 49: ...4 20 DDP70 Finisher Maintenance Manual M M L 0 0...
Page 137: ...7 16 DDP70 Finisher Maintenance Manual M M L 0 0...