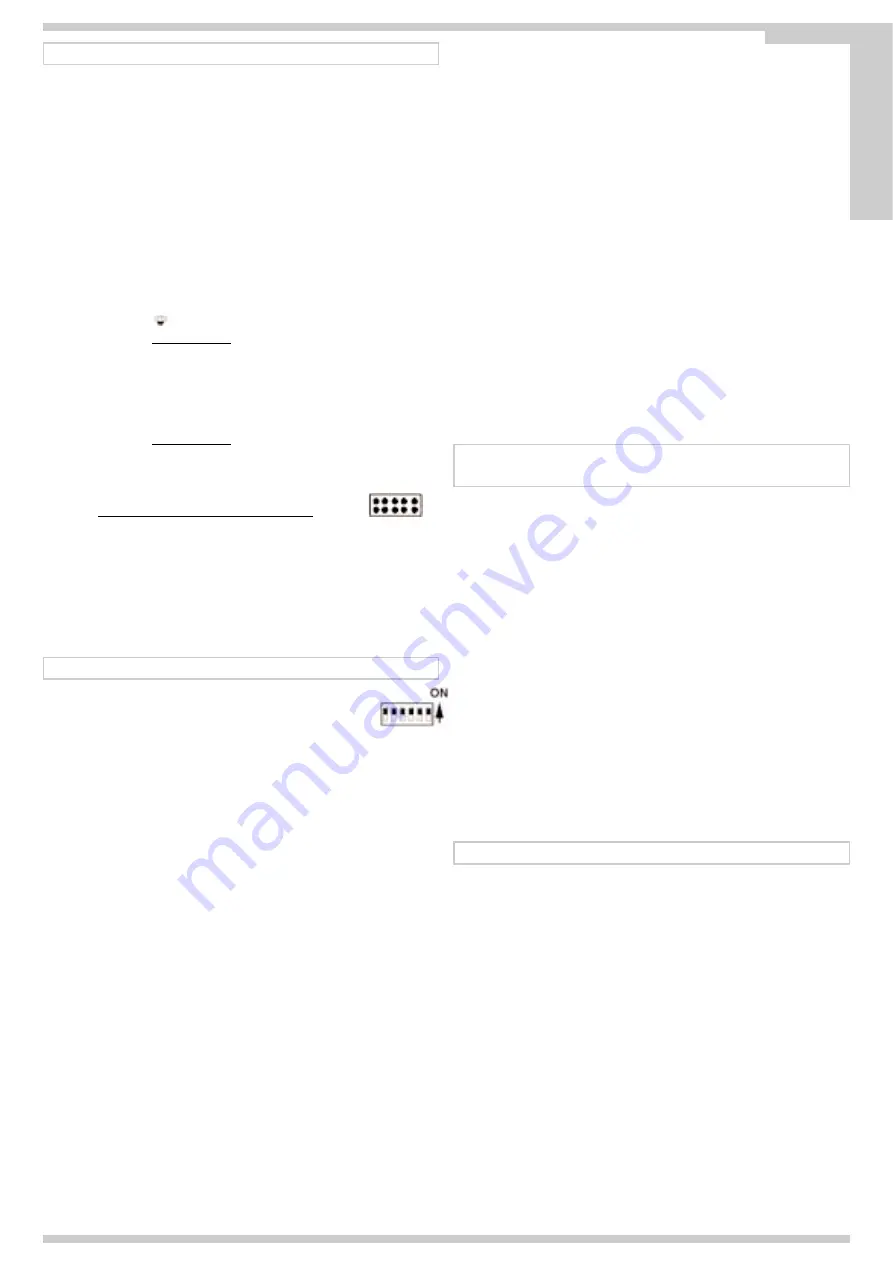
A - CONNECTIONS
J1 =>
SEC.TRANSF. Connector for secondary transformer
J2 =>
MOTOR 1 Connection MOTOR 1 (without polarity)
MOTOR 2 Connection MOTOR 2 (without polarity)
J3 =>
AERIAL
Radio Antenna
COM.
Common contact unit
PHOT.
Photocell contact (NC)
K BUTT.
Single impulse contact (NA)
SIGNAL
Gate open indicator and signal of working condition, with battery
and low battery (12Vdc 3W max)
BUZZER
Negative phase connection acoustic signal (12Vdc max 200 mA)
Respect polarity.
A -
Negative for power supply to accessories at 24Vdc
A+
Positive for power supply to accessories at 24Vdc
BLINKER
Negative phase connection flashing light at 24Vdc
(cod.ACG7061)
Respect polarity.
LOCK
Electro-lock connection (MAX 15W 12V)
J4 =>
SW
Connector dedicated to programming in the factory.
Do not insert any jumpers into the connector.
J5 =>
BATTERY CHARGER Connector for 24Vdc battery charger card (code
ACG4648)
J6 =>
RADIO incorporated radio module (model CRX), or connector for RIB trigger
radio receiver with 24Vdc power supply
J7 =>
L1 - N Power supply 230 Vac 50/60 Hz – external to the card - (120V/60Hz
upon request)
B - SETTINGS
DIP 1 (ON) - CONTROL FOR MOTOR ROTATION DIRECTION (POINT C)
DIP 2 (ON) - PROGRAMMING OF TIMING (POINT D)
DIP 1-2 MEMORIZATION/CANCELLATION OF RADIO CODES FOR
MOTOR CONTROL (ONLY MODEL CRX) (POINT E)
OPERATIONAL MICRO-SWITCHES
DIP 3 Waiting time before automatic closure (ON)
DIP 4 Photocells always active (OFF) – Photocells only active upon closing (ON)
DIP 5 Pre-flashing (ON) – Normal flashing (OFF)
DIP 6 Single impulse command (K BUTT) and step by step radio receiver (ON) -
automatic (OFF)
DIP 7 Functioning with current sensor (OFF-active) Time functioning (ON-activated).
DIP 8 Enabling of electric lock (ON-activated)
DIP 9 Enabling of electric lock release and release facility (ON-activated)
DIP 10 Enabling of electric lock coupling (ON- activated)
JP1
=> RESET
JP2
=> Check that the jumper is inserted!
JP3
=> Selection of functioning with 1 or 2 motors (closed grooves for 2 motors by default)
JP4
=> Available for special applications
PROG
=> SW1 Programming button
LOW SPEED => TM1 Electronic regulator for low speed on approach
Adjustment of low speed is carried out using the LOW SPEED Trimmer which varies the
output voltage to the head/s of the motor/s (turn clockwise to increase speed). Adjustment
is carried out to establish the correct speed at the completion of opening and closing,
depending on the structure of the gate, or if there is any light friction that could
compromise the correct working of the system.
M1 =>
Regulator for current sensor of motor 1
M2 =>
Regulator for current sensor of motor 2
LED SIGNALS
L1 photocell contact (NC) (red)
L2 not assembled
L3 not assembled
L4 gate opening M1 (green)
L5 gate closing M1 (red)
L6 gate opening M2 (green)
L7 gate closing M2 (red)
L8 control button K-Button (green)
L9 programming activated (red)
L10 radio code programming (green)
RELAYS
RL1 RELAY CLOSE MOTOR 1
RL2 RELAY OPEN MOTOR 1
RL3 RELAY CLOSE MOTOR 2
RL4 RELAY OPEN MOTOR 2
OMNIFET
Q1 POWER OMNIFET THAT CONTROLS MOTOR 1 BOTH ON OPENING AND ON
CLOSING
Q2 POWER OMNIFET THAT CONTROLS MOTOR 2 BOTH ON OPENING AND ON
CLOSING
FUSES
F
1.6A TRANSFORMER PROTECTION FUSE (external to card K2 24V)
F1
4A PROTECTION FUSE FOR ACCESSORIES
F2
4A PROTECTION FUSE FOR MOTOR 1
F3
4A PROTECTION FUSE FOR MOTOR 2
C – CONTROL FOR MOTOR ROTATION DIRECTION AND
CALIBRATION OF THE CURRENT/IMPACT SENSORS
1 - Place DIP1 to ON
=> LED L9 will begin to flash.
2 - Press the PROG. button and keep pressed
(movement is now performed in the man
present mode open-stop-close-stop-open-etc.) => RED LEDS L5 and L7 will light up
and the wings of the gate will close with a fixed interval of 4 sec. If they open instead of
closing, release the button and invert the two wires of the relevant motor.
3 - Once fully closed release the PROG. button.
4 - Press the PROG. button and keep pressed
=> GREEN LEDS L4 and L6 will light up
and the wings of the gate will open with an interval of 2 sec.
5 - Fully open the gate, release the PROG. button and carry out calibration of the
mechanical stops for opening (on the operator).
6 - Press the PROG button and keep pressed
until the gate is fully closed.
7 - Return DIP1 to OFF => LED L9 will go out, indicating exit from the test.
N.B.: During this test the photocells are not active.
CALIBRATION OF THE CURRENT/IMPACT SENSORS
1 - Turn M1 and M2 trimmers fully clockwise (+).
2 - Place DIP1 to ON.
3 - Press the PROG. button and keep pressed
leaving that the motors push in closing
the gate already closed. At the same time turn the M1 trimmer in an anticlockwise
direction until LED L5 (for M1) turns off (this turns off also the M1 motor).
4 - Repeat the procedure with trimmer M2 until LED L7 turns off (this turns off also the M2
motor). After that depress PROG push-button.
5 - Return DIP1 to OFF.
D – TIMING PROGRAMMING FOR 2 MOTORS (#)
CAN BE CARRIED OUT IN 2 WAYS:
MODE 1 – WITH CURRENT/IMPACT SENSOR (DIP 7 OFF)
1 - The gate must be fully closed.
2 - Position
DIP 2 to ON
=> LED L9 will emit brief flashes.
3 - Press PROG. button
=> M1 opens.
4 - Upon reaching the mechanical stop on opening, the CURRENT SENSOR stops M1
(with memorization of the time) => At the same time M2 is activated and opens.
5 - Upon reaching the mechanical stop on opening, the CURRENT SENSOR stops M2
(with memorization of the time) => At the same time countdown begins of the waiting
time before automatic closing (max 5 minutes).
6 - Press the PROG. button
=> Countdown of the waiting time before automatic closing
stops and M2 closes.
7 - Press the PROG. button
=> M1 closes thus establishing the interval between M2 and
M1. At the same time LED L9 will stop flashing, signalling exit from the learning
process. From this moment onwards the safety devices or other controls for the gate
will work normally (reversal, stops, alarms, etc....).
8 - Closure of the wings will be carried out at high speed and then upon approaching total
closure at low speed (depending on what has been set on the LOW SPEED trimmer).
9 - Upon reaching full closure the current sensors will stop the gate.
10 - AT THE END OF PROGRAMMING RETURN DIP 2 TO OFF.
Pag. 17 di 28
E
N
G
L
I
S
H
Summary of Contents for ABK0024
Page 4: ...I T A L I A N O Pag 4 di 28 COLLEGAMENTI ELETTRICI K2 24V Cod BC07059 K2 24V CRX Cod BC07058 ...
Page 16: ...Pag 16 di 28 K2 24V Code BC07059 K2 24V CRX Code BC07058 ELECTRIC CONNECTIONS E N G L I S H ...
Page 22: ...Pag 22 di 28 K2 24V Code BC07059 K2 24V CRX Code BC07058 ELEKTROANSCHLÜSSE D E U T S C H ...