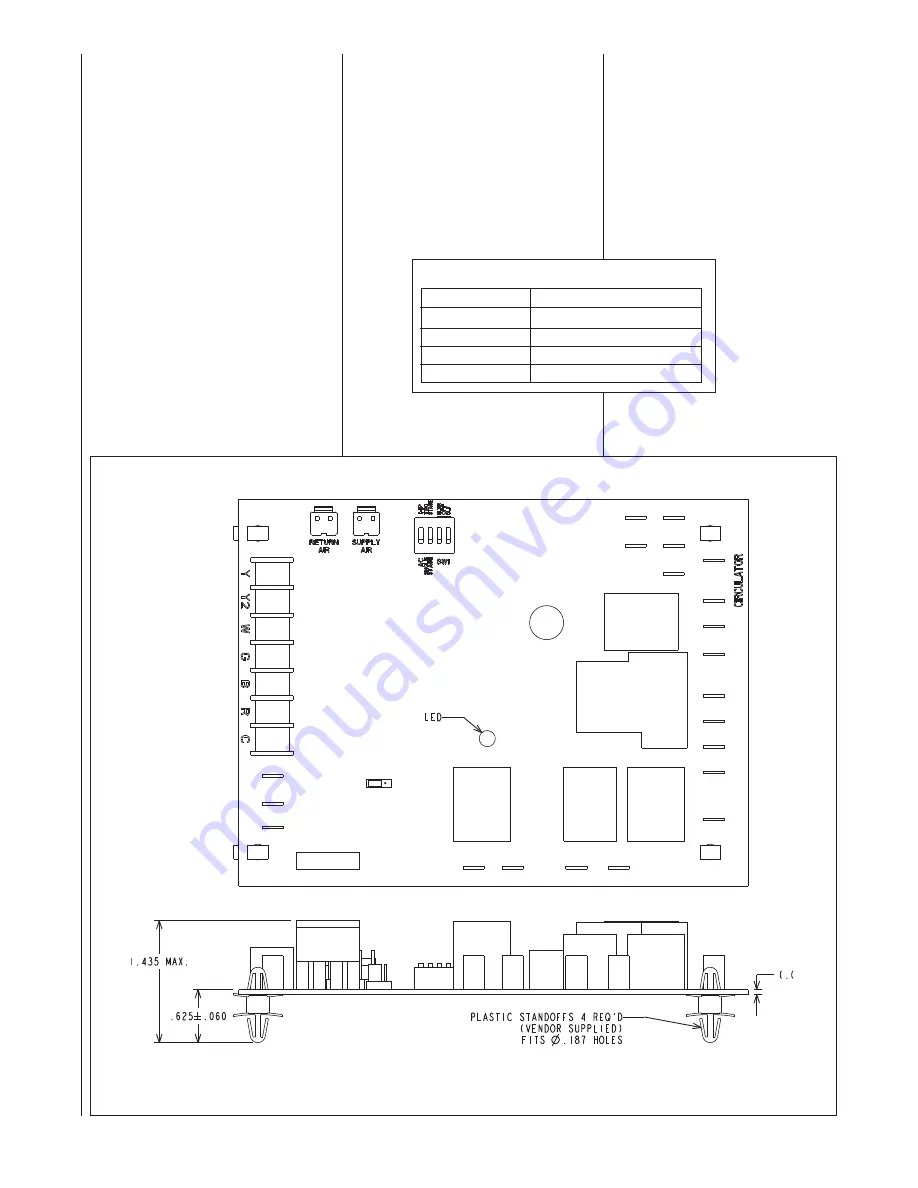
20
TABLE 1
System Low Voltage Wiring
Diagrams
NOTE:
Local codes may require
thermostat wiring to be routed through
conduit or raceways. In such instances
splices can be made inside the Hydronic
Air Handler. All wiring must be nEC
Class I and must be separated from
incoming power leads.
Provide field-supplied disconnect for
maximum fuse or circuit breaker sizes, as
required by code.
Transformer is factory wired for 115V
operation.
The secondary circuit of the transformer
is protected by a 3-amp fuse mounted on
the printed circuit board.
FIGURE 15
HYDRONIC AIR-HANDLER CONTROL BOARD (NON-MODULATING)
NOTES:
1. For proper operation of an open loop system (refer to Figures 11 and 17), the jumper (shunt) position on PCB point “P7” should be in
the FS position.
2. When changing shunt position ensure that unit power is turned off.
Wire Gauge Maximum Distance (feet)
18 gauge 60
16 gauge 100
14 gauge 160
12 gauge 250
Dip Switch Options:
Refer to the appropriate diagram for the
proper dip switch setting to be used with
the designed application (Figure 17).
THERMOSTAT INSTALLATION:
Thermostat should be mounted:
• approximately 5 ft. (1.5 m) from floor
• close to or in a frequently used
room, preferably on an inside,
partitioning wall
• on a section of wall without pipes
or duct work.
Thermostat should nOT be mounted:
• close to a window, on an outside
wall, or next to a door leading to
the outside.
Summary of Contents for RW1P
Page 29: ...29 FIGURE 21 ELECTRICAL WIRING DIAGRAM PSC MOTORS RW1P...
Page 32: ...32 FIGURE 24 ELECTRICAL WIRING DIAGRAM...
Page 33: ...33...
Page 34: ...34...
Page 35: ...35...
Page 36: ...36 CM 0617...