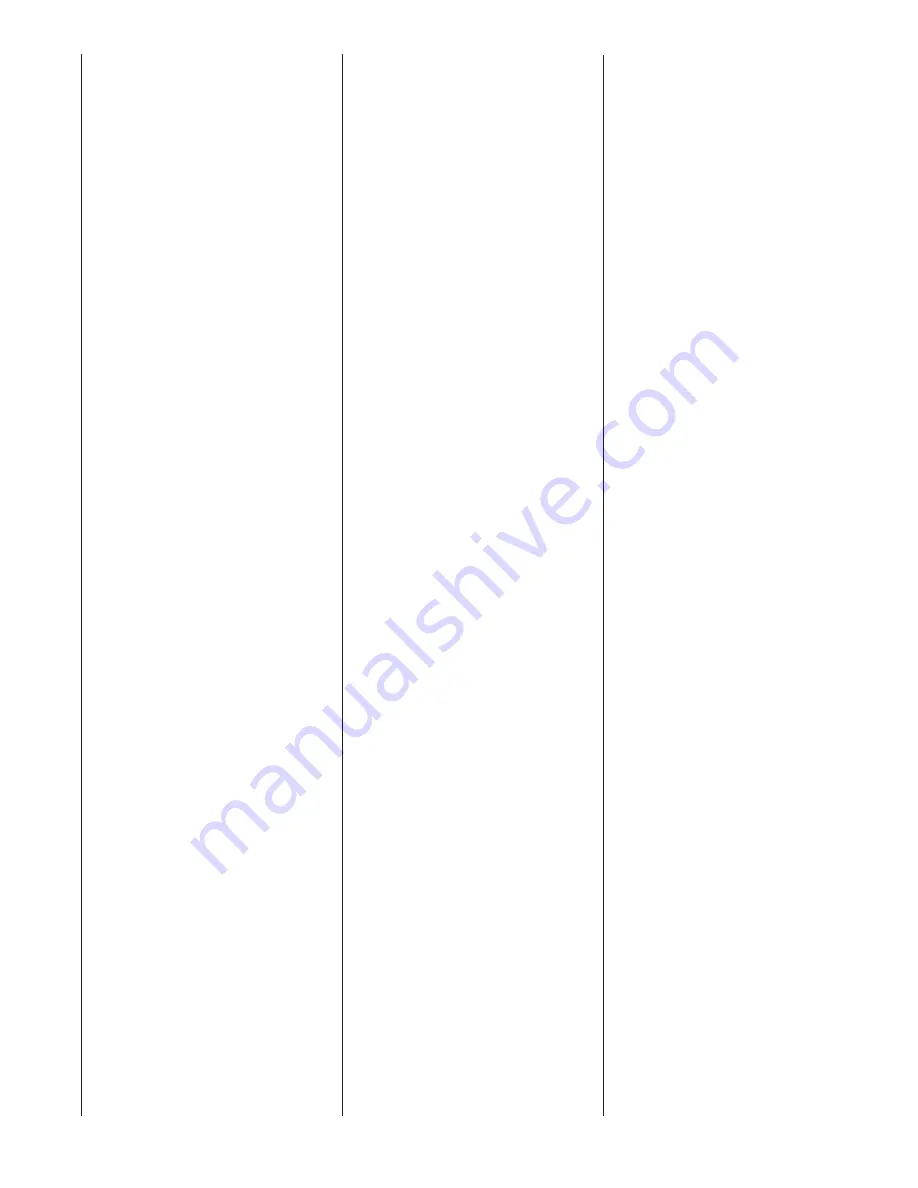
14
PLUMBING
Codes:
The RW1T air handler is used in potable
water systems. Therefore, it is important
to observe all local sanitary codes when
installing water lines. The water supply
mating connection to the Hydronic Air
Handler is made via the two 3/4 in. dia.
copper stubs labeled “WATER In” and
“WATER OUT” (see Figure 1).
All associated hydronic piping MUST
comply with ICC, UPC and any other
local codes or ordinances having
jurisdiction. USE POTABLE GRADE
COPPER PIPInG AnD BRASS
APPURTEnAnCES OnLY.
Soldering Copper Tubing:
The common method of joining copper
tubing in hydronic heating systems is
soft soldering. Plumbing codes do not
allow solders containing lead to be used
for domestic water service. USE OnLY
95/5 tin/antimony solder for all piping
systems that incorporate a domestic
water supply.
NOTE:
Precautions must be taken
during soldering to avoid debris or
solder from lodging in piping system.
Water Storage Tank:
When connecting directly to a water
storage tank it is necessary to ensure
the water flow rate does not become
excessive. Excessive water flow can
result in increased system noise and
potential system damage. In order to
regulate the flow it is required that an
adjustable valve be placed between the
air handler outlet and the storage tank
Rheem Accessory HC. Furthermore, two
pressure taps will need to be installed,
the first located between the air handler
outlet and the adjustable valve as near
as possible to the outlet, and the second
on the inlet water attached as near as
possible to the inlet. While the water
pump is engaged the adjustable valve
will be closed until the pressure
difference between the outlet and the
inlet is greater than 13.5 PSID.
Tubing Insulation:
Any tube-conveying fluid at a
temperature greater than that of the
surrounding air releases heat.
Insulate all accessible hot water lines
and associated valves with material,
such as expanded neoprene or
polyurethane 3/8-in. to 1⁄2-in. thick.
Match the pipe sleeve’s inside diameter
to the pipe’s outside diameter for a snug
fit. Place the pipe sleeve so the seam
will be face down on the pipe. Tape,
wire, or clamp insulation every foot or
two to secure it to the pipe. If taping is
desired, use acrylic tape instead of duct
tape.
Copper Tubing Support:
Copper tubing must be properly
supported to prevent sagging or
buckling. On horizontal runs with hard
temper tubing, the following maximum
support spacing is suggested:
• 1/2 in. to 3/4 in. tube: 5 feet maximum
spacing
• 1 in. to 1-1/4 in. tube: 6 feet maximum
spacing
The above suggested spacing does not
account for extra weight of piping
components such as an expansion tank,
etc. When such components are
present, the piping should be supported
immediately adjacent to the component.
On vertical runs, copper tubing should
be supported at each floor level or at a
maximum of every 10 feet.
Thermal Expansion of Piping:
In all hydronic systems, piping
undergoes temperature swings as the
system operates. This causes changes
in the length of the piping due to thermal
expansion.
If the piping is rigidly mounted, this
expansion can cause annoying popping
or squeaking sounds and, in extreme
cases, the piping can even buckle.
To counter expansion movement,
design piping circuits with sufficient
elbows, tees or expansion loops (only
used in large systems) or piping
supports that allow the tubing to expand
and contract freely.
Another alternative is to install an
expansion compensator fitting capable
of absorbing the movement.
Hydronic Resistance of
Fittings, Valves, and Other
Devices:
Before the total hydronic resistance
of a piping circuit can be found, the
individual hydronic resistances of all
fittings, valves, or other such
components must be determined.
One approach is to consider each
fitting, valve, or other device as an
equivalent length of copper tube of
the same pipe size (see Table 1).
By using the equivalent length of
piping for all components in the
circuit, the circuit can be treated as if
it were a single piece of pipe having
a length equal to the sum of the
actual pipe length, the total
equivalent lengths of all fittings,
valves, or other devices. Refer to
Figure 9 and the calculation of
equivalent lengths.
Pipe Sizing Considerations:
When selecting a pipe size for a
given flow rate, the resulting average
flow velocity should be between 2
and 4 feet per second.
At water flow velocities of
approximately 2 feet per second,
flowing water will carry air bubbles
along a vertical pipe. Average flow
velocities of 2 feet per second or
higher can draw along air bubbles in
a downward flow. At the above
stated velocities air bubbles shall be
routed to an air separator where they
can be collected and discharged from
the system. Use Taco 4900 series air
separator, Model 49-075, or
equivalent (field supplied).
Average flow velocities higher than 4
feet per second could cause flow
noise and should be avoided.
Expansion Tank:
All liquids used in hydronic heating
systems expand when heated. For
all practical purposes, liquids are
incompressible. Any container
completely filled with a liquid and
sealed from the atmosphere will
experience a rapid increase in
pressure as the liquid is heated.
To prevent this from occurring, all
closed-loop hydronic systems MUST
be equipped with an expansion tank.
Refer to expansion tank man u fac -
turer’s instructions for proper sizing
and installation.
Water circulation:
The hydronic air handler has a strict
in press cycle which will circulate the
water in the coil for 6 minutes per day
to prevent water stagnation.
Summary of Contents for RW1P
Page 29: ...29 FIGURE 21 ELECTRICAL WIRING DIAGRAM PSC MOTORS RW1P...
Page 32: ...32 FIGURE 24 ELECTRICAL WIRING DIAGRAM...
Page 33: ...33...
Page 34: ...34...
Page 35: ...35...
Page 36: ...36 CM 0617...