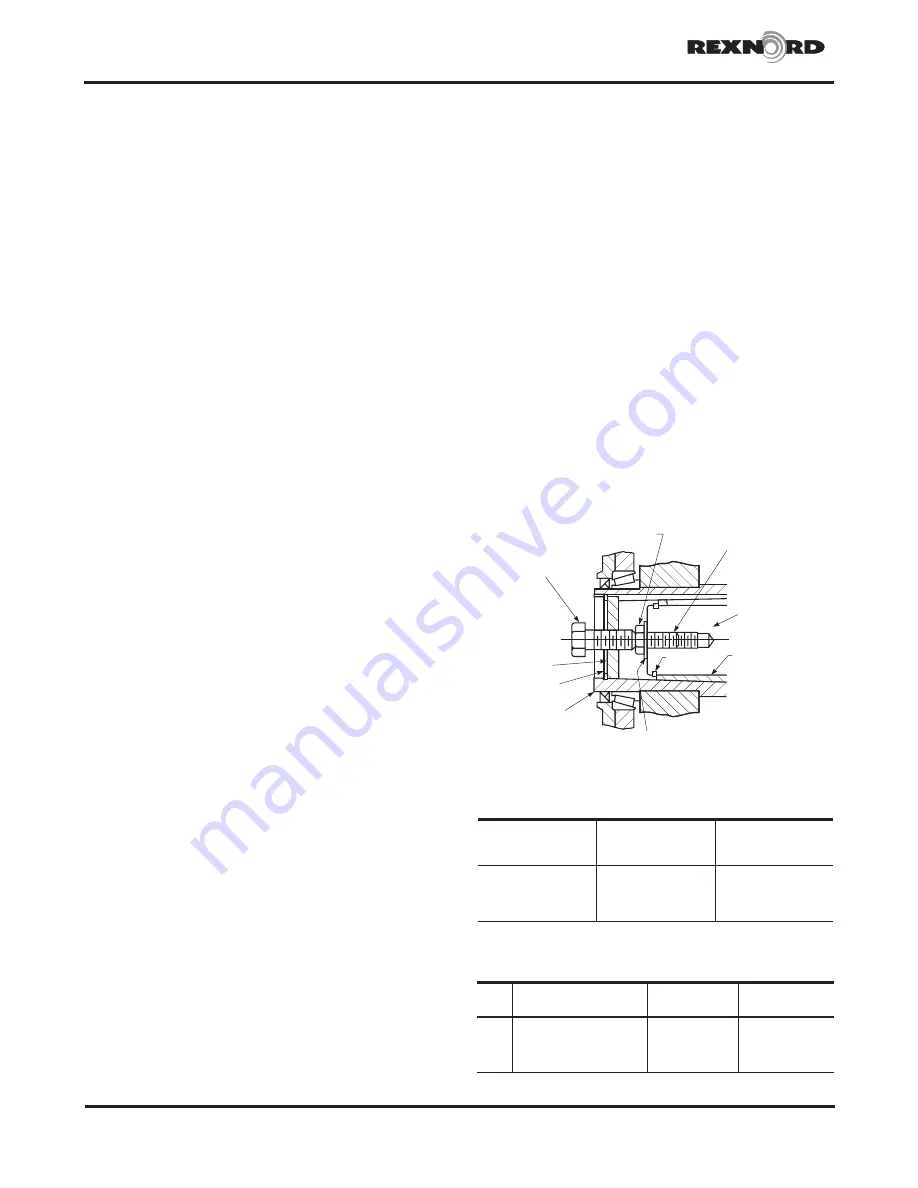
378-206
Rexnord
January 2019
3001 W. Canal St., Milwaukee, WI 53208-4200 USA
Supersedes 07-15
Telephone:
414-342-3131
Fax:
414-937-4359
www.rexnord.com
(PN-212395)
Appendix J
•
Falk Quadrive Shaft-Mounted Drives Model A
(Page 44 of 53)
Sizes 5407-5608
Drive Shaft Recommendations Using TA Taper Bushing
INTRODUCTION
— These instructions are for use when a
flange mounted 5407-5608JF drive is to be used and the
manufacture of a tapered drive shaft is not feasible . For
JF tapered drive shaft recommendations, see Appendix
H . Use this appendix to retrofit existing applications or for
outfitting new installations . Parts required are the drive, TA
Taper bushing and a thrust plate kit .
This appendix will allow the use of a straight drive shaft
with the tapered bushing (without spanner nut) on flange
mounted applications . Provided are dimensions (Table
4) for shaft recommendations and instructions for the
installation and removal of the assembly . All bushing bore
sizes, which are available in the standard Quadrive, are
possible with this setup .
FIGURE 2
— 5407-5608JF drives are furnished with a
flange adapter installed . The hollow shaft of the drive has
a tapered bore which accepts the tapered bushing . When
the bushing is drawn into the taper, a clamping force is
applied to the drive shaft . The drive shaft is drawn into the
hollow shaft via a fastener in the thrust plate . The bushing
seats against a shoulder on the driven shaft and is drawn
into the drive with the shaft . Removal is accomplished by
using a jackscrew in the thrust plate and forcing the drive
shaft out of the drive . The retaining ring in the drive shaft
assures that the bushing will be removed along with the
shaft .
DRIVE SHAFT RECOMMENDATIONS
— The
recommendations for the drive shaft consist of two major
features . The first is the shoulder which must be provided
in the location shown in Figure 2 . This shoulder provides
the backing necessary to draw the bushing into the
taper . A permanently fixed shoulder must be provided in
order for this design to be effective . The shoulder may
be a welded collar or an integral step . SET COLLARS
ARE NOT ACCEPTABLE . A retaining ring may be used,
in the driven shaft, to provide the shoulder, but stress
concentrations occur at the groove and therefore shaft
stresses must be checked . The second major feature on
the shaft is the retaining ring groove in the shaft end . This
feature is recommended to ensure positive removal of the
bushing when the drive shaft is removed from the drive .
The threaded hole in the end of the drive shaft accepts the
thrust plate fastener .
WARNING
: Lock out power source and remove all external
loads from system before servicing drive or accessories.
INSTALLATION PROCEDURE
— With the drive shaft
manufactured per the recommendations shown, and the
bushing selected for the proper shaft diameter, remove
and discard the retaining ring and spanner nut from the
bushing assembly .
5407JF
— Use of the tapered bushing requires that the
flange of the bushing be removed to clear the adapter,
Figure 2 . A flangeless bushing is available for the 3 .4375”
(87 mm) diameter shaft only .
ALL JF DRIVES
— Slide the bushing (flange end first)
onto the drive shaft until it contacts the shoulder on the
shaft . Insert the key through the bushing and into the drive
shaft keyway . Install the retaining ring into the groove in the
drive shaft . Bring the drive into position, line up the hollow
shaft keyway with the key and slide the bushing and drive
shaft into the hollow shaft bore .
Attach the drive to the mounting surface with fasteners (not
provided) . Refer to Table 1 for fastener size and tightening
torque . Assemble the thrust plate and retaining ring into
the counterbore in the hollow shaft . Insert the thrust plate
fastener through the thrust plate and thread into the drive
shaft end . Tighten to the torque given in Table 2 . Install all
covers and guards .
REMOVAL PROCEDURE
— Remove hollow shaft cover .
Remove the thrust plate fastener, retaining ring and thrust
plate from the hollow shaft . Refer to Table 3 and select
a backing bolt and flat washer and install them into the
drive shaft as illustrated in Figure 1 . The head of the
backing bolt provides a working surface for the removal
bolt . Reinsert the thrust plate and retaining ring into the
hollow shaft and select a removal bolt from Table 3 . Thread
the removal bolt into the thrust plate until it contacts the
backing bolt head . Tighten the removal bolt to the torque
indicated in Table 3 (If the thrust plate rotates in the shaft,
align the slot in the plate with the hollow shaft keyway
and insert a screw driver or piece of key stock to prevent
rotation of the plate) . After torquing the bolt, as instructed,
strike the bolt sharply with a hammer and retorque the
bolt if separation of the drive from the shaft did not occur .
Repeat this procedure, retorquing the bolt after each blow,
until separation occurs .
HOLLOW
SHAFT
THRUST
PLATE
RETAINING
RING
FLAT WASHER
TAPPED HOLE
IN DRIVE SHAFT
DRIVE SHAFT
RETAINING
RING
BUSHING
BACKING BOLT
REMOVAL
BOLT
Figure 1
Table 1 — JF Drive – Foundation Fastener &
Tightening Torque
(Non-Lubricated Fasteners)
Drive
Size
Fastener Size
& Grade
Max. Tightening
Torque
lb-ft (Nm)
5407
.750-10UNC, Grade 5
245 (332)
5415
1.250-7UNC, Grade 5
1050 (1424)
5507
1.250-7UNC, Grade 5
1050 (1424)
5608
1.500-6UNC, Grade 5
1842 (2497)
Table 2 — Thrust Plate Fastener Data
(Non-Lubricated Fasteners)
Drive
Size
Fastener Size & Grade
Max Tightening
Torque lb-ft (Nm)
Min Thread Depth
Inches (mm)
5407
1.000-8UNC x 5.50, Grade 8
792 (1073)
2.75 (69.8)
5415
1.250-7UNC x 6.00, Grade 8
1596 (2164)
3.00 (76.2)
5507
1.250-7UNC x 6.00, Grade 8
1596 (2164)
3.00 (76.2)
5608
1.250-7UNC x 8.00, Grade 8
1596 (2164)
3.50 (88.9)