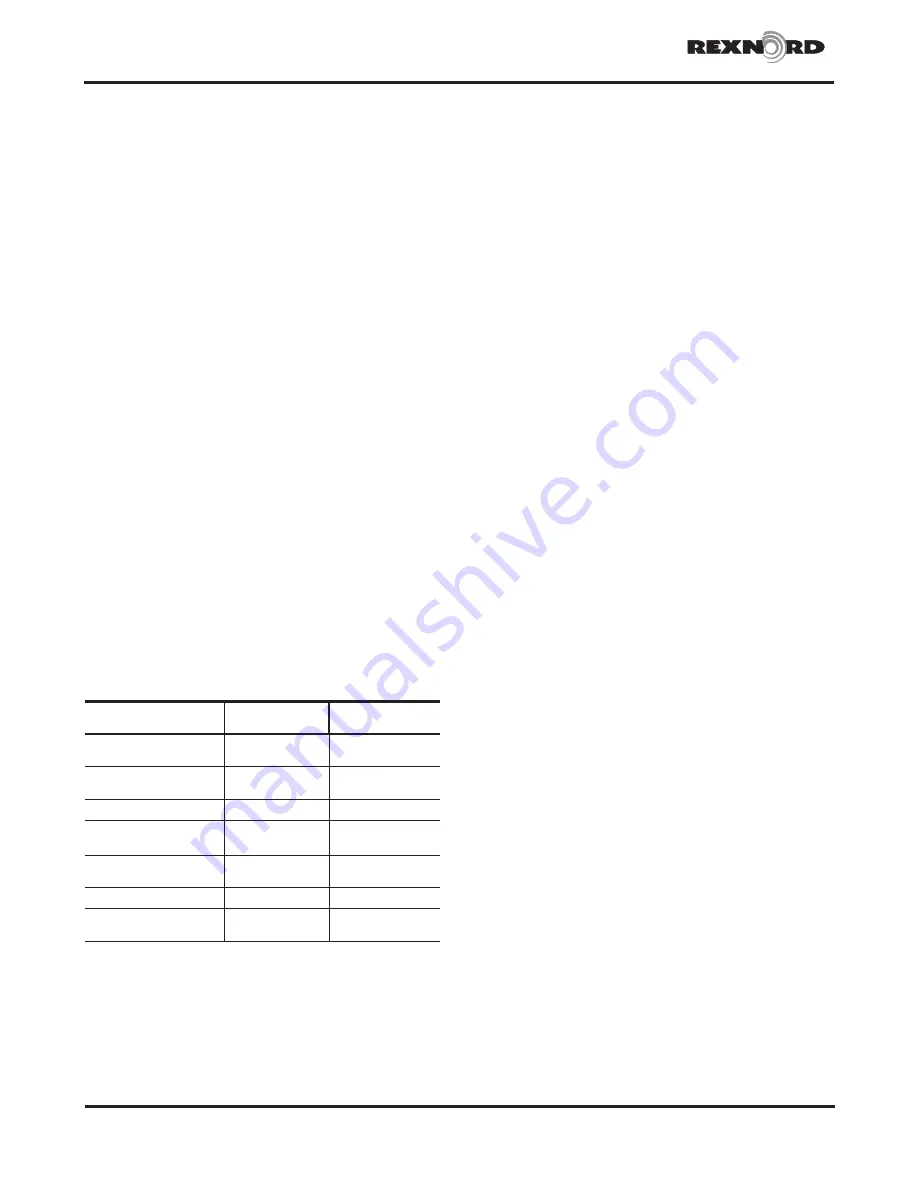
378-206
Rexnord
January 2019
3001 W. Canal St., Milwaukee, WI 53208-4200 USA
Supersedes 07-15
Telephone:
414-342-3131
Fax:
414-937-4359
www.rexnord.com
(PN-212395)
Appendix A
•
Falk Quadrive Shaft-Mounted Drives Model A
(Page 26 of 53)
Sizes 5407-5608
PETROLEUM LUBRICANTS —
In the absence of oil
analysis, change gear oils every 6 months or 2500 operating
hours, whichever occurs first . Change oil more frequently
when gear drives operate in extremely humid, chemical or
dust laden atmospheres . In these cases, lubricants should
be changed every 3 to 4 months or 1500 to 2000 hours . If
the drive is operated in an area where temperatures vary
with the seasons, change the oil viscosity grade to suit the
temperature, refer to Table 3 . Lubricant suppliers can test
oil from the drive periodically and recommend economical
change schedules .
SYNTHETIC LUBRICANTS —
In the absence of oil
analysis, synthetic lube change intervals can be extended
to 8000 hours depending upon operating temperatures .
Laboratory analysis is recommended for optimum lubricant
life and drive performance . Change lube with change in
ambient temperature, if required . Refer to Table 4 .
Falk GMax 6000
change interval can be up to 15,000
hours . It has broad temperature range so seasonal oil
changes are generally not needed . The condition of GMax
must be monitored to maintain lubricant properties and
cleanliness .
GREASE-LUBRICATED SEALS
All drives are furnished with grease purged seals which
minimize the entry of contaminants and abrasive dusts into
the drive . Drives are shipped with NLGI #2 grade grease in
the seal housing cavities unless otherwise specified .
Whenever changing oil in the drive, purge the seals
with one of the NLGI #2 grade greases listed in Table 7 .
Depending upon the degree of contamination, it may be
necessary to purge contaminated grease from seals more
often (at least every 3 to 6 months) . Slowly pump fresh
bearing grease through the seal,
WITH HAND GREASE
GUN,
until fresh grease flows out along the shaft . Wipe off
purged grease .
WARNING:
Greases in Table 7 contain harmful substances
not allowed in the food processing industry. If grease
could contaminate the product, as in the food and drug
industries, the grease originally supplied with gear drive
must be removed and replaced with grease listed in Table
14. Refer to gear drive assembly/disassembly instructions.
Simply purging grease with grease gun will not remove all
grease and cross-contamination will likely occur. Grease
registered as H1 by NSF, National Sanitation Foundation, is
suitable for food processing applications.
STORED & INACTIVE GEAR DRIVES
Refer to Section II (Drive Service and Repair) for details on
stored & inactive gear drives .
Grease application or re-lubrication should be done at temperatures
above 20°F (-7°C) . If grease must be applied at cooler temperatures
consult lubricant supplier for recommendations .
TABLE 7 —
Conventional NLGI #2 Grade
Grease
for Grease Purged Seals
0° to +200°F (-18° to +93°C)
Manufacturer
EP Grease
n
Grease Without
EP Additives
Chevron / Texaco /
Caltex
Multifak EP 2
- - -
Citgo Petroleum Corp.
Lithoplex RT 2
Premium Lithium EP 2
- - -
ExxonMobil / Esso
Mobilux EP 2
Unirex N2
Petro-Canada
Lubricants
Precision General
Purpose EP2
Precision XL EMB Grease
Precision Synthetic EMB
Phillips 66 / Conoco /
76 Lubricants / Kendall
Multiplex Red
- - -
Shell Oil Co.
Gadus S1 V220-2
Gadus S2 V100 - 2
Total Lubricants USA /
Keystone Div. Penwalt Corp.
Multis EP 2
Multis 2
s
Not suitable for food grade applications .
n
Caution: Do not use EP grease in external backstop purged seals .