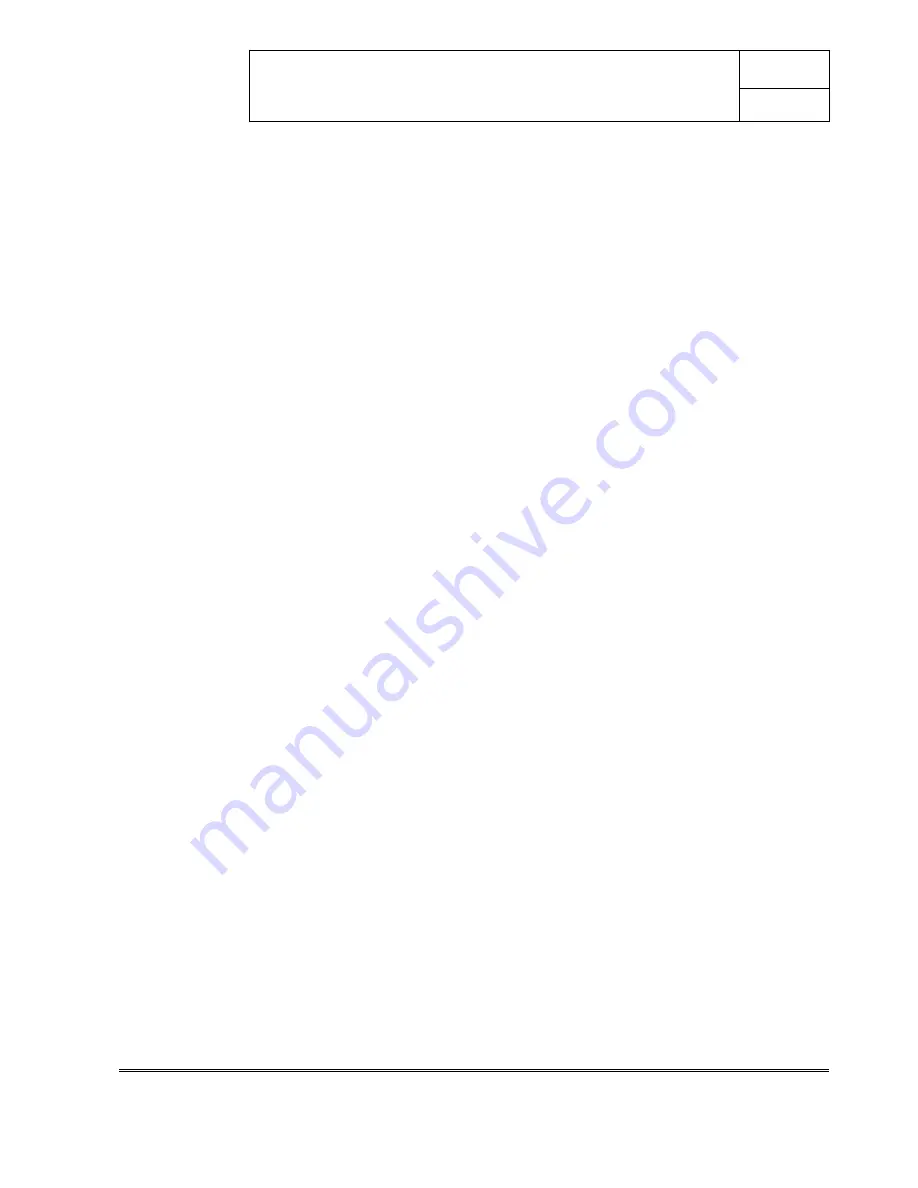
red
TECNIKA 28-35
USE AND INSTALLATION MANUAL
Chapter
2
page 6
Guarantee term
Technical dept. - All rights reserved - Reproduction prohibited
The guarantee does not cover:
1.
Damage made by atmospheric agents, chemicals, electrochemical elements, incorrect product use,
natural disasters, electrical discharges, fires, faults in the electrical system, modifications to or
tampering with the product, and/or other causes not ensuing from the product manufacturing
2.
Damage caused by normal corrosion
3.
Damage relating to the combustion chamber
4.
Damage to seals, claddings, painted/chromed parts, handles and electrical wires
5.
Damage to masonry work
6.
Damage to parts of the system for the production of DHW not supplied by RED
7.
Damage to the heat exchanger if a suitable condensation-proof circuit is not set up to guarantee a
minimum boiler return temperature of at least 55 °C.
8.
Servicing for calibration or product adjustments
9.
Incorrect or negligent use.
10.
All damage caused by transport; we consequently advise you to check the goods carefully upon
receipt, notifying your retailer immediately of any damage, making a note on the delivery note and
on the copy that travels with the carrier.
Please contact your retailer and/ or local importer in the event of product failure.
RED will not be held liable for any damage which may - either directly or indirectly - be caused to property,
or personal injury or harm to animals ensuing from failure to observe all the instructions provided herein and
the applicable regulations regarding installation, use and maintenance of the appliance.
The parts replaced will be guaranteed for the remaining guarantee cover period starting from the original
date of purchase of the product.
2.3.
Additional clauses
If faulty or malfunctioning parts are detected during normal product use, these will be replaced free of
charge ex retailer who made the sale or ex our local technical service centre.
For products sold abroad, the same circumstances will again result in free replacement, ex our retailer, with
the exception of specific conditions agreed upon at the time of negotiations with the foreign distributor.
In the case of replaced parts, the guarantee will not be extended.
No damages are awarded for the product downtime period.
This is the only applicable guarantee and no-one is authorised to provide any other guarantees in the name
of or on behalf of RED.
2.4.
Liability
RED will not pay any compensation for direct or indirect damage caused by or dependent upon the product.
2.5.
Court with jurisdiction
In the event of any controversy, the court with jurisdiction is the Court of Pordenone (Italy).
2.6.
Liability exclusion
The manufacturer is not able to supervise the observance of the instructions provided in this manual. Nor is
it able to monitor the conditions and methods of installation, operation, use and maintenance of the product.
Incorrect installation could cause damage and endanger persons. Consequently, we cannot be held in any