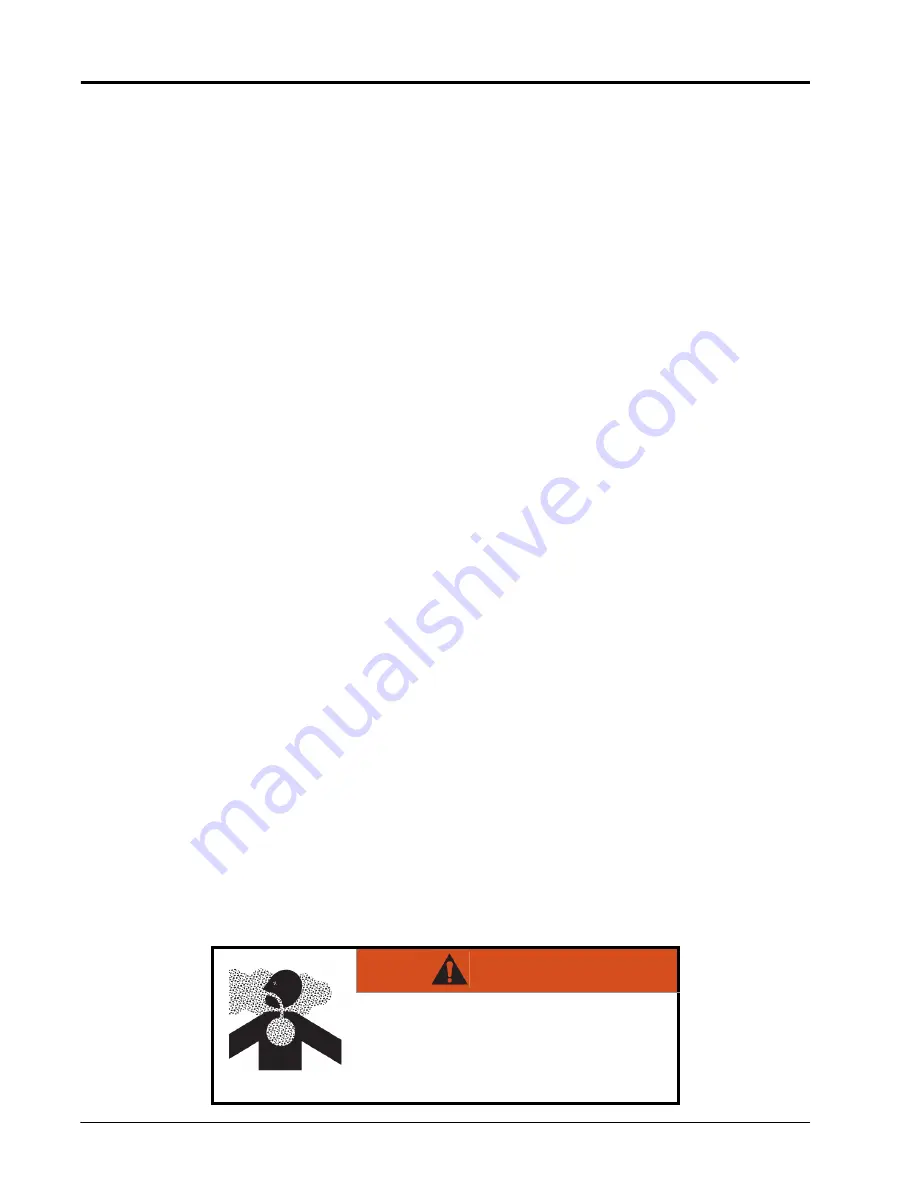
A
PPENDIX
F
108
ISO Product Controller II and Hawkeye Operation Manual
completed, the ISO icon at the top right of the screen will be green. Hawkeye nozzle control valves must be
properly indexed for this to work.
8. Inspect the status of the overlap control unlock. Temporary unlock is usually active upon start-up but a
permanent unlock purchase is required to ensure proper overlap control operation.
9. Ensure the alarm indicator is green. Red indicates a serious error condition that will prevent the system from
spraying. Yellow alarm indicates a warning that requires investigation but will not prevent spraying. Clear all
conditions as necessary.
10. Enter a test speed in the UT mode. The boom section switches on the vehicle should respond with the
corresponding boom section icons in the UT window. No triangle indicates that the boom is off. an empty
triangle indicates the boom is active but is being controlled by Accuboom. A triangle that is filled in blue
indicates the boom is spraying. The nozzle control valves should click of operating properly. Expect a pump
pressure error because the pump is not running.
NOTE:
With water in the tank this step can be performed with the engine running. Do not run the pump for
an extended period of time with no liquid in the tank because this may damage the seals.
11. Start a job. Ensure that all necessary widgets are available to the operator to allow proper machine operation.
Make a copy for the complete widget setup for the operator to modify.
12. In job view mode, enter a test speed. Verify that the section control is off. The boom section switches should
respond to the corresponding boom sections in the UT window. No triangle means the boom is off. An empty
triangle indicates the boom is active but is being controlled by Accuboom. A triangle filled in blue means the
boom should be spraying. Expect a pump pressure error since the pump is not running. if the booms do not
respond correctly, delete and import the boom settings.
NOTE:
With water in the tank this step can be performed with the engine running. Do not run the pump for
an extended period of time with no liquid in the tank because this may damage the seals.
13. After all systems are functions properly, will the tank with water and complete the functional inspection.
FUNCTIONAL INSPECTION
Refer to the following sections for assistance with validating that the Hawkeye nozzle control system has been
installed properly:
NOZZLE CONTROL VALVE FUNCTION
To verify that the Hawkeye nozzle control system is functioning properly after installation:
1. Flush the main product tank and boom plumbing with clean water, and verify the tank contains at least 100
gallons [379 L] of clean water.
2. Park the equipment in an area with enough space to unfold the booms and allows for visual inspection of the
spray pattern from a moderate distance (e.g. 20 ft [6.1 m]).
3. Set the Hawkeye nozzle control system to manual mode, and set both the pump PWM and nozzle PWM to
50%. Refer to the ± Bump section on page 43 for assistance with adjusting the PWM percent values in the
manual control mode.
4. Toggle all section switches and the master switch.
WARNING
Equipment will begin spraying. Avoid inhaling
spray particulate and avoid direct contact with
any agricultural chemicals. Seek immediate
medical attention if symptoms of illness occur
during, or soon after, use of agricultural
chemicals, products, or equipment.
Summary of Contents for ISO Product Controller II
Page 10: ...CHAPTER 1 viii ISO Product Controller II and Hawkeye Operation Manual...
Page 16: ...CHAPTER 1 6 ISO Product Controller II and Hawkeye Operation Manual...
Page 22: ...CHAPTER 2 12 ISO Product Controller II and Hawkeye Operation Manual...
Page 50: ...CHAPTER 4 40 ISO Product Controller II and Hawkeye Operation Manual...
Page 92: ...APPENDIX A 82 ISO Product Controller II and Hawkeye Operation Manual...
Page 95: ...P N 016 0171 584 H 85 FIGURE 3 Generic Cabling for Self Propelled Sprayer...
Page 97: ...P N 016 0171 584 H 87 FIGURE 5 Generic Cabling for Pull Type Sprayer with Existing Raven CAN...
Page 99: ...P N 016 0171 584 H 89 FIGURE 7 20 Spacing Generic Cabling...
Page 111: ...P N 016 0171 584 H 101...
Page 112: ...APPENDIX D 102 ISO Product Controller II and Hawkeye Operation Manual...
Page 116: ...APPENDIX E 106 ISO Product Controller II and Hawkeye Operation Manual...
Page 120: ...APPENDIX F 110 ISO Product Controller II and Hawkeye Operation Manual...
Page 128: ...APPENDIX G 118 ISO Product Controller II and Hawkeye Operation Manual...
Page 134: ...APPENDIX H 124 ISO Product Controller II and Hawkeye Operation Manual...