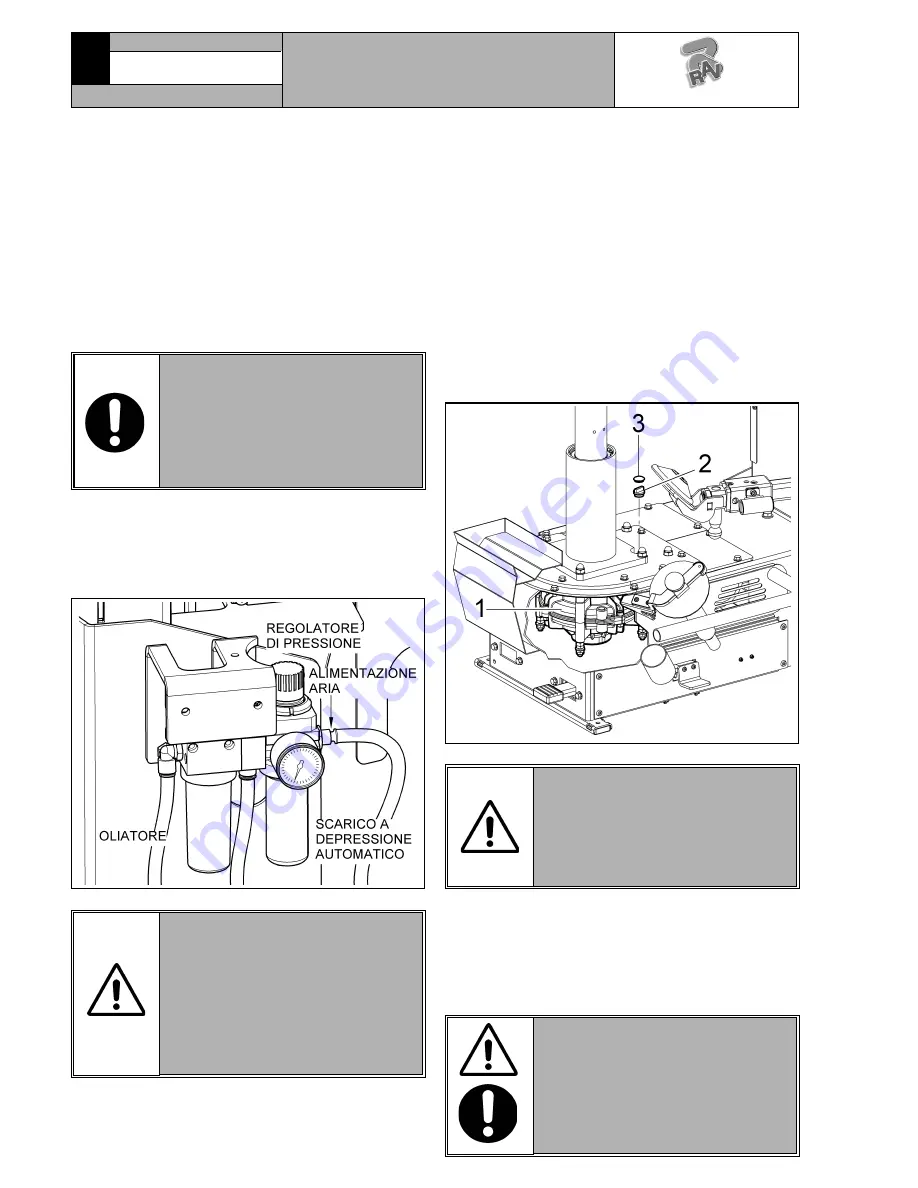
GB
Page 25 of 32
INSTRUCTION, USE AND
MAINTENANCE MANUAL
G1150.30MAGIC - G1150.30MAGICIT
RAVAGLIOLI S.p.A.
7107-M001-0_R
Fig. 51
Fig. 50
• Periodically, with a frequency of at least once a month,
lubricate the arms of the bead breaking roller and of
the tools.
13.0 ROUTINE MAINTENANCE
To guarantee the efficiency and correct functioning of the
machine, it is essential to carry out daily or weekly clean-
ing and weekly routine maintenance, as described be-
low.
Cleaning and routine maintenance must be conducted
by authorized personnel and according to the instruc-
tions given below.
• Disconnect the mains power supply before starting
any cleaning or routine maintenance operations.
• Remove deposits of tyre powder and other waste ma-
terials with a vacuum cleaner.
DO NOT BLOW IT WITH COMPRESSED AIR
.
• Do not use solvents to clean the pressure regulator.
• The conditioning unit is equipped with an automatic
vacuum-operated drain therefore it requires no manual
intervention by the operator (see
Fig. 50
).
IN ORDER TO ALLOW A LONGER
LIFE OF THE FILTER AND OF ALL
MOVING PNEUMATIC DEVICES,
YOU HAVE TO MAKE SURE THAT
THE SUPPLIED AIR IS:
• EXEMPT FROM THE LUBRICATING
OIL OF THE COMPRESSOR;
• EXEMPT FROM HUMIDITY;
• EXEMPT FROM IMPURITY.
THE MANUFACTURER DOES NOT
ACCEPT ANY DAMAGE RESULTING
FROM THE FRAILURE TO OBSERVE
THE ABOVE INSTRUCTION, AND
SUCH FAILURE COULD INVALIDATE
THE WARRANTY!!
BEFORE CARRYING OUT ANY MAIN-
TENANCE OPERATIONS, MAKE
SURE THERE ARE NO WHEELS
CLAMPED ON THE CHUCKING TA-
BLE AND THAT ALL SUPPLIES TO
THE MACHINE HAVE BEEN DIS-
CONNECTED.
13.1 Lubricants
Special lubricant for spindle movement control gearbox.
Use
ESSO GEAR OIL GX140
.
Lubricate slides, screws/nut screws or racks and pin-
ion with a soft brush using lubricant of
ESSO GP
type.
ANY DAMAGE TO THE MACHINE
DEVICES RESULTING FROM THE
USE OF LUBRICANTS OTHER THAN
THOSE RECOMMENDED IN THIS
MANUAL WILL RELEASE THE
MANUFACTURER FROM ANY LI-
ABILITY.
• Immediately replace worn parts, bead breaking roller,
assembly tools.
• Every
week
and/or when necessary, top up the oil tank
using the filler hole provided closed by a cap or screw
on the lubricator filter.
N.B: This operation should not be carried out by
unscrewing the cup of the lubricator filter.
• The use of synthetic oil might damage the pressure
regulator filter.
• At regular intervals, (at least every 100 working hours)
check reduction gear (
Fig. 51 pos. 1
) lubricating oil
level. Such operation must be effectuated removing the
plug (
Fig. 51 pos. 3
), positioned on the provided hole
prearranged on the frame, and removing the plug po-
sitioned on reduction gear (
Fig. 51 pos. 2
).