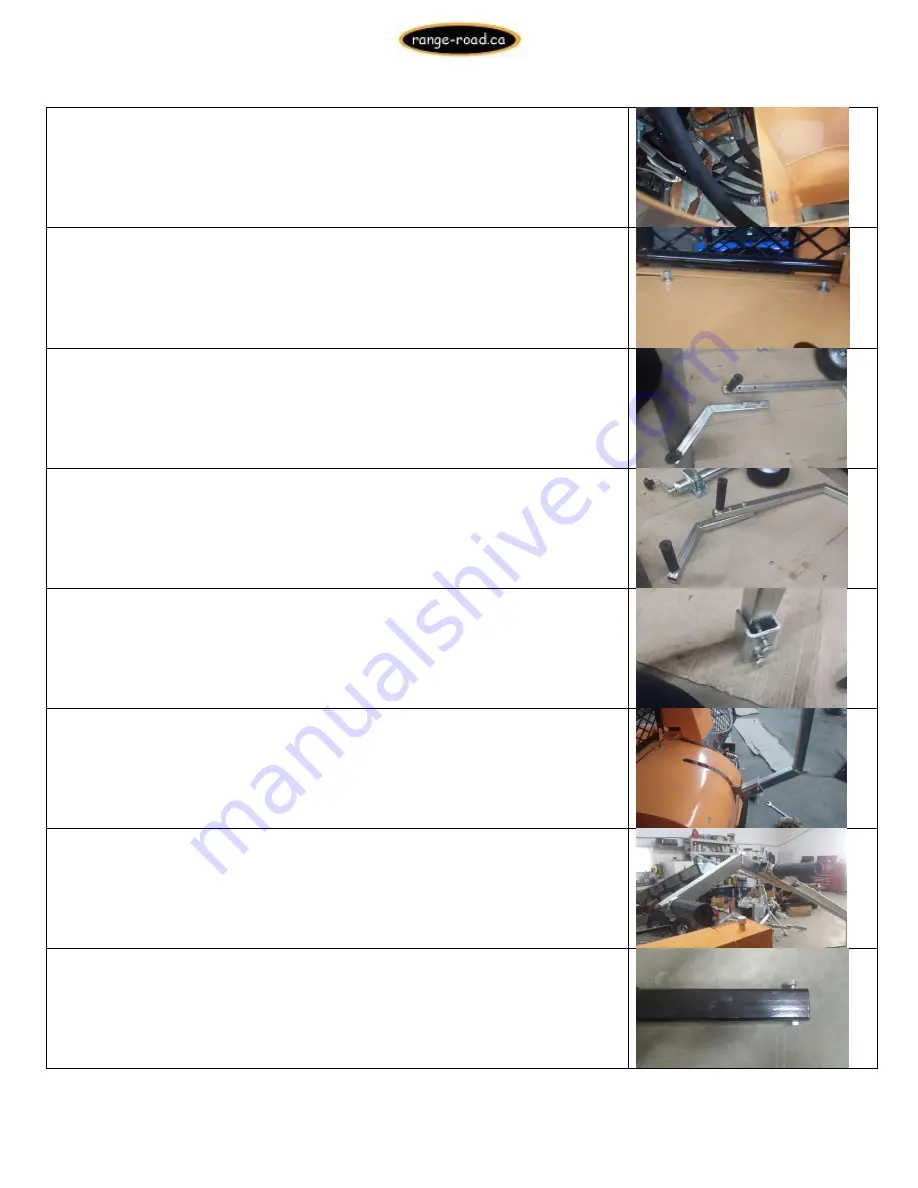
RR27T
Range Road Enterprises Ltd
Box 944
Eckville AB T0M 0X0
www.range-road.ca
Page 12
56.) Install 10mm Bolt & Nut in side of sawdust cover
57.) Install 2 Allan head bolts ion top of cover, tighten all bolts
58.) Remove 2 – 13mm Bolts & Nuts from chainsaw engagement arm
extension
59.) Attach extension to drawbar and tighten 13mm bolts
60.) Remove 2 – 13mm Bolts, Nuts & Bracket from bottom of engagement
arm
61.) Put engagement arm in place, install bracket and 2 – 13mm Bolts &
Nuts, Tighten
Install Handle Extension if needed
62.) Remove 16mm bolt x 17mm nut from drawbar