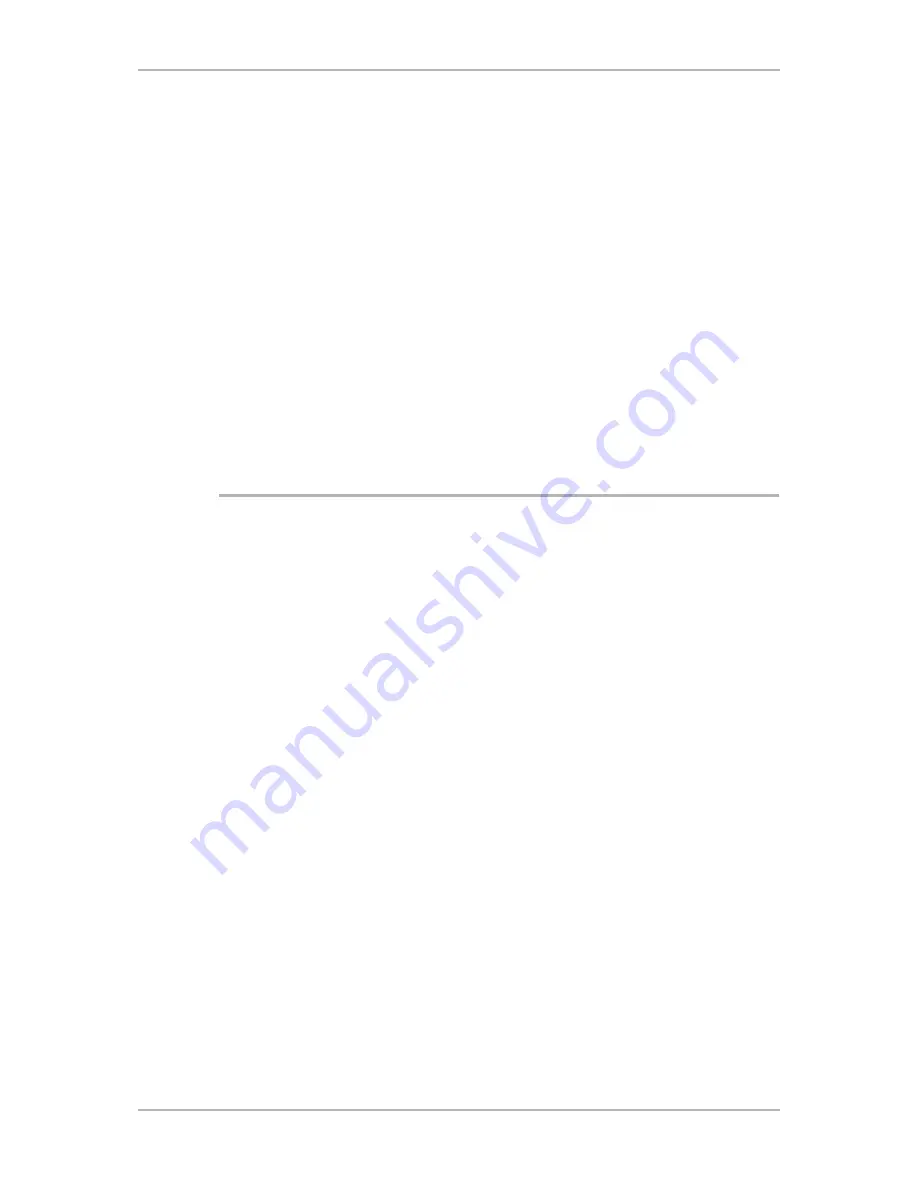
MAINTENANCE - Page 51
© 2005 SANDVIK TAMROCK CORP.
Troubleshooting
S 83 STD
EXCESSIVE BACK PRESSURE IN RETURN LINE
Check the installation. Check the size of the return line.
RELIEF VALVE IN HYDRAULIC CIRCUIT OPENS AT A LOW PRESSURE. HAMMER OPERATING
PRESSURE IS NOT REACHED
Check the installation. Check the relief valve operation. Adjust the relief valve in
hydraulic circuit. Measure the high pressure in the hammer inlet line. Contact your
local dealer for more information.
LEAKAGE FROM PRESSURE TO RETURN IN EXCAVATOR HYDRAULIC CIRCUIT
Check the installation. Check the pump and the other hydraulic components.
PRESSURE LOSS IN PRESSURE ACCUMULATOR
The hammer must be serviced in an authorized Rammer service shop.
FAILURE IN HAMMER VALVE OPERATION
The hammer must be serviced in an authorized Rammer service shop.
4.5 THE HAMMER DOES NOT STOP OR HAS RUN-ON
INTERNAL LEAKAGE IN THE HAMMER
The hammer must be serviced in an authorized Rammer service shop.
FAILURE IN HAMMER CONTROL VALVE OPERATION
Check the hammer control valve in the carrier.
Summary of Contents for S 83 STD
Page 1: ...3 05 OPERATION AND MAINTENANCE OMS83SENG 305 HYDRAULIC HAMMER RAMMER S 83 STD ...
Page 3: ...OPERATION Page 3 2005 SANDVIK TAMROCK CORP S 83 STD OPERATION ...
Page 30: ... 2005 SANDVIK TAMROCK CORP Page 30 OPERATION Operation S 83 STD ...
Page 31: ...LUBRICATION Page 31 2005 SANDVIK TAMROCK CORP S 83 STD LUBRICATION ...
Page 39: ...MAINTENANCE Page 39 2005 SANDVIK TAMROCK CORP S 83 STD MAINTENANCE ...
Page 53: ...SPECIFICATIONS Page 53 2005 SANDVIK TAMROCK CORP S 83 STD SPECIFICATIONS ...