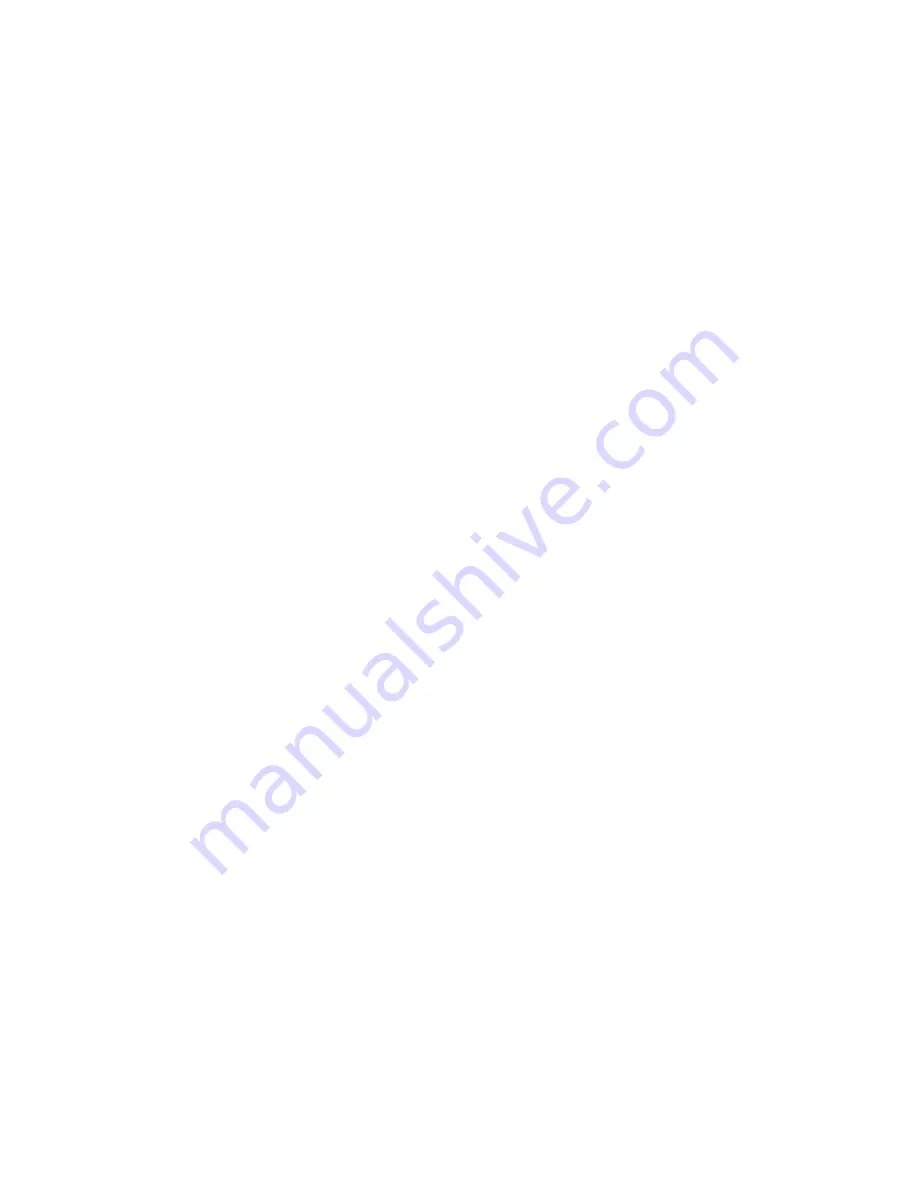
Installation Manual
Combi - cod. 99943NA – November 2002
4
GENERAL INSTALLATION REQUIREMENTS
GAS SAFETY
It is the law that all gas appliances are installed by a CORGI registered installer (you can check this by contacting corgi on 01256.372200) in
accordance with the regulations listed below. Failure to install appliances correctly could lead to prosecution. It is in your own interest and
that of safety to ensure that the law is complied with. Failure to have your appliance installed to comply with the installation instructions and
the requirements listed below could invalidate your guarantee.
RELATED DOCUMENTS
The installation of the boiler must be in accordance with the relevant requirements of the Gas Safety regulations, Building regulations, I.E.E.
regulations and the bylaws of the local water authority.
It should be in accordance also with any relevant requirements of the local authority and the relevant recommendations of the following
British Standard Codes of Practice:
B.S 6400:
1985 & B.S. 6891 : 1988.
BS 5376:
Selection and Installation of Gas Space Heating ( 1 and 2 family gases)
Part 2: Boilers of rated input not exceeding 60 Kw
BS 5449:
Central Heating for domestic premises
Part 1: Forced circulation Hot Water System
CP 342:
Centralised Hot Water Supply BS 6700 :
1987
Part 2: Buildings other than individual
BS 5440:
Flues and air supply for Gas Appliances of rated input not exceeding
60 Kw (1 and 2 family gases)
Part
1:
Flues
Part 2: Air Supply
BS 5446:
1990: Installation of Gas Hot Water supplies for domestic purposes
GAS SUPPLY
Service Pipes: The local gas region should be consulted at the installation planning stage in order to establish the availability of supply of
gas. An existing service pipe must not be used without prior consultation with the local gas region.
Meters: A gas meter is connected to the service pipe by the local gas region or local gas region contractor. An existing meter should be
checked to ensure that it is capable of passing an additional 3.4 m3/hr (125 ft/hr) before the appliance is installed. The meter outlet
governor should ensure a nominal dynamic pressure of 20m Bar, (8 in wg) at the boiler. Installation pipes should be fitted in accordance
with BS6891.1988.
Pipework that supplies the boiler must be a 22 mm. ininterrupted supply from meter to the isolation cock of the
boiler.
The complete installation must be tested for soundness as described in the above code, BS 6400: 1985 & BS6891.
IMPORTANT: BOTH THE USER AND THE MANUFACTURER RELY UPON THE INSTALLER, WHOSE JOB IS TO INSTALL THE BOILER
AND CONNECT IT TO A CORRECTLY DESIGNED HEATING SYSTEM. THE INSTALLER SHOULD ACQUAINT HIMSELF WITH THE
CONTENTS OF THIS PUBLICATION AND THE RELEVANT BRITISH STANDARDS CONCERNING INSTALLATION REQUIREMENTS.
LOCATION OF BOILER
In siting the combination boiler, the following limitations MUST be observed:
The position selected for installation should be within the building, and MUST allow
adequate space for installation, servicing and operation of the combination boiler, and for air circulation around it. The boiler is not suitable
for external installation.
This position MUST also allow for a suitable flue termination to be made. The boiler must be installed on a flat vertical wall which is capable
of supporting the weight of the combination boiler, and any ancillary equipment.
If the boiler is to be fitted in a timber framed building it should be fitted in accordance with the British Gas publication "Guide for Gas
Installations in Timber Frame Housing, Reference IGE/UP/6. If in doubt, advice must be sought from the local region of British Gas.
The boiler may be installed in any room or internal space, although particular attention is drawn to the requirements of the current I.E.E.
Wiring Regulations, and in Scotland the electrical provisions of the Building Regulations applicable in Scotland, with respect to the
installation of the boiler in a room or internal space containing a bath or shower.
Where a room-sealed appliance is installed in a room containing a bath or shower, any electrical switch or appliance control utilising mains
electricity must be so situated that it cannot be touched by a person using the bath or shower.
A compartment used to enclose the combination boiler MUST be designed and constructed specifically for this purpose. An existing
cupboard, or compartment, may be used provided it is modified accordingly.
Where installation will be in an unusual location, special procedures may be necessary. BS 6798 gives detailed guidance on this aspect.
For clearances to be made available for installation and servicing, see Sections 5.2.2. to 5.2.4.
Summary of Contents for RSF 24 E
Page 2: ......