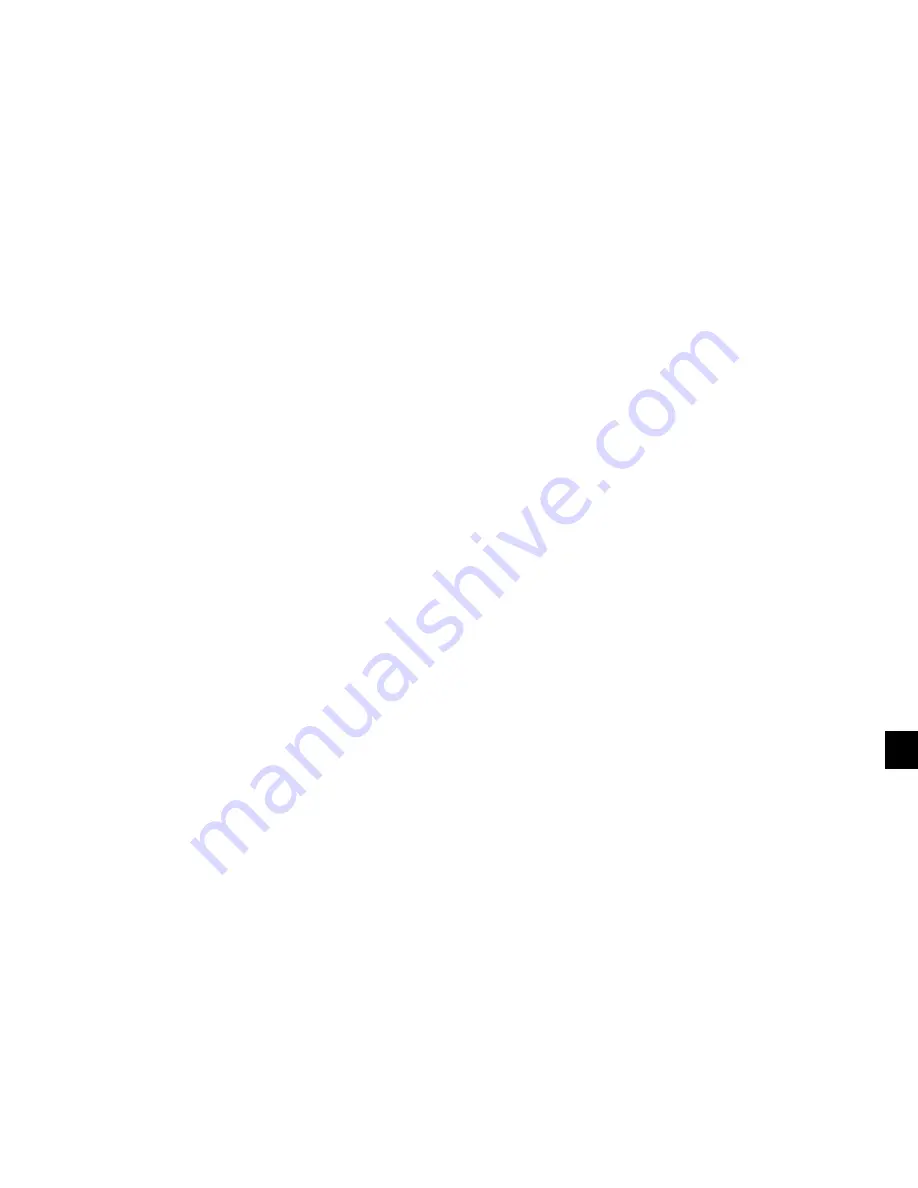
161
QUANTECH
FORM QTC3-NM1
ISSUE DATE 08/03/2022
SECTION 8 – UNIT OPERATION
8
As an example of compressor staging (see
), a chiller with six compressors using a
Cooling Setpoint programmed for 45°F (7.20°C) and a
Range Setpoint of 10 °F (5.56 °C). Using the formulas
in
, the control range will be
split up into six (seven including hot gas) segments,
with the Control Range determining the separation be-
tween segments. Note also that the Cooling Setpoint is
the point at which all compressors are OFF, and Cool-
ing Setpoint plus Range is the point all compressors
are ON. Specifically, if the return water temperature is
55°F (12.8°C), then all compressors will be ON, pro-
viding full capacity. At nominal gpm, this would pro-
vide approximately 45°F (7.2°C) leaving water tem-
perature out of the evaporator.
If the return water temperature drops to 53.4°F (11.9°C),
one compressor would cycle OFF leaving five com-
pressors running. The compressors would continue to
cycle OFF approximately every 1.7°F (.94°C), with the
exception of hot gas bypass. Notice that the hot gas
bypass would cycle ON when the return water tem-
perature dropped to 46.25°F (7.9°C). At this point one
compressor would be running with hot gas.
Should the return water temperature rise from this point
to 46.7°F (8.2°C), the hot gas bypass would shut OFF,
still leaving one compressor running. As the load in-
creased, the compressors would stage ON every 1.7°F
(0.94°C).
Also note that
not only pro-
vides the formulas for the loading (ON POINT) and
unloading (OFF POINT) of the system, the “STEP” is
also shown in the table. The “STEP” is the increment
in the sequence of the capacity control scheme that can
be viewed under the OPER DATA key. See
the OPER DATA key.
RETURN CHILLED LIQUID SYSTEM LEAD/
LAG AND COMPRESSOR SEQUENCING
A Lead/Lag option may be selected to help equalize
average run hours between systems with 2 refriger-
ant systems. This may be programmed under the OP-
TIONS key. Auto Lead/Lag of the 2 systems based on
average run hours of the compressors in each system.
Manual Lead/Lag selects specifically the sequence
which the microprocessor starts the systems.
The microprocessor will sequence compressors load
and unload systems according to
. The microprocessor will lead/lag compressors
within each circuit to maximize individual compres-
sor run time for the purpose of lubrication. It will also
prevent the same compressor from starting 2 times in
a row. The microprocessor will not attempt to equalize
run time on individual compressors within a system.
Each compressor in a system will be assigned an ar-
bitrary number 1, or 2. The non-running compressor
within a system with the lowest priority number will
always be the next compressor to start. The running
compressor with priority number 1 will always be the
next compressor to shut OFF. Whenever a compressor
is shut OFF, the priority numbers of all compressors
in each system will be decreased by 1 with the wrap
around. This control scheme assures the same com-
pressor does not repeatedly cycle ON and OFF.
ANTI-RECYCLE TIMER
The programmable anti-recycle timer assures that sys-
tems do not cycle. This timer is programmable under
the PROGRAM key between 300 and 600 s. When-
ever possible, to reduce cycling and motor heating, the
anti-recycle timer should be adjusted to 600 s. The pro-
grammable anti-recycle timer starts the timer when the
first compressor in a system starts. The timer begins
to count down. If all of the compressors in a circuit
cycle OFF, a compressor within the circuit will not be
permitted to start until the anti-recycle timer has timed
out. If the lead system has run for less than 5 min, 3
times in a row, the anti-recycle timer will be extended
to 10 min.
ANTI-COINCIDENCE TIMER
This timer is not present on single-system units. Two
timing controls are present in software to assure com-
pressors within a circuit or between systems, do not
start simultaneously. The anti-coincidence timer as-
sures there is at least a one minute delay between sys-
tem starts on 2-circuit systems. This timer is NOT pro-
grammable. The load timers further assure that there
is a minimum time between compressor starts within
a system.
EVAPORATOR PUMP CONTROL AND HYDRO
KIT PUMP CONTROL
The evaporator pump dry contacts (XTBC2 – Termi-
nals 23 and 24) are energized when any of the follow-
ing conditions are true:
1. Low Leaving Chilled Liquid Fault
2. Any compressor is running
3. Daily Schedule is ON, Unit Switch is ON and Re-
mote Stop is closed
Summary of Contents for QTC3040T
Page 10: ...THIS PAGE IS INTENTIONALLY LEFT BLANK...
Page 14: ...THIS PAGE INTENTIONALLY LEFT BLANK...
Page 30: ...THIS PAGE IS INTENTIONALLY LEFT BLANK...
Page 34: ...THIS PAGE IS INTENTIONALLY LEFT BLANK...
Page 73: ...THIS PAGE IS INTENTIONALLY LEFT BLANK...
Page 102: ...THIS PAGE IS INTENTIONALLY LEFT BLANK...
Page 110: ...THIS PAGE IS INTENTIONALLY LEFT BLANK...
Page 168: ...THIS PAGE IS INTENTIONALLY LEFT BLANK...