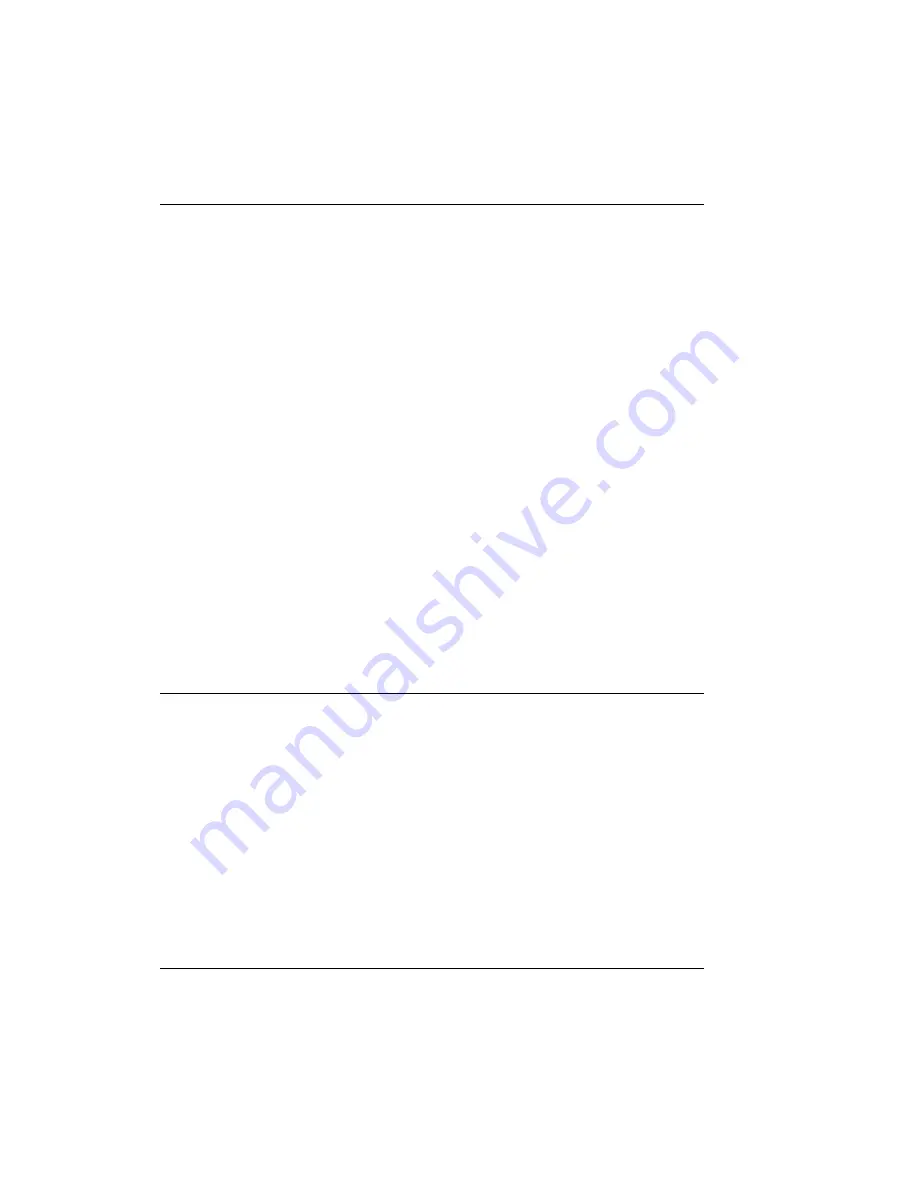
QLS 2000/3000 Series Digital Color Printers
16
Printer Setup
Specify Media Type
1. Press the Menu pushbutton to display the Main menu.
2. Use the arrow buttons to move the on-display indicator to the Media
position, then press the Select button to display the Media menu.
3. From the Media menu, use the arrow buttons to position the on-display
indicator before Type.
4. Press the Select button to move to the next line.
5. Use the arrow buttons to specify whether the stock has any top-of-form
indicators, and if so, which type:
Continuous.............................Top-of-form sensor detects no indicators.
Gap ........................................Top-of-form sensor interprets a gap, slot, or hole as a
top-of-form indicator.
Inverted Gap ..........................Top-of-form sensor interprets a solid area as a top-of-
form Indicator.
Mark ......................................Top-of-form sensor interprets a dark reflective mark
as a top-of-form indicator.
Calibration
Current Media
Calibrating the printer for the media being used is essential. Calibrate after
every change of label size or type.
During calibration, the printer senses any top-of-form indicator between labels
and allows the printer to position widely varying types of media automatically
and correctly. The printer stores the last calibrated values and menu setups even
after shut down and restart.
When calibrating continuous media, media length cannot be calibrated. Instead,
the printer is calibrated to detect the Media Out condition.