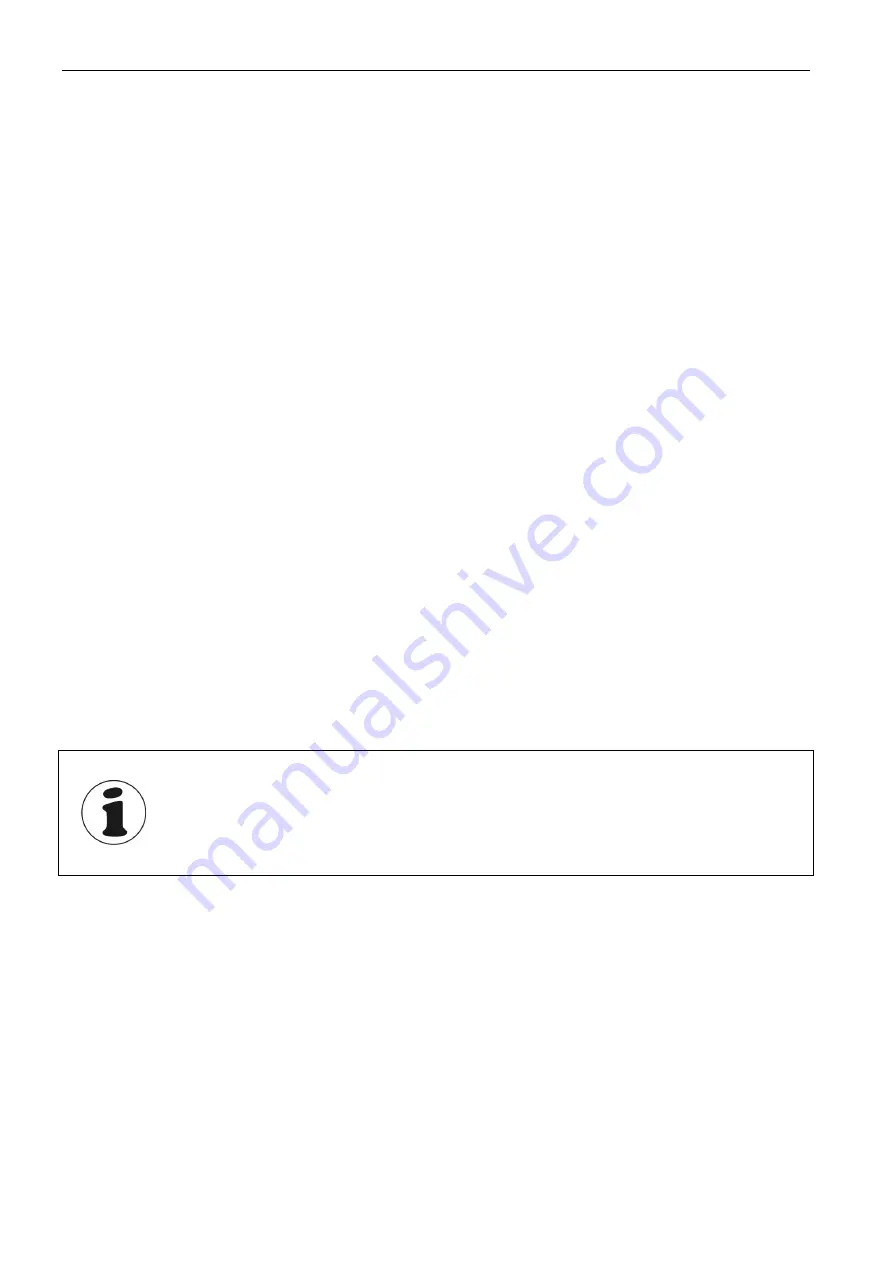
Pronar PDT260; PDT260C, PDT300; PDT 300C, PDT340
SECTION 1
1.6
•
protective aprons,
•
bearings.
The warranty service only applies to factory defects and mechanical damage that is not due
to the user's fault.
In the event of damage arising from:
•
mechanical damage which is the user's fault, caused by road accidents,
•
by inappropriate use, adjustment or maintenance, use of the machine for
purposes other than those for which it is intended,
•
use of damaged machine,
•
repairs carried out by unauthorised persons, improperly carried out repairs,
•
arbitrary and wilful adjustments to the machine's structure.
the user may lose the right to warranty service.
The user is obliged to report immediately on noticing any wear in the paint coating or traces
of corrosion, and to have the faults rectified whether they are covered by the warranty or not.
For detailed Terms & Conditions of Warranty, please refer to the WARRANTY BOOK
attached to each machine.
TIP
Demand that the seller carefully and precisely fills out the Warranty Book and warranty
repair coupons. A missing date of purchase or sale point stamp, may make the user
ineligible for any warranty repair or refund.
Modification of the mower without the written consent of the Manufacturer is forbidden. In
particular, do NOT weld, drill holes in, cut or heat the main structural elements of the
machine, which have a direct impact on the machine operation safety.
1.5
TRANSPORT
The machine is prepared for sale completely assembled and does not require packing.
Packing is only required for the machine operator's manual and elastic covers. Supply to user
takes place by transport vehicle. Transport of the mower is permissible connected to a tractor
Summary of Contents for PRONAR PDT260
Page 2: ......
Page 6: ......
Page 7: ......
Page 10: ...5 8 TIGHTENING TORQUE FOR NUT AND BOLT CONNECTIONS 5 18 5 9 TROUBLESHOOTING 5 20 ...
Page 11: ...SECTION 1 BASIC INFORMATION ...
Page 20: ...Pronar PDT260 PDT260C PDT300 PDT 300C PDT340 SECTION 1 1 10 ...
Page 21: ...SECTION 2 SAFETY ADVICE ...
Page 32: ...Pronar PDT260 PDT260C PDT300 PDT 300C PDT340 SECTION 2 2 12 ...
Page 33: ...SECTION 2 Pronar PDT260 PDT260C PDT300 PDT 300C PDT340 2 13 ...
Page 34: ...Pronar PDT260 PDT260C PDT300 PDT 300C PDT340 SECTION 2 2 14 ...
Page 35: ...SECTION 3 DESIGN AND OPERATION ...
Page 45: ...SECTION 4 CORRECT USE ...
Page 72: ...Pronar PDT260 PDT260C PDT300 PDT 300C PDT340 SECTION 4 4 28 ...
Page 73: ...SECTION 5 MAINTENANCE ...
Page 94: ...Pronar PDT260 PDT260C PDT300 PDT 300C PDT340 SECTION 5 5 22 ...
Page 95: ...NOTES ...
Page 96: ... ...
Page 97: ......