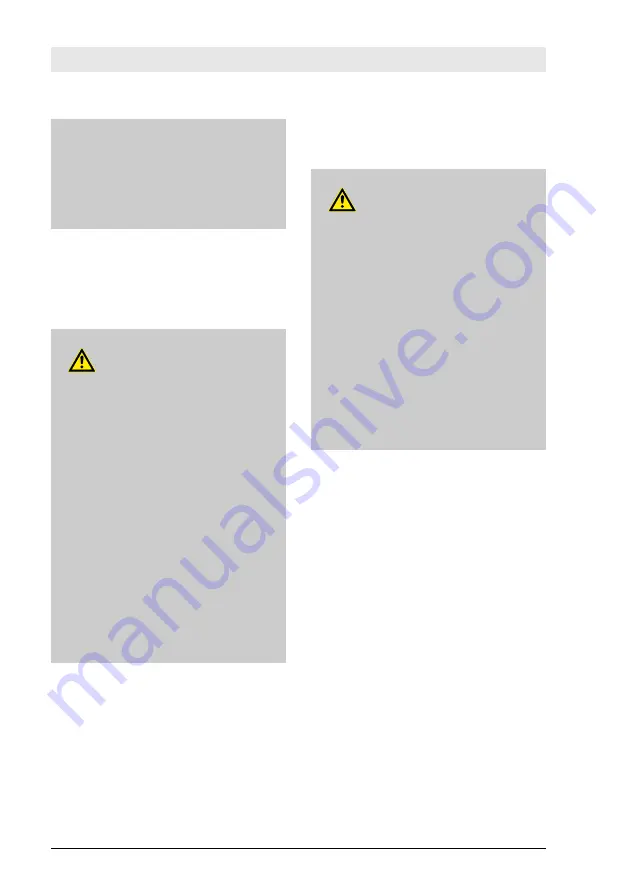
–
Do not place any electronic
storage media, credit cards,
etc. within the vicinity of the
magnetic source. Data could
be deleted
2.3.5 Hazards caused by
media
Hazardous media
WARNING!
Risk of injury from hazardous
media!
If the flow monitor is used for toxic,
corrosive or very hot/cold media
then there is a risk of serious injury
if the media escapes.
–
Observe details in the safety
data sheet of the media
–
Comply with the safety, acci-
dent prevention and environ-
mental protection regulations
appropriate to the media used
–
Wear personal protective
equipment in accordance with
the safety data sheet
2.4 Personnel require-
ments
WARNING!
Risk of injury due to use of
insufficiently trained and quali-
fied personnel!
If unqualified personnel work on
the device or are located within its
hazard zone, dangers arise which
may result in serious injuries and
considerable damage to property.
–
All work must be performed by
qualified personnel only.
–
Keep unqualified personnel
away from hazard zones.
Authorized personnel is to be restricted
to those persons who can be expected
to carry out their work reliably. Persons
whose ability to respond is influenced,
e.g. by drugs, alcohol or medication,
are not authorized.
Observe the age and occupational reg-
ulations at the site when choosing per-
sonnel.
Safety
Personnel requirements
18.03.2015
14
Summary of Contents for SW-01
Page 69: ...Fig 59 Type SW 04 3 4 Technical data Dimension sheet 27 04 2015 69...
Page 70: ...Fig 60 Typ SW 04 1 Technical data Dimension sheet 27 04 2015 70...
Page 153: ...Fig 60 Type SW 04 3 4 Technical data Dimension sheet 18 03 2015 70...
Page 154: ...Fig 61 Type SW 04 1 Technical data Dimension sheet 18 03 2015 71...