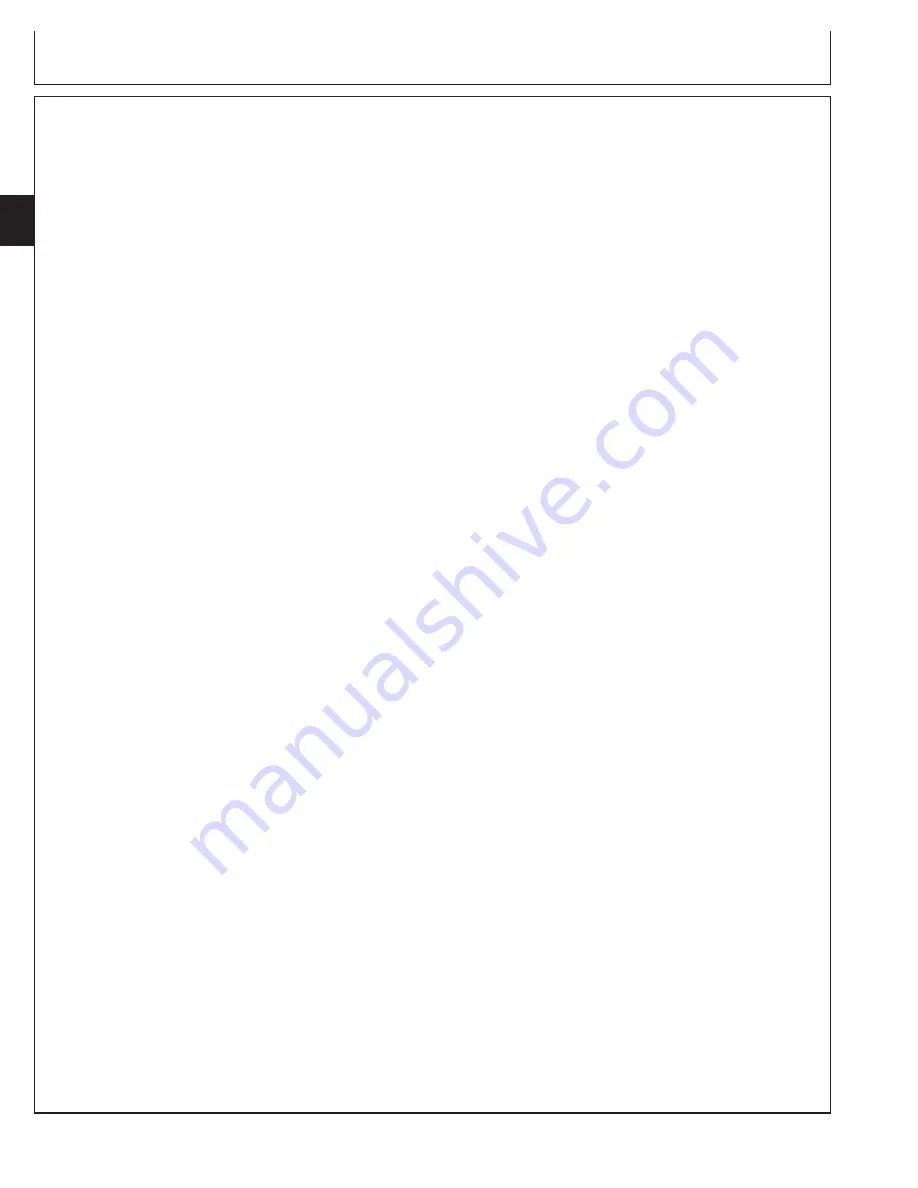
Crankshaft, Main Bearings, and Flywheel
02
040
24
RG,RG34710,168
–19–13AUG99–1/2
Crankshaft Grinding Guidelines
IMPORTANT: Crankshaft grinding should be done
ONLY by experienced personnel on
equipment capable of maintaining
crankshaft size and finish
specifications.
If undersize bearings are used,
check bearing clearance after
bearing caps have been tightened to
specified torque. If undersize
bearings are too tight and clearance
is not within specifications, the
journal and bearing will be wiped
clean of all oil. This would result in
premature wear of parts.
In addition to the standard size main and connecting
rod bearings, the following undersize bearings are
available.
Specification
Crankshaft Main Bearings
Available—Undersize
0.25, 0.50 mm (0.010, 0.020
in.)
.............................
If journals are tapered, out-of-round, scored or
damaged, grind the crankshaft and install the proper
undersize bearings.
If the crankshaft is to be reground, use the following
recommended procedure:
1. Compare the crankshaft journal measurements
taken during inspection and determine the size to
which the journals are to be reground.
2. If one or more main or connecting rod journals
require grinding, then grind all of the main journals
or all of the connecting rod journals to the same
required size.
3. All journal fillet radii must be free of any sharp grind
marks or scratches. The fillet must blend smoothly
into the journal and crank cheek. Check the radius
with a fillet gauge.
IMPORTANT: Care must be taken to avoid
localized heating which often
produces grinding cracks.
4. Cool the crankshaft while grinding by using coolant
generously. DO NOT crowd the grinding wheel into
the work.
IMPORTANT: Grind crankshaft with journals
turning clockwise, as viewed from
the front end of crankshaft. Lap or
polish journals in opposite direction
of grinding.
5. Polish or lap the ground surfaces to the specified
finish to prevent excessive wear of the journals.
NOTE: Production crankshafts are induction hardened
and shotpeened at the factory. Field
shotpeening is not recommended due to the
equipment required and part geometry.
6. If the thrust surfaces of the crankshaft are worn or
grooved excessively, regrind and polish. Maintain
the specified radius between each thrust surface
and the bearing journal. An oversize thrust washer
set containing one standard washer and two
0.18 mm (0.007 in.) oversize washers is available.
(See THRUST BEARING NEW PART
SPECIFICATIONS, later in this group.)
NOTE: When thrust surfaces are reground and
oversize washers used, crankshaft end play
specification must be maintained to within
0.038—0.380 mm (0.0015—0.0150 in.). (See
CHECK CRANKSHAFT END PLAY, earlier in
this group.)
7. Stone the edges of all oil holes in the journal
surfaces smooth to provide a radius of
approximately 1.50 mm (0.060 in.).
CTM100 (06APR04)
02-040-24
P
OWER
T
ECH
10.5 L & 12.5 L Diesel Engines
040604
PN=220
Continued on next page
Summary of Contents for 6105ADW
Page 16: ...Contents 01 CTM100 06APR04 01 2 POWERTECH 10 5 L 12 5 L Diesel Engines 040604 PN 2 ...
Page 50: ...Contents 02 CTM100 06APR04 02 4 POWERTECH 10 5 L 12 5 L Diesel Engines 040604 PN 4 ...
Page 334: ...Contents 03 CTM100 06APR04 03 2 POWERTECH 10 5 L 12 5 L Diesel Engines 040604 PN 2 ...
Page 350: ...Contents 04 CTM100 06APR04 04 2 POWERTECH 10 5 L 12 5 L Diesel Engines 040604 PN 2 ...
Page 376: ...Contents 05 CTM100 06APR04 05 2 POWERTECH 10 5 L 12 5 L Diesel Engines 040604 PN 2 ...
Page 412: ...Contents 06 CTM100 06APR04 06 2 POWERTECH 10 5 L 12 5 L Diesel Engines 040604 PN 2 ...