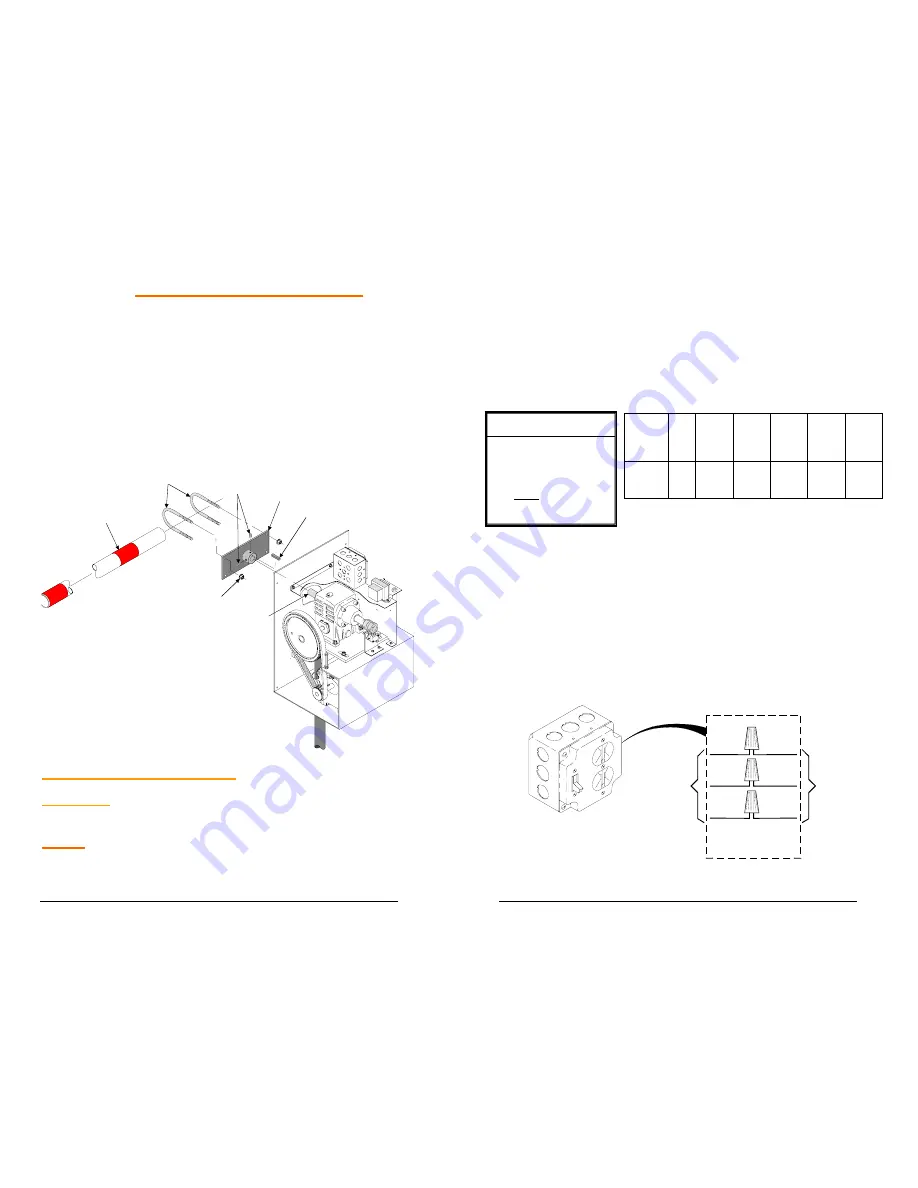
15
INSTALLATION OF BARRIER ARM
1. Install arm flange on power head output shaft as shown
figure below ,and secure position with ¼” square key and
(2) 5/16 set screws.
2. Install (2) 2-1/2” U-bolts in arm flange as shown.
3. Install 3/8 serrated flange nuts loosely on U- bolts.
4. Insert barrier arm pipe through two U-bolts and secure the
desired position by tightening the 3/8 serrated flange nuts
on the u-bolts.
2-1/2" U-BOLTS
ARM FLANGE
POWER HEAD
OUTPUT SHAFT
1/4" SQUARE KEY
5/16" SET
SCREWS
(4) 3/8" SERRATED
FLANGE NUTS
BARRIER ARM PIPE
ELECTRICAL CONNECTIONS
WARNING
- DO NOT APPLY POWER UNTIL TOLD TO DO
SO. RISK OF SHOCK OR INJURY MAY RESULT!
NOTE:
Wiring to operator must use watertight materials in
accordance with local electric code. See wire gauge/distance
charts for proper sizing. Master/Slave installations should
have
SEPARATE
power supply wiring or length of wire runs
16
BLK
BLK
WHT
WHT
GRN
GND
INSIDE UTILITY BOX,
CONNECT AS SHOWN
INCOMING
POWER
115V - 1Ø
OPERATOR
UTILITY BOX
should be figured at half that shown on the chart.
This unit
must be grounded in accordance with N.E.C. and local
codes.
Before connecting the operator, use a voltmeter to determine
that the electrical service is 115V. THIS OPERATOR
CANNOT BE CONNECTED AT 230 VOLTS. Damage will
result which is not covered under warranty.
1. Be sure power switches at source and operator are OFF.
2. Connect incoming power lines and ground wire as shown
below.
Hot leg (black) to BLACK; Neutral (white) to White:
Ground to GREEN
Line
Voltage
HP
14
AWG
12
AWG
10
AWG
8
AWG
6
AWG
115
VAC
1/2
150 250 400 500 650
LOW VOLTAGE WIRE
GAUGE /DISTANCE CHART
24 AWG: Up to 150'
20 AWG: 150' - 200'
250' - 1,500'
Control wiring should be run as twisted
pairs. DO NOT run control wires in the
same conduit as power wires. telephone
wires, or loop detector leads.
18 AWG: