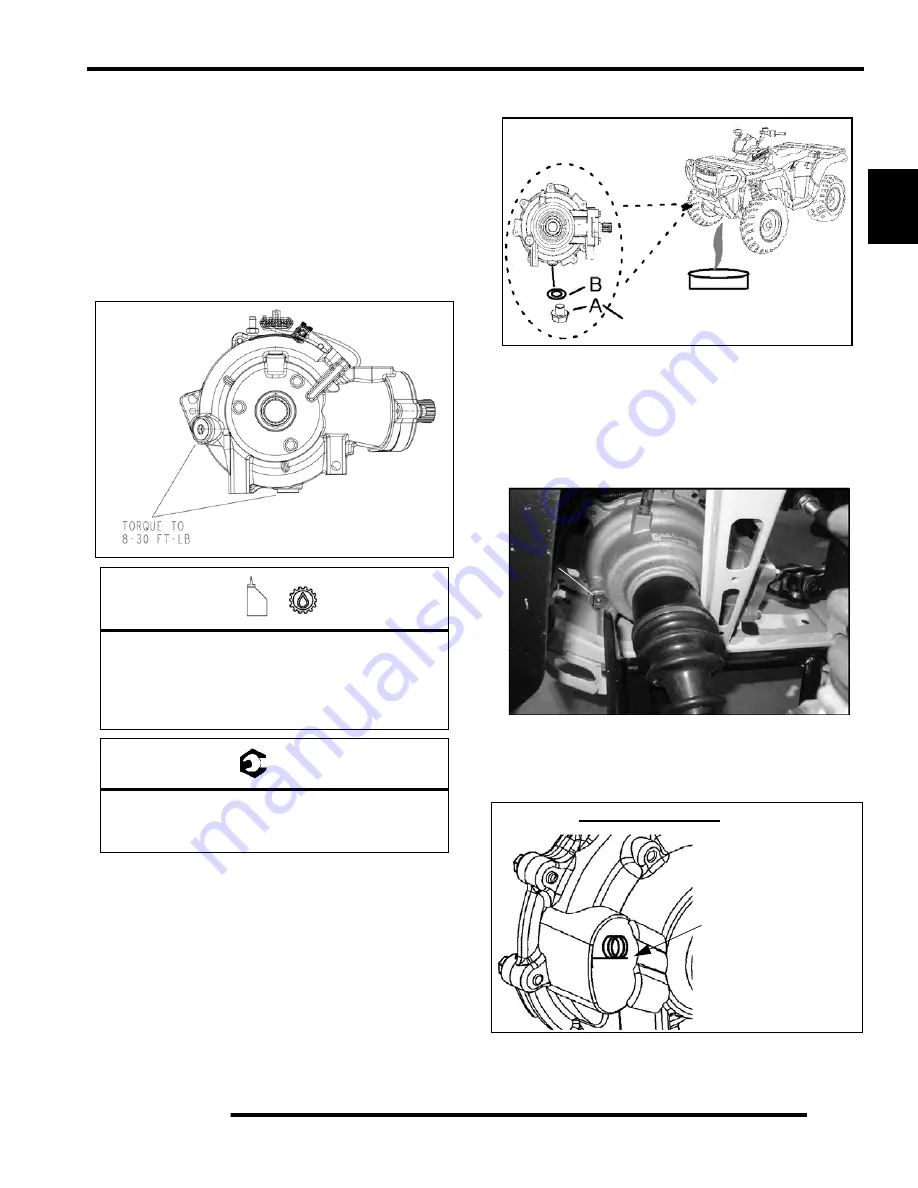
2.9
MAINTENANCE
2
9923412 - 2012 Sportsman 400/500 and EFI Tractor Service Manual
© Copyright 2011 Polaris Sales Inc.
Front Gearcase Lubrication
The front gearcase lubricant level should be checked and
changed in accordance with the maintenance schedule.
• Be sure vehicle is level before proceeding and in
PARK
• Check vent hose to be sure it is routed properly
and unobstructed
• The correct front gearcase lubricant to use is
Polaris Demand Drive PLUS Hub Fluid.
To Check the Lubricant Level:
The front gearcase lubricant level cannot be checked with
a dipstick. The gearcase must be drained and re-filled with
the proper amount of lubricant or be filled to the bottom of
the fill plug hole threads. Refer to procedures.
To Change Gearcase Lubricant:
1.
Remove gearcase drain plug (A) located on the
bottom of the gearcase and drain oil. (The drain plug
is accessible through the skid plate.) Catch and
discard used oil properly.
2.
Clean and reinstall drain plug (A) using a new sealing
washer (B). Torque to specification.
3.
Remove fill plug. Inspect the O-ring.
4.
Fill with the recommended fluid amount or to the
bottom of the fill plug hole threads. (See Illustration
below).
5.
Install / torque fill plug and check for leaks.
=
Specified Lubricant:
Demand Drive PLUS Hub Fluid
Gearcase Capacity:
8.97oz. (265 ml.)
=
T
Fill Plug Torque:
8-10 ft.lbs. (11-14 Nm)
Drain Plug Torque:
11 ft.lbs. (15 Nm)
Drain Plug
Left Side View
Fill Plug
Front Gearcase
Fill -Demand
Hub Fluid
Drive PLUS
Summary of Contents for 2012 Sportsman Forest 500 International
Page 1: ...1 GENERAL 2 MAINTENANCE 3 ENGINE 4 FUEL SYSTEMS 5 BODY SUSPENSION...
Page 2: ...6 CLUTCH 7 FINAL DRIVE 8 TRANSMISSION 9 BRAKES 10 ELECTRICAL...
Page 3: ...NOTES...
Page 115: ...NOTES ENGINE 3 60...
Page 117: ...4 2 FUEL SYSTEM...
Page 139: ...NOTES CARBURATION AND FUEL SYSTEM 4 24...
Page 185: ...NOTES 500 EFI FUEL SYSTEM 4 70...
Page 212: ...NOTES...
Page 258: ...NOTES CLUTCHING 6 46...
Page 330: ...NOTES TRANSMISSION 8 24...
Page 424: ...NOTES ELECTRICAL 10 60...
Page 425: ...Located By Battery...
Page 426: ......
Page 427: ...Located By Transmission Breakout Resistor Module...
Page 428: ......
Page 429: ...Located By Battery...
Page 430: ......
Page 431: ...Located By Transmission Breakout Resistor Module...
Page 432: ......