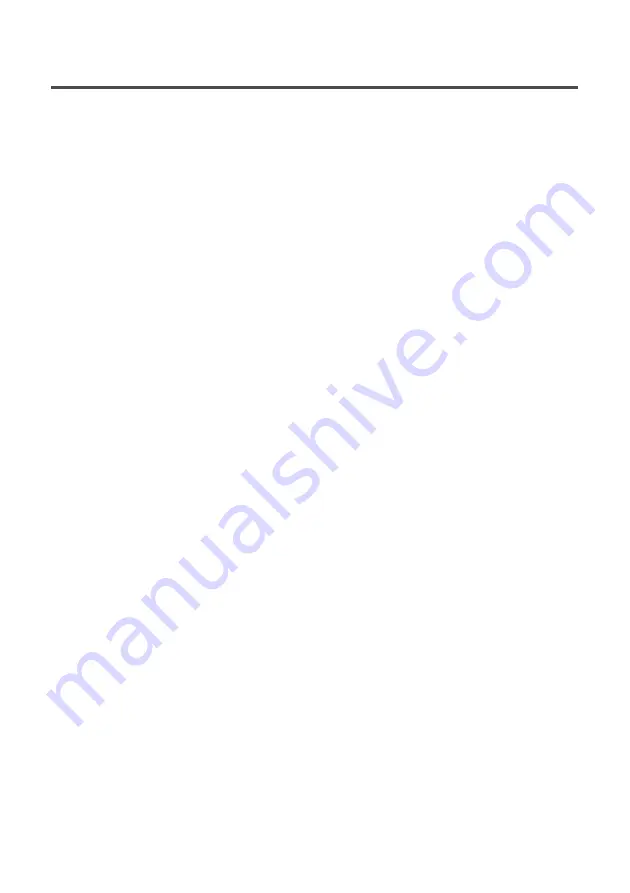
36
Reference
Machine stops for ‘Doubles’ that aren’t there
If you have problems with incorrect double detection, it may be due to the fact
that a new batch of material is being used which is slightly thicker. While running
the original trial piece, the machine would have calibrated itself to the material
thickness. When it senses the new, thicker material, it thinks that a double was
fed. Press
Trial Piece to recalibrate to the new material.
You can turn double detection off if an occasional duplicate insert is not important
- see pages 30 and 31.
Machine feeds ‘Doubles’ without stopping
Check that double detection is turned on - see pages 30 and 31.
Make sure you’ve run a trial piece to calibrate the double detection - see page 6.
Envelope flaps won’t seal
Check that Seal is selected (green indicator lit) - see page 6.
Check that the moistener isn’t empty - see page 9.
Try selecting safe seal mode - see page 31.
Address position wrong or address doesn’t appear in envelope window
Check that the addressed sheet is loaded properly - see page 10.
Check that the addressed sheet is loaded into Sheet feeder A2 (if it’s installed).
Try adjusting the address position - see page 29.
Inserts or business reply envelopes feed poorly from Insert Feeder C
Changing the orientation of the insert stack may help. For pre-folded inserts it’s
normally best to load with the ‘closed’ edge feeding first. Business Reply
Envelopes can normally be loaded right way up and facing you. However, if the
flaps are pulled open when feeding, try loading with the flaps down and facing
you.
Following installation of Sheet Feeder 2, the system doesn’t work
Check that the DI200 is correctly located onto Sheet Feeder 2.
Turn the machine off, wait a few seconds and then turn back on.
Check that no debris (dust, paper, etc.) has fallen into the Sheet Feeder 2
electrical connector.