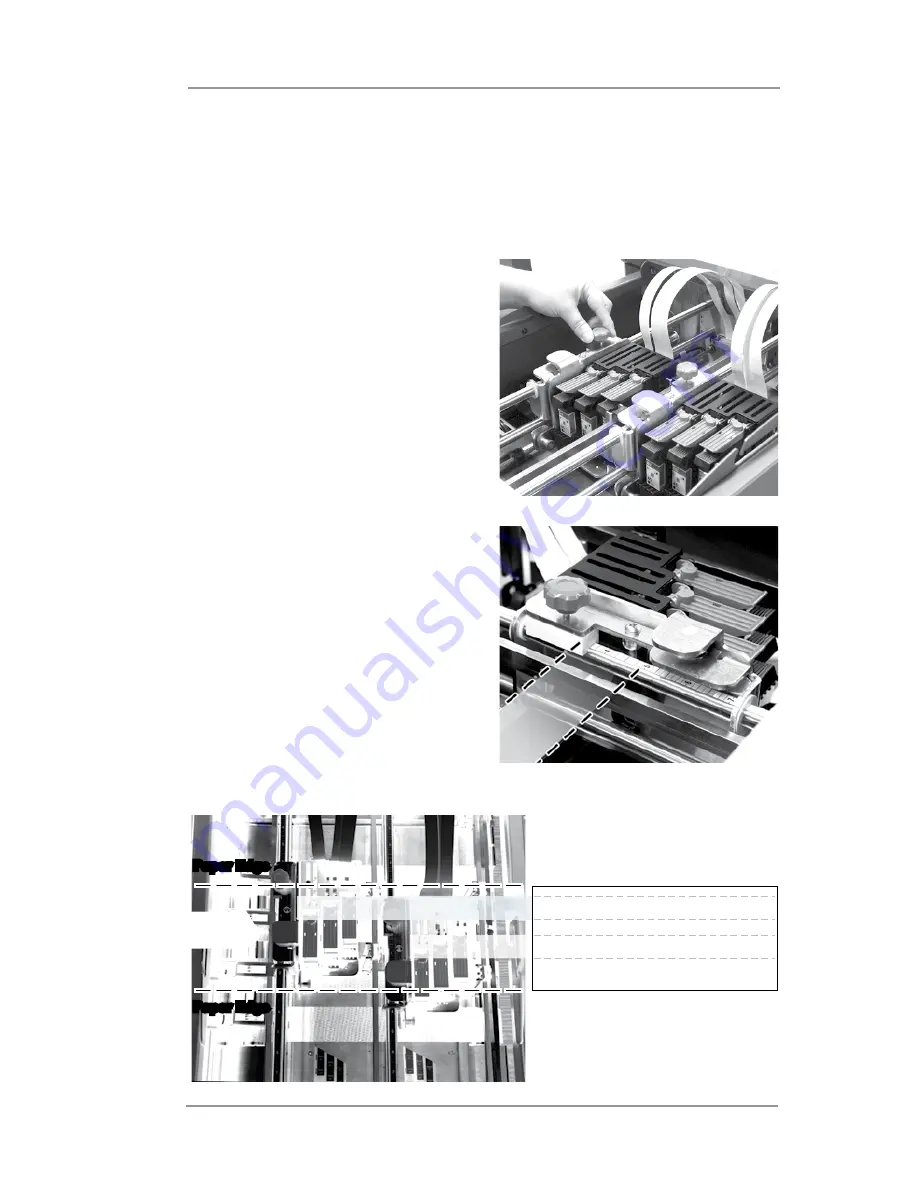
Printer Basics • 2
2-9
SV61749 Rev. D
6. Setting the Print Head Positions
It is necessary to position the two print head assembly modules
correctly over the path of the media so that your images and text will
print where you want them to.
A. Loosen the blue clamp knob on
top of the first module of print
heads (Module A).
B. Slide print head Module A along
the ruled slide guide to adjust
it's position until the slotted area
of the module is located over
the area that you wish to print
on (see photos side and below).
You can use the ruler printed
on the slide guide (US only)
if applicable to the envelope
printer software application that
you are using.
Example of print zones
Paper Edge
Material
Path
Print Zone
(Bank A)
Print Zone
(Bank B)
Company ABC
123 Anywhere Lane
Some Town, USA 12345
Corporation 123
456 Somewhere Street
Any Town, ST 67891
Paper Edge
Summary of Contents for da95f
Page 1: ...Operator Guide International English Version AddressRight DA Series Printer DA95F ...
Page 7: ...Contact Information List vi SV61749 Rev D ...
Page 64: ...3 Printer Maintenance 3 20 SV61749 Rev D ...
Page 74: ...4 Troubleshooting 4 10 SV61749 Rev D ...
Page 82: ...Appendix A Specifications A 8 SV61749 Rev D ...
Page 86: ...A 4 SV61749 Rev D ...