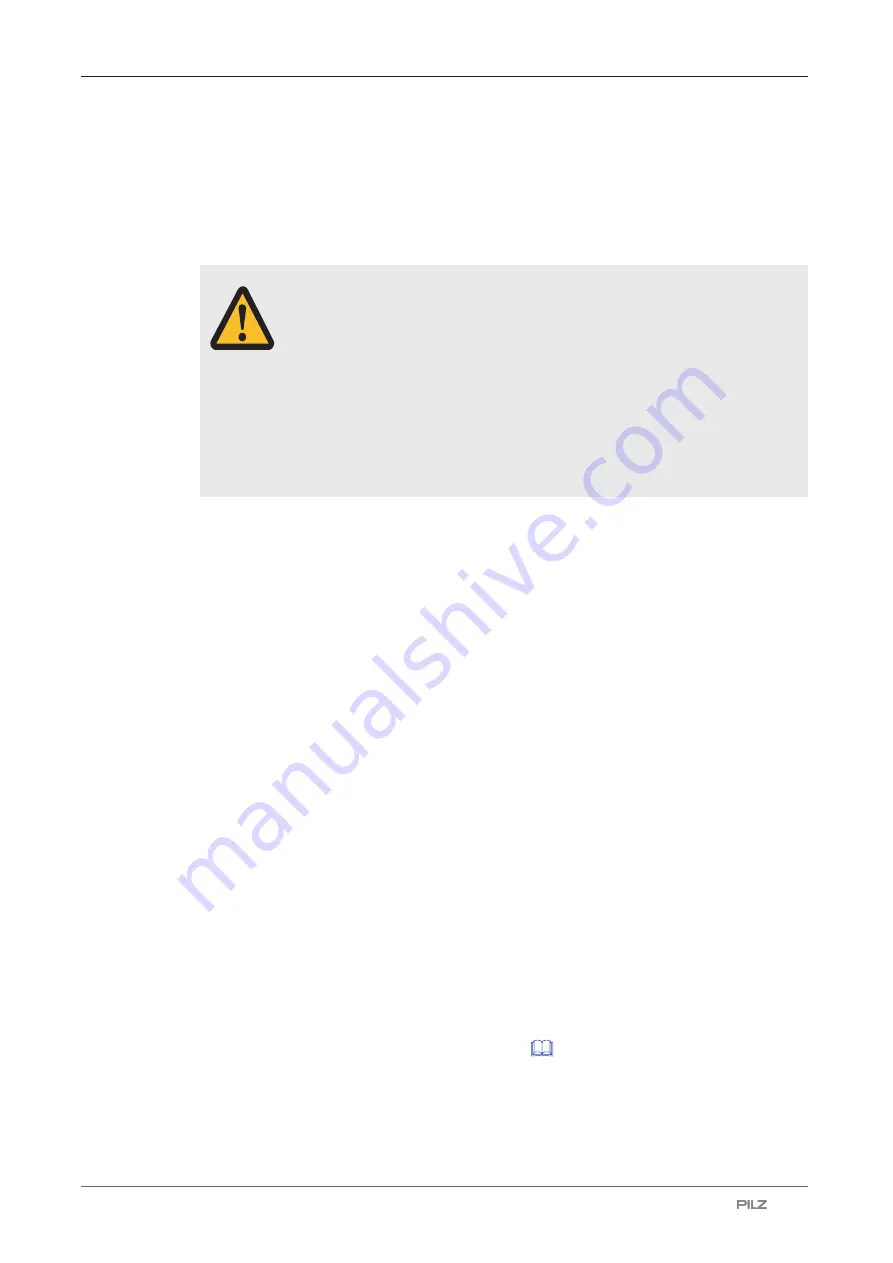
Change, maintenance, decommissioning
System Description Service Robotics Modules
1004870-EN-05
| 104
10.2.2
Exchanging the safety control system
The system or plant integrator is obligated to take the situations in which service robotics
modules from Pilz are exchanged into account in his risk analysis. The risk analysis must
indicate the appropriate measures.
We recommend that you consider the following when exchanging the safety control system.
WARNING!
Risk of electrocution!
When voltage is applied, contact with live components could result in seri-
ous or even fatal injury from an electric shock.
Ensure that assembly and disassembly work is carried out only in the de-
energised state.
Before you start disassembling, switch off the supply voltage at the control
cabinet main switch and disconnect the supply voltage cable.
Prerequisites
}
The robot arm has been moved to its park position, depending on the application.
}
The wiring diagram for the application is available.
}
The supply voltage has been switched off at the control cabinet main switch.
}
The supply voltage cable for the robot control module has been disconnected.
}
A safety control system with identical design and identical hardware version is available
as the exchange device.
Procedure
}
Remove all connections and connectors from the safety control system.
}
Remove the SD card from the safety control system and insert the SD card in the ex-
change device.
}
Swap the safety control system for the exchange device.
}
Restore all the connections using the wiring diagram for the application.
Please note:
The supply voltage must only be reconnected right at the end!
}
Switch on the safety control system.
}
On the safety control system, perform the deliberate operator action to transfer the nam-
ing data and device project. To do this refer to the PSS 4000 System Description (see
chapter entitled Mode of operation – Functions of the reset button – Deliberate operator
action to transfer the naming data and/or device project).
}
).