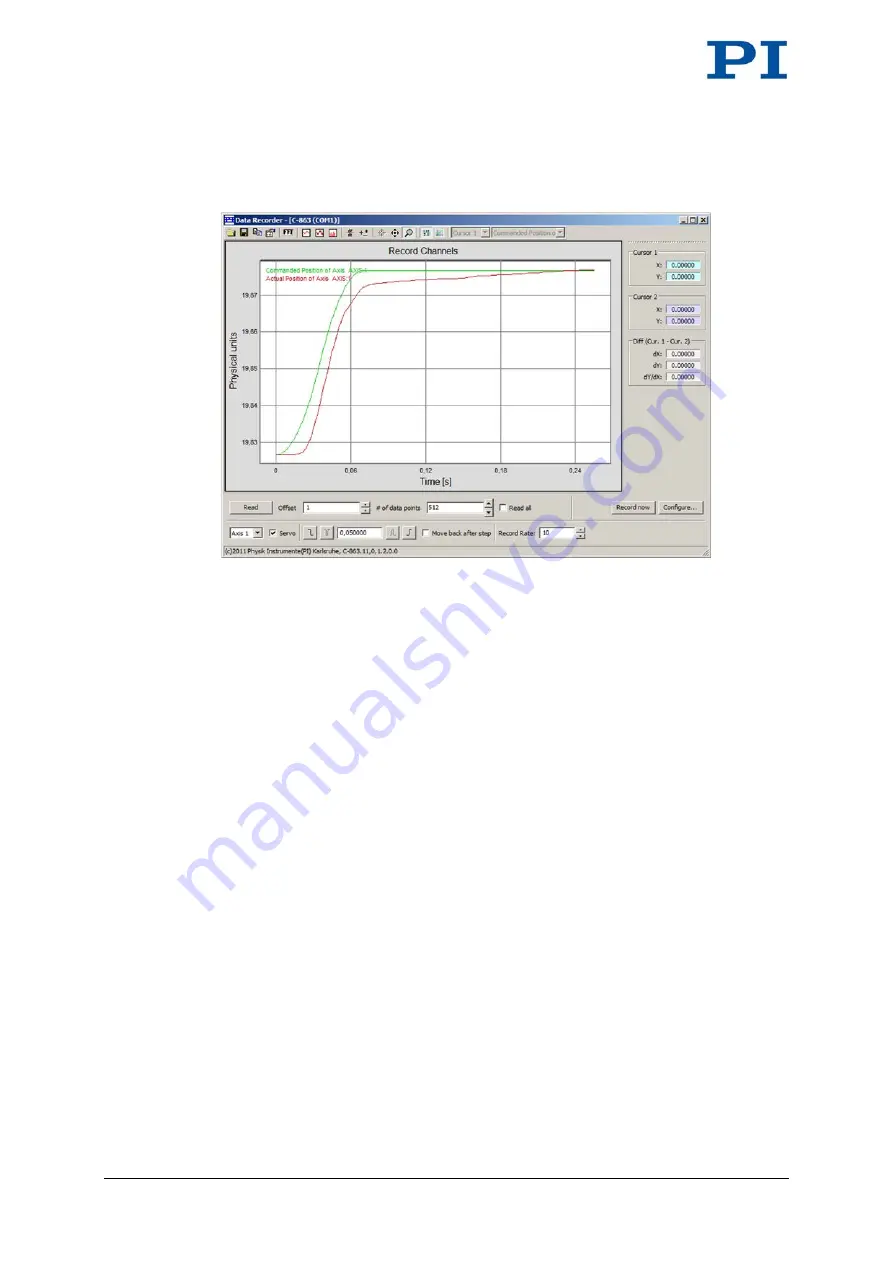
7 Start-Up
64
Version: 2.0.0
MS205Equ
C-863 Mercury Controller
Figure 18: PIMikroMove: Data recorder with graphical display of a to slow step-and-settle
7.7 Optimizing the Servo-Control Parameters
Adjusting the P-I-D controller optimizes the dynamic properties of the system
(overshoot and settling time). The optimum P-I-D controller setting depends on your
application and your requirements.
As a rule, optimization is done empirically and involves the following parameters.
Details see "Servo Algorithm and Other Control Value Corrections" in the detailed
version of the user manual MS205E:
P-Term
(0x1)
I-Term
(0x2)
D-Term
(0x3)
I-Limit
(0x4)
The behavior of the stage is monitored under various values in closed-loop operation.
In the following, PIMikroMove is used for optimizing the P-I-D servo-control
parameters.