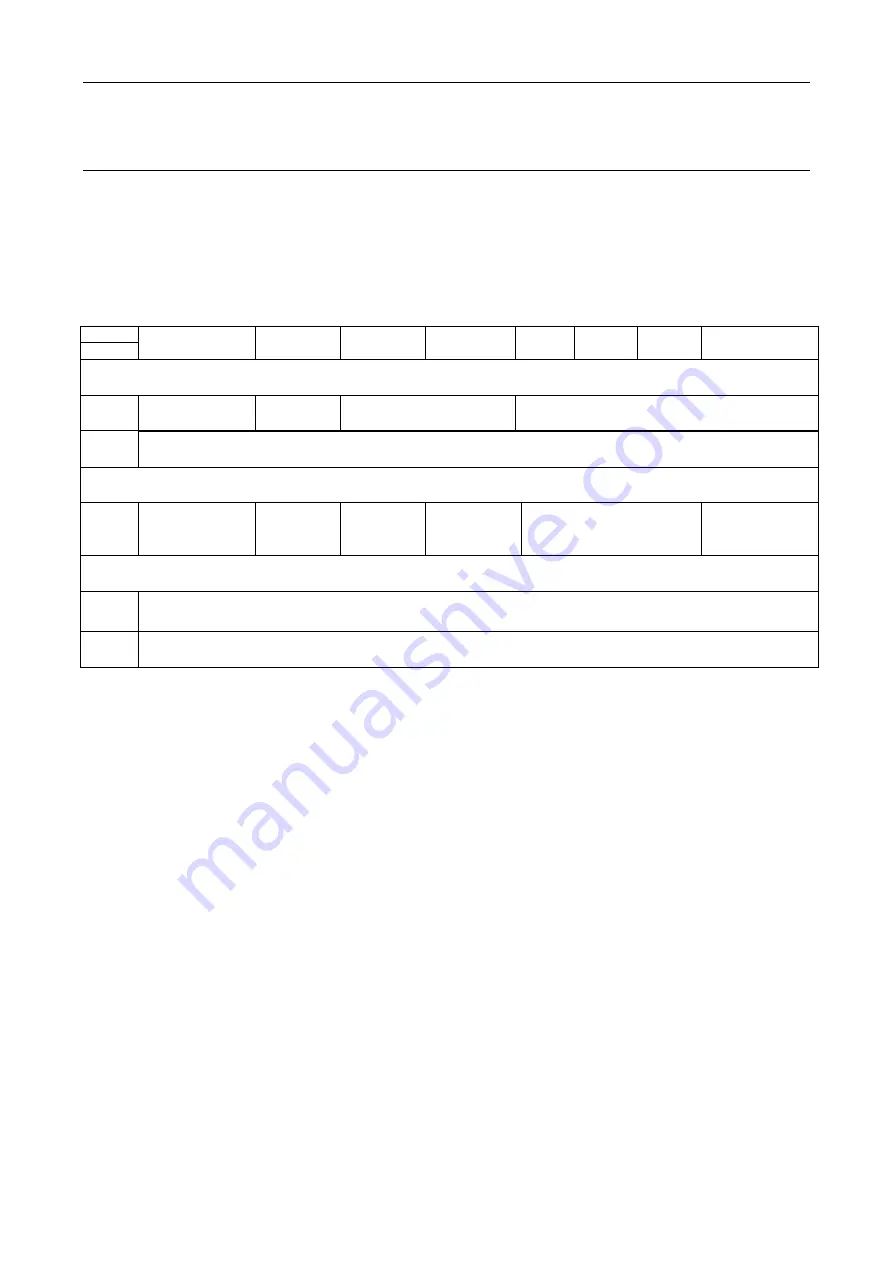
phytron
79
MA 1303-A007 EN
12 Appendix: Parameters and Data Record
12.1 Data Record 128 (DS128): Read and Write Parameters
i
The data record can be read
without
restriction.
Bit →
7
6
5
4
3
2
1
0
Byte ↓
HEADER
0
reserved = 0
MajorVersion = 1
MinorVersion = 0
1
Length of the following channel parameter block (byte 2 ... 35)
34 Byte
DIAGNOSIS
2
Position Error
Driver
Error
reserved
DIS input
active
reserved
Missing supply
voltage L+
DRIVER CONFIGURATION
3…6
Start-stop frequency
7…10
Acceleration