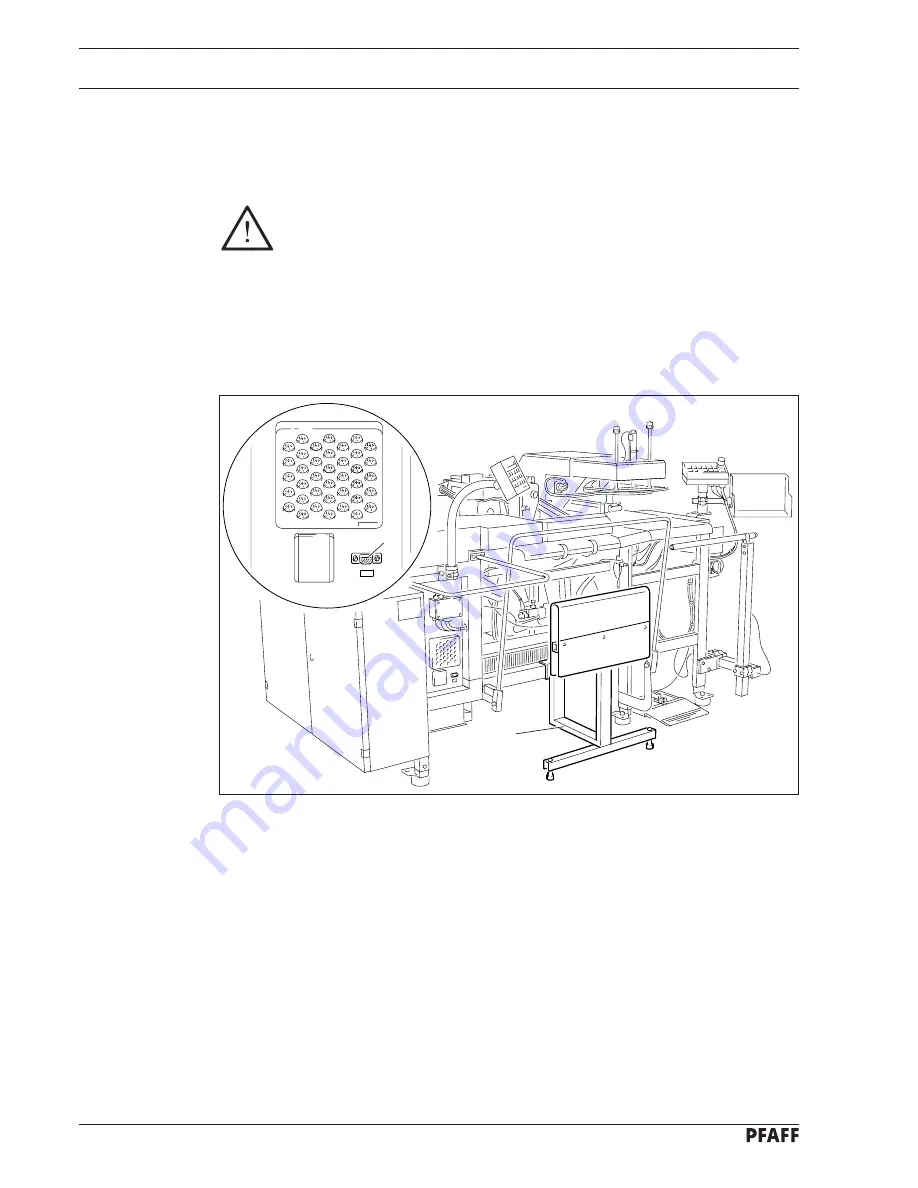
Mounting and commissioning the machine
9 - 1
9
Mounting and commissioning the machine
After unpacking the machine, check it for any transport damage. In case of damage, inform
the shipping company and the responsible PFAFF dealer.
The machine must only be mounted and commissioned by qualified personnel!
All relevant safety regulations are to be observed!
9
.01
Mounting
Suitable connections for supplying electricity and compressed air must be available at the
machine’s location (refer to
chapter 3 Specifications
).
The location where the machine is set up must have a flat, sturdy surface.
●
Lift the machine with a forklift from the shipping pallet.
●
Screw the six enclosed rubber springs onto the legs.
●
Set down the machine on the ground and make sure it is standing horizontally by pushing
the legs.
●
Attach stacker frame and align.
●
Plug disk drive into socket
2
.
Fig. 9 - 01
1
2
Summary of Contents for 3568-12/22
Page 1: ...3568 12 22 Instruction manual 296 12 17973 Betriebsanleitungengl 03 97...
Page 72: ......
Page 73: ......
Page 140: ......
Page 141: ......