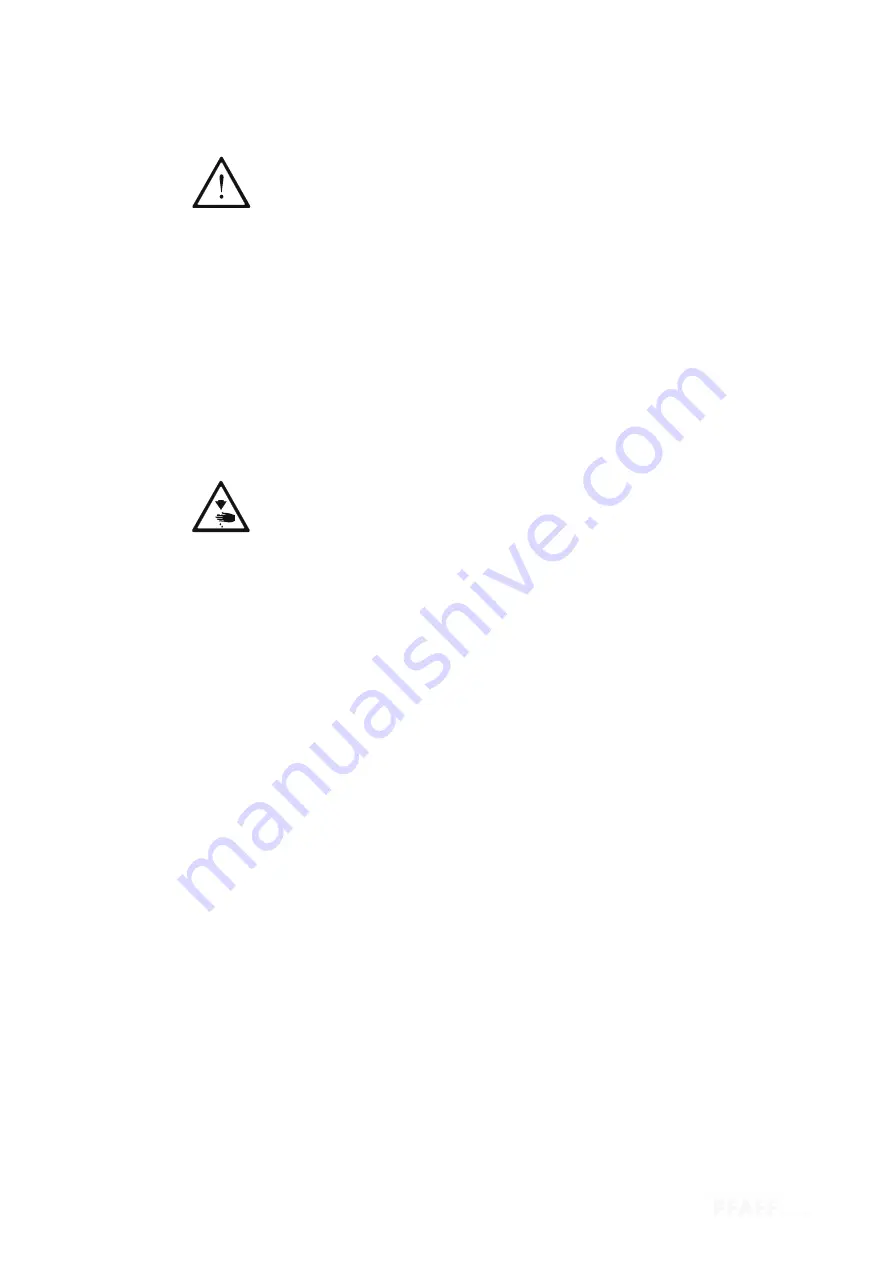
Adjustment
66
13 Adjustment
No screw clamp may be fastened to the needle bar with the
PFAFF
3519-4/01!
This may damage the special needle bar coating.
13
.01
Notes on adjustment
All adjustments in this manual are based on a fully assembled machine and may only be
carried out by technical staff trained for this purpose. Machine covers, which have to be
removed and replaced to carry out checks and adjustments, are not mentioned in the text.
The order of the following chapters corresponds to the most logical work sequence for
machines that have to be completely adjusted. Both the preceding and following chapters
must be observed if only specific individual work steps are carried out.
The screws and nuts indicated in brackets ( ) are fastenings for machine parts, which must
be loosened before any adjustment and tightened again afterwards.
Unless otherwise stated, the machine must be disconnected from the electric
and pneumatic supplies for all adjustment work!
Risk of injury due to accidental machine start-up!
13
.02
Tools, gauges and other accessories
●
1 set of screwdrivers with blade widths from 2 to 10 mm
●
1 set of wrenches with jaw widths from 7 to 14 mm
●
1 set of Allen keys from 1.5 to 6 mm
●
1 open-ended wrench with 22 mm wrench size
●
1 metal ruler, order no. 08-880 218-00
●
1 adjustment gauge, (order no. 95-752 474-05)
●
1 setting gauge for the hook drive belt tension, order no. 61-111 639-76
●
1 setting gauge for the infeed table needles, (order no. 95-743 776-15)
●
Thread and testing material
13
.03
Abbreviations
t.d.c. = top dead centre
b.d.c. = bottom dead centre
Summary of Contents for 3519-5/01
Page 38: ...Sewing 38 Double point darts Fig 10 02 0 320 mm 0 320 mm Insertion mark Insertion mark...
Page 155: ...155 91 191 499 95 Part 7 Version 07 02 12 Circuit Diagram Overview Start 2 Start 1 Air okay...
Page 156: ...156 Circuit Diagram Overview Version 07 02 12 91 191 499 95 Part 8 A12 CAN3...
Page 157: ...157 91 191 499 95 Part 9 BDF P1 Version 07 02 12 Circuit Diagram Overview RS232 interface...