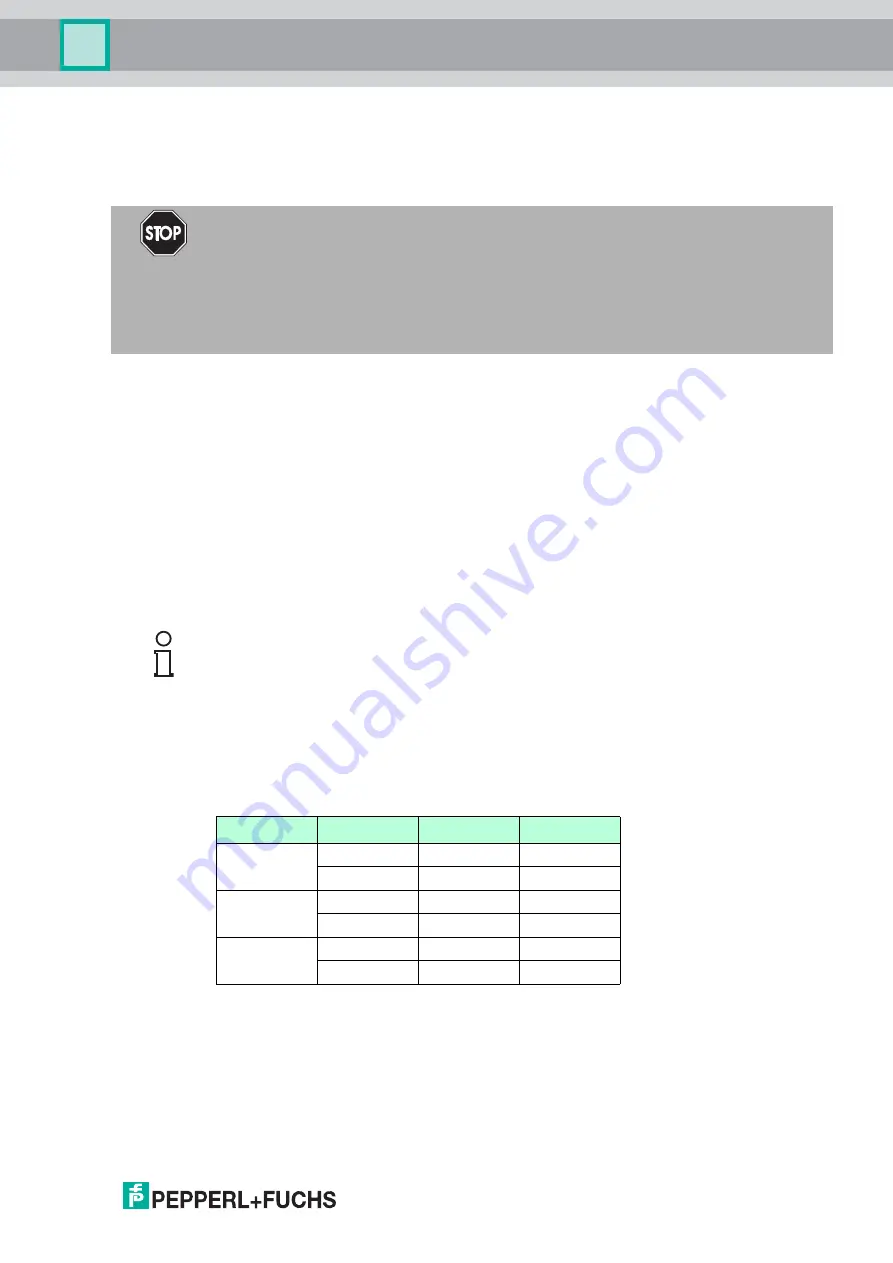
Temperature Multi-Input Device
Installation and Commissioning
2
017-
05
15
3.2.2
F2 Housing Degree of Protection
The following section contains information concerning the installation and sealing of the cable
glands and the housing cover.
Installing Cable Glands
When installing cable glands, observe the following:
■
Only insert permanently laid cables and wires into the cable glands.
• Ensure that the cables laid do not execute any strain on the cable glands.
• For permissible cable diameters, refer to the respective datasheet.
■
Use an appropriate strain relief clamp, e.g., a suitable cable clamp.
■
Seal unused cable glands with a suitable plug or replace them with appropriate screw
plugs. Observe the required degree of protection IP66.
• For a choice of stop plugs and screw plugs, refer to the respective datasheets.
• Note that the ambient temperature range can be restricted by the stopping plug.
■
Protect plastic cable glands against mechanical hazard.
The following table with tightening torques offers an approximate guideline:
F2D0-TI-Ex8.* Tightening Torques for Cap Nuts and Counterparts
Danger!
Explosion hazard or danger to life from inadequate installation of cable glands
If you do not install cable glands according to the instructions given in the instruction manual,
this can generate sparks that can ignite the surrounding potentially explosive atmosphere.
Furthermore, insufficient installation practice can result in electric shock.
Ensure you carry out any cable gland installations in accordance with the instructions given in
the instruction manual.
Note!
Careful when tightening cap nuts!
■
The cap nuts must be securely tightened. Tightening the cap nuts too much or not enough
both can affect the degree of protection.
■
The tightening torques of cap nuts vary, depending on the cable type used. For exact
details refer to the documentation of your cable manufacturer.
Type
Size
Cap nut
Counterpart
F2D0-TI-
Ex8.*.*:*.CG
M16
2.5 Nm
3.75 Nm
M20
2.5 Nm
3.75 Nm
F2D0-TI-
Ex8.*.*:*.CGB
M16
6 Nm
6 Nm
M20
10 Nm
10 Nm
F2D0-TI-
Ex8.*.*:*.CGS
M16
6 Nm
6 Nm
M20
10 Nm
10 Nm