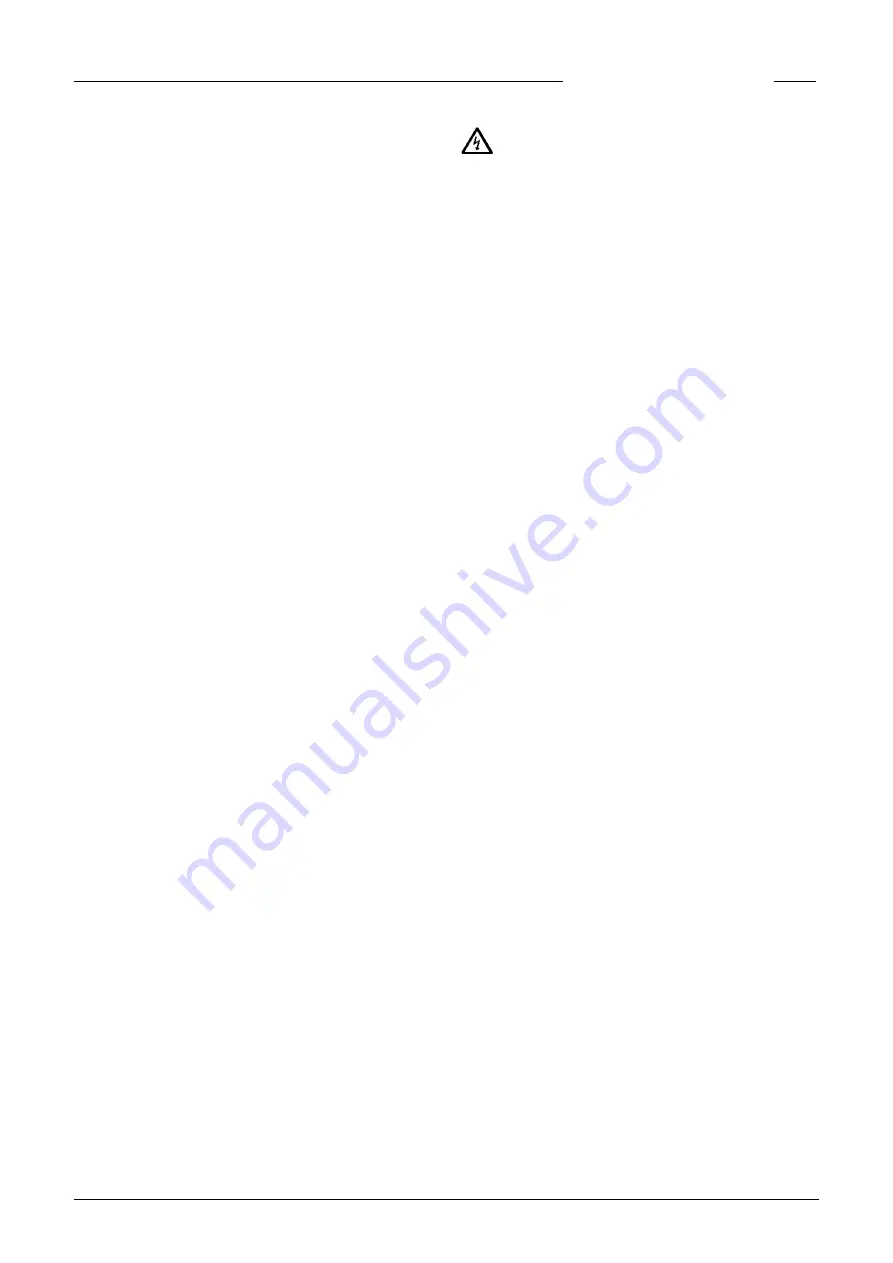
11
ENGLISH
Installing the tank
Close the sluice valve in the inlet (accessory) to prevent any
leakage of water during the installation work.
Screw the four angle brackets to the sides of the tank.
NOTICE!
Ensure that the tank does not become deformed due to over-
tightening the screws, otherwise this could result in leakage.
Slide the lifting station, together with the clamping flange, as
far as possible onto the inlet pipe and then align them.
If a DN 150 side inlet is used, it must first of all be opened up at
the location marked using a Ø 152 hole saw and then deburred.
The standard inlet must in this case be closed off with the seal-
ing plug supplied.
Tighten the hexagon screws on the clamping flange.
In the case of compli 2500, connect the two tanks together
with a DN 150 pipe and clamping flanges.
Mark the position of the drill-holes for anchoring the tank to
the ground, drill the holes, insert rawlplugs and screw the tank
in place using wood screws and washers.
Installing the pump
Screw three duckfeet to the underside of each bend.
Connect the bends to the tank using a flexible connector and
hose clamps.
Next, bolt the bends to the floor.
Place the seals on the bends, set the pumps down on top of
them and affix them from below using hexagon screws.
Installing the ventilation
Connect the DN 70 vent pipe to the top of the tank with the
flexible connector and vent it above roof level. In the case of
compli 2500, both tanks must be connected with a flexible
connector but they can be brought together with a tee branch.
Installing the pressure pipe
Attach the supports to the flanged connections (accessory)
and screw them to the pumps. The remaining parts of the
pressure pipe can now be assembled:
1. Swing-type check valves (accessory),
2. Stop valves (accessory)
3. “Y” piece (accessory).
4.
Connect up the pressure pipe with the flexible connector and
a flanged spigot (accessory) and take it in a loop over the local
backup level.
Emergency pump connection (DN 50 at front)
This connection is used for the HMP hand diaphragm pump
(accessory).
Using a (Ø 38) hole saw, open up either the right-hand or left-
hand pipe socket at the location marked and deburr the edges.
Fix the hand diaphragm pump to the wall at an easily acces-
sible place and connect it to the pipe sockets on the tank with
PVC piping and flexible connectors. The pressure pipe must be
laid in a loop above the local backup level.
ELECTRICAL CONNECTION
NOTICE!
Only qualified electricians may carry out electrical
works to the pump or the control units.
WARNING!
Before carrying out any work, unplug the lifting station from the
mains socket and ensure that the power supply to the lifting sta-
tion cannot be switched on again by anyone else.
NOTICE!
Never put the mains plug and free lead ends in water! If
water gets into the plug, this can cause malfunctions and dam-
age.
The relevant standards (such as EN standards), national regu-
lations (such as VDE in Germany), and the regulations of the lo-
cal power supply companies must be observed.
Observe the operating voltage (see type plate)!
The lifting stations have a level controller that switches the
pumps on and off depending on the level of the water. An in-
tegrated alarm system beeps if there is a malfunction, even if
this is only temporary.
If the pumps overheat, the motor cuts out due to the wind-
ing thermostat. Before remedying the fault, the lifting sta-
tion must be disconnected from the power supply. Unplug the
mains plug from the electrical socket or turn the main switch
off, as otherwise the pumps will be switched on again auto-
matically after they have cooled down. A direct malfunction
message is not generated.
For the mains electrical connection of compli 1525, 1535, 2525
and 2535 type units, a correctly installed five pole CEE power
socket is required (3/N/PEx400 V, 50 Hz). This must be located
in a dry room above the backup level.
For compli 1555, 1575, 15100, 2555 and 2575 type units, the
mains power supply is connected directly to the terminals of
the main switch for the control unit. The cross section of the
connection cable must be configured to take into account the
current input of the pumps and the length of the connection
cable.
NOTICE!
Only time delay fuses or automatic fuses with C char-
acteristics are to be used as pre-fuses for the pump. If the pre-
fuses have been triggered, the cause of the malfunction must
be eliminated before switching the pump on again.
Mounting the control unit
Only operate the control unit in dry rooms above the backup
level, and keep the housing closed at all times. The control
unit must be easily accessible to enable it to be checked at any
time. High humidity and condensation can destroy the con-
trols!
Connecting the pumps
The pumps are connected to the control unit on site in ac-
cordance with the circuit diagram (appendix). The three-phase
pumps are protected with an overcurrent release or motor
protection switch, set to the rated c 10%.
Coil thermostats
NOTICE!
In addition to the overcurrent release or motor pro-
tection switch, the thermostats in the motor winding must be
connected to the control unit (terminal 30/32).
The thermostat contacts are suitable for a maximum of 250 V
/ 1.2 A (cos phi = 0.6) and are labelled 30 and 32 for connection
purposes. The motor is switched off via the 230V control cir-
cuit when the response temperature is reached. The pump is
switched on again automatically after the winding has cooled
down.
Summary of Contents for COMPLI 15100/2 B5
Page 2: ...2 ...
Page 43: ...43 compli 1500 ...
Page 44: ...44 compli 2500 ...
Page 45: ...45 ...
Page 46: ...46 ...
Page 50: ...50 BS 1016 PD BS 1620 PD ...
Page 51: ...51 BS 1016 PD BS 1620 PD ...
Page 52: ...52 Main switch BS 2532 PD ...
Page 53: ...53 pot free contact optional YE YE GN YE GN GN RD RD BS 2532 PD ...