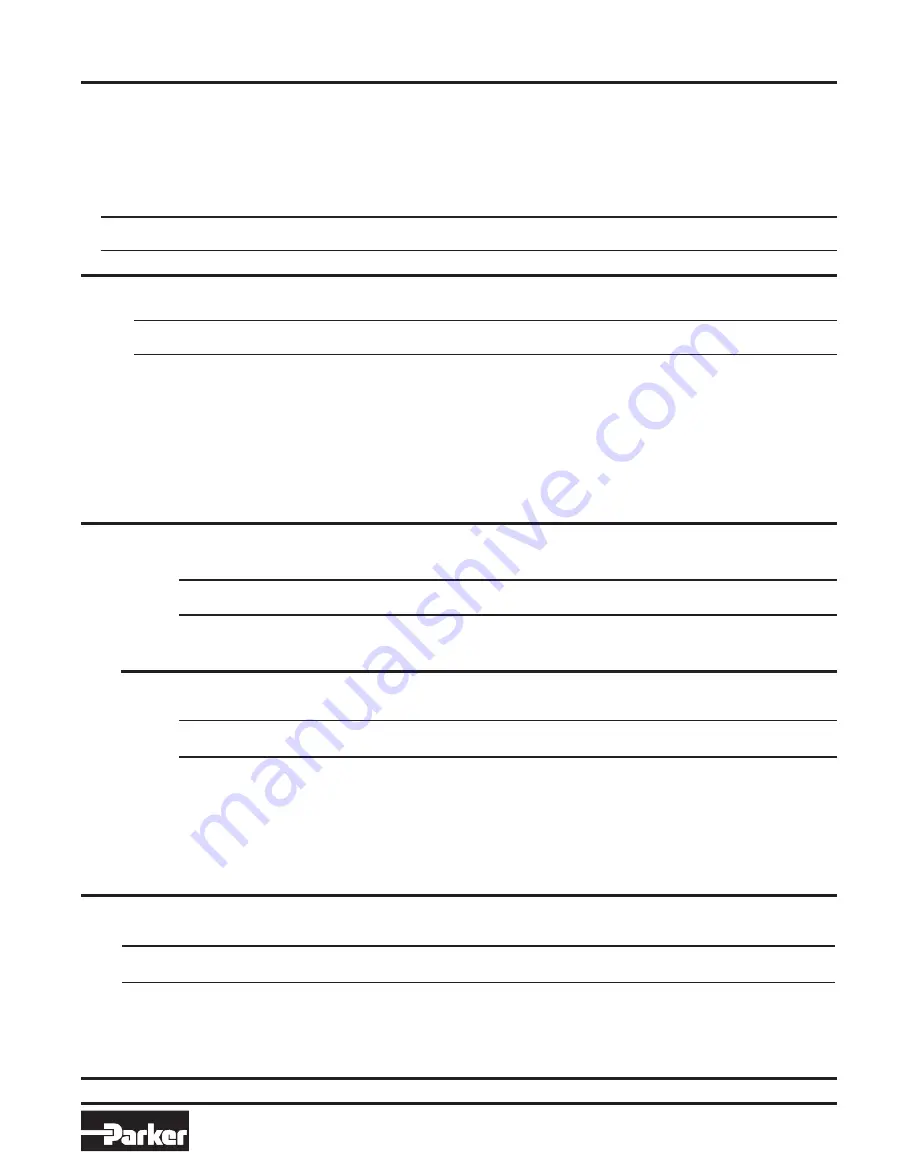
HY13-1527-M1/US
Torqmotor™ Service Procedure
TF, TG, TH and TL Series
Parker Hannifin Corporation
Hydraulic Pump/Motor Division
Greeneville, TN 37745 US
16
TH Service Parts List Chart
Chart Use Example:
TH0140MS310AAAB Torqmotor™ includes part numbers listed to the right of TH (SERIES), 0140 (DISP.), M (MOUNTING), S (PORTING),
31 (SHAFT), 0 (ROTATION), and AAAB (OPTION) shown in the left hand column of the chart.
Caution:
The charted component service information is for the Torqmotors listed only. Refer to the original equipment manufacturer of the equipment
using the Torqmotor for assembly numbers not listed below.
EXPLODED VIEW
ITEM #
8
5 & 6
7
9
11
1
13
1
14
1
15 17
1
19 20 25
COMMUTATOR MANIFOLD WEAR
THRUST
INNER
THRUST
THRUST BACKUP
OUTER DIRT & WATER BACKUP
DESCRIPTION
ASSEMBLY
(SEE NOTE) PLATE BEARING BEARING WASHER(2) BEARING WASHER BEARING
SEAL
WASHER
TH-
Service Part # ME018000A1 ME015000 477342 068024 071031 069010 (2) 069022 028537 069034
478063
028538
SERIES
EXPLODED VIEW
2
(SELECT ITEM # BOLT PER OPTION GROUP)
ITEM #
1 OR 1A OR 1B OR 1C
8A
8B
10
DISPLACEMENT
ROTOR ROTOR FREE
RUNNING DRIVE
DRIVE
LINK
(in
3
/rev)
BOLT (7) BOLT (7) BOLT (7) BOLT (7)
THICKNESS
SET
ROTOR SET
LINK
“L DIM”
0140- 8.6
021390 021273 021273 021379
.6286
ME097003 ME097007 ME093000
4.4385
0170- 10.3
021376 021387 021387 021392
.7518
ME107003 ME107007 ME103000
4.5650
0195- 12.0
021352 021379 021379 021291
.8768
ME127003 ME127007 ME123000
4.6905
0240- 14.5
021272 021291 021291 021412
1.0643
ME157003 ME157007 ME153000
4.8795
0280- 17.1
021340 021392 021392 021385
1.2518
ME187003 ME187007 ME183000
5.0685
0335- 20.6
021273 021385 021385 021366
1.5018
ME217003 ME217007 ME213000
5.3195
0405- 24.7
021379 021366 021415 021374
1.7923
ME247003 ME247007 ME243000
5.6045
0475- 29.1
021392 021394 021394 021393
2.1268
ME297003 ME297007 ME293000
5.9475
0530- 32.3
021385 021393 021393 021395
2.3768
ME337003 ME337007 ME333000
6.1985
0625- 38.0
021366 021329 021329 021458
2.7536
ME377003 N/A ME373000
6.5745
0785- 48.0
021395 021388 021388 021416
3.5036
ME487003 N/A ME483000
7.3285
0960- 58.5
021396 021389 021389 021399
4.2536
ME587003 N/A ME583000
8.0815
DISPLACEMENT GROUP
EXPLODED VIEW
ITEM #
1
18
DESCRIPTION
SERVICE
MOUNTING
PORTING
HOUSING ASS’Y
MS- SAE A (4 Bolt)
7/8” O-Ring
MJ012002A1
US- Wheel Mt. (4 Bolt)
7/8” O-Ring
MJ012001A1
MM- Standard Mt. (4 Bolt)
Manifold
MJ012014A1
EXPLODED VIEW
ITEM #
1, 1A, 1B, 1C
2
1
18
DESCRIPTION
END
SERVICE
MOUNTING
PORTING
BOLT
COVER
HOUSING ASS’Y
MA- Standard Mount (4 Bolt)
Rear Port (7/8” O-Ring; Axial)
Item #1B
ME016009
MJ012004A1
UA- Wheel Mt. (4 Bolt)
Rear Port (7/8” O-Ring; Axial)
Item #1B
ME016009
MJ012003A1
MB- Standard Mount (4 Bolt)
Rear Port (7/8” O-Ring; Radial)
Item #1B
ME016002
MJ012004A1
UB- Wheel Mt. (4 Bolt)
Rear Port (7/8” O-Ring; Radial)
Item #1B
ME016002
MJ012003A1
ME- Standard Mount (4 Bolt)
Rear Port (Manifold; Radial)
Item #1B
ME016001J1
MJ012004A1
UE- Wheel Mt. (4 Bolt)
Rear Port (Manifold; Radial)
Item #1B
ME016001J1
MJ012003A1
P*- SAE B (4 Bolt)
Rear Port Only
Item #1B
MJ012008A1
K*- SAE CC (4 Bolt)
Rear Port Only
Item #1B
MJ012019A1
HOUSING GROUP
Mounting Code Porting Code
REAR POR
TING
FRONT POR
TING
Mounting Code Porting Code
EXPLODED
VIEW
ITEM
#
12
12A
12B
12C
12D
12E
12F
COUPLING
7/8-14x1.250
LOCK
RETAINING
DESCRIPTION
SHAFT
KEY
NUT
WASHER
BOLT
WASHER
RING
19- 1 3/8” Tapered Shaft
MJ019011
31- 1-1/2” Tapered Shaft
MJ019000
039046* (3/8x1)
025131
32- 1-1/2” Straight Key
MJ019001 039040** (3/8x1.43)
028492
021483
028966
401464
36- 17 Tooth Spline
MJ019002
62- 14 Tooth Spline
MJ019007
73- 17 Tooth Spline M12 Tap MJ019009
COUPLING SHAFT GROUP