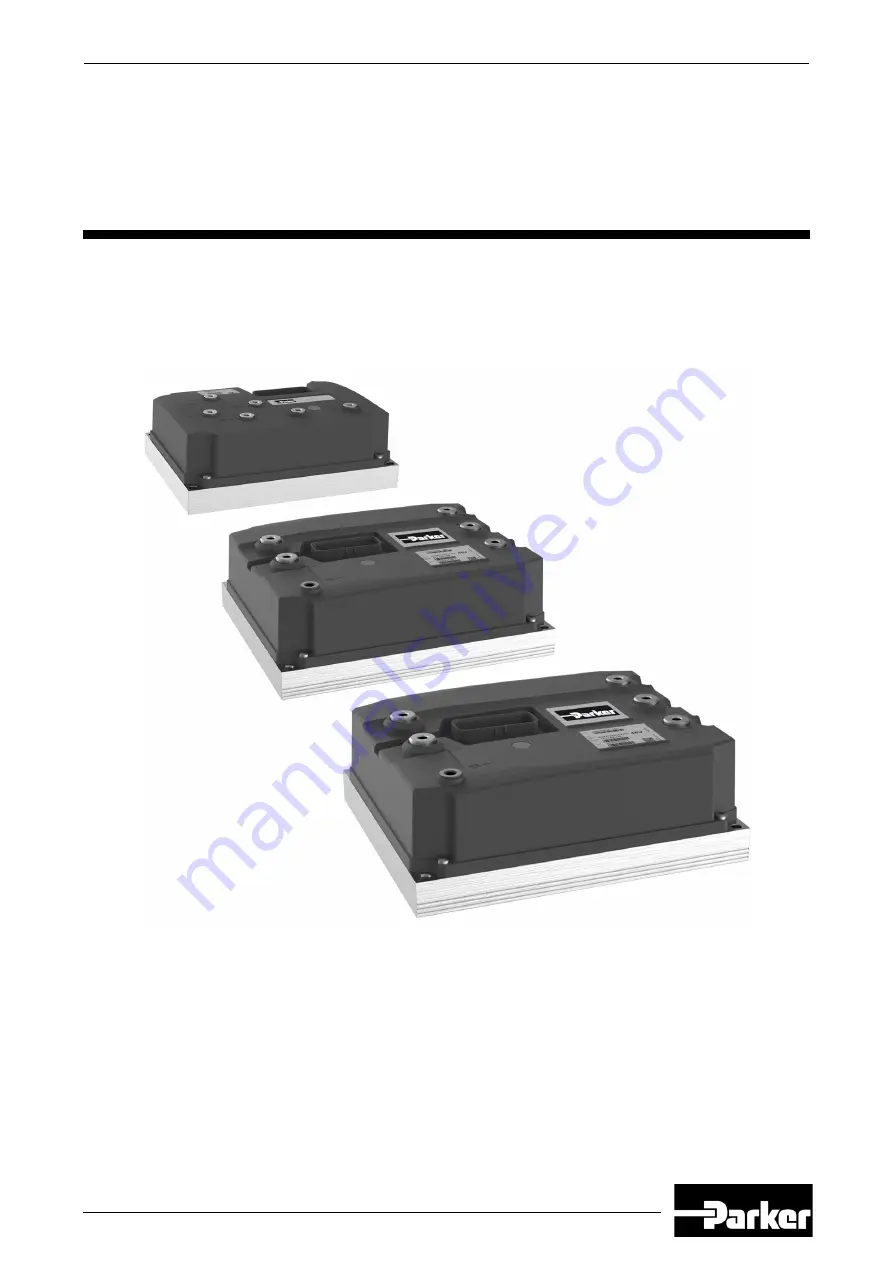
GVI Product Manual: Frames C, D & E
We reserve the right to make technical changes.
25.09.19 06:47
192-300300N1 GVI Frames C, D & E 2019-9
The data correspond to the current status at the time of printing.
Product Manual GVI
GVI: Global Vehicle Inverter Frame C, D and E
192-300300
192-300300N1 GVI
Product Manual
September 2019