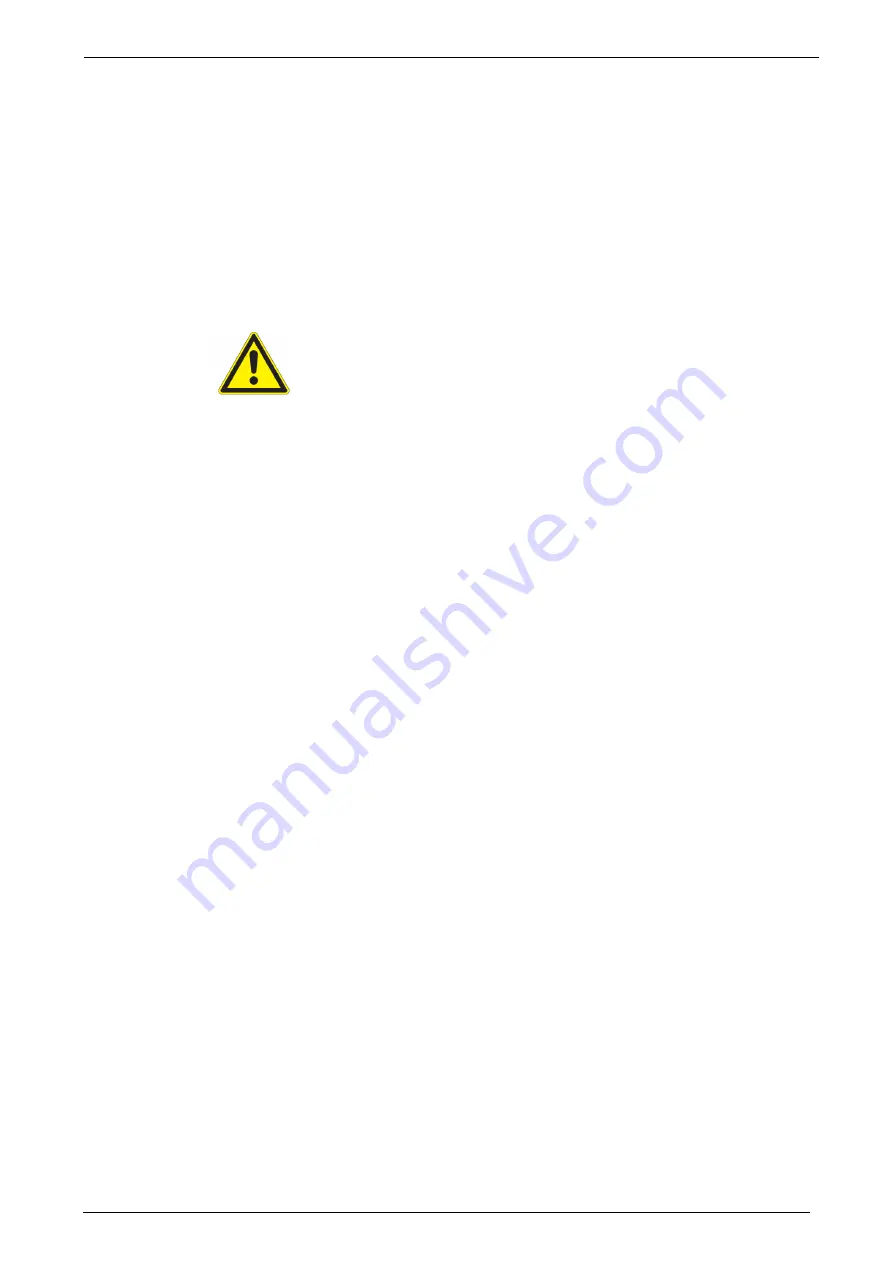
Parker EME
Introduction
15
192-300300N1 GVI Frames C, D & E 2019-9
7. Integration guidelines
7.1
Introduction
This chapter describes guidelines for integration of the motor controller. Integration is the installation of the
converter into a vehicle.
The information is general in nature. General instructions for mounting of the converter in a vehicle are found
in chapter 10.
High power levels are exposed at each of the connection posts. These terminals should be protected from
accidental contact which could result in a short circuit.
WARNING
ESD - risk of damage to equipment
Electrostatic discharges (ESD) can damage sensitive electronic components.
•
Do not touch the I/O connector pins.
•
The GVI meets all necessary standards for ESD-protection.
However, very high levels of static electricity can build up
during handling of the equipment. The built-in ESD-protection
does not replace a professional and careful handling.
7.2
Dust and liquid ingress prevention
The dust/moisture protection of the motor controller is only valid when the mating I/O connector is inserted
and correctly assembled with appropriate cable seals.
The motor controller cover provides a measure of protection from liquids and particles dripping, splashing or
spraying onto it. The motor controller must not be subjected to liquids under high pressure.
7.3
Cooling requirements
The motor controller is mounted upon a solid heat sink. This is the surface that transfers heat from the power
conversion components to the surroundings.
In order to cool the power conversion components efficiently, it is important to consider the thermal
resistance between the heat sink and the surroundings according to chapters 7.3.1. The motor controller
operating temperature is specified in chapter 13.1. Higher operating temperature or less efficient cooling is
permissible, but will result in a reduction of the operating lifetime or power output of the motor controller (see
chapter 13.2).
The motor controller is designed to operate with a maximum heat sink temperature of 85 ºC. During
performance testing of a new vehicle design, it is necessary to ensure that the vehicle can fulfill its
environmental and performance specifications without exceeding this temperature of the motor controller. If
this is not possible to achieve, the OEM should consider improving cooling of the motor controller, switching
to larger motor controllers, or reduce vehicle performance.
If the heat sink temperature exceeds 85 °C the maximum available motor current is automatically reduced.
The motor controller will still operate, with reduced performance, up to 110 °C, when an emergency
shutdown will take place. It should be noted though, that the motor controller is operating outside its
specification in this case, and it should only be used as a “limp home” option to let the driver return the
vehicle to a service area where the reason for the overheating can be remedied.
It is strongly recommended that an error message is generated and that vehicle performance is decreased if
the motor controller temperature exceeds 85 °C.