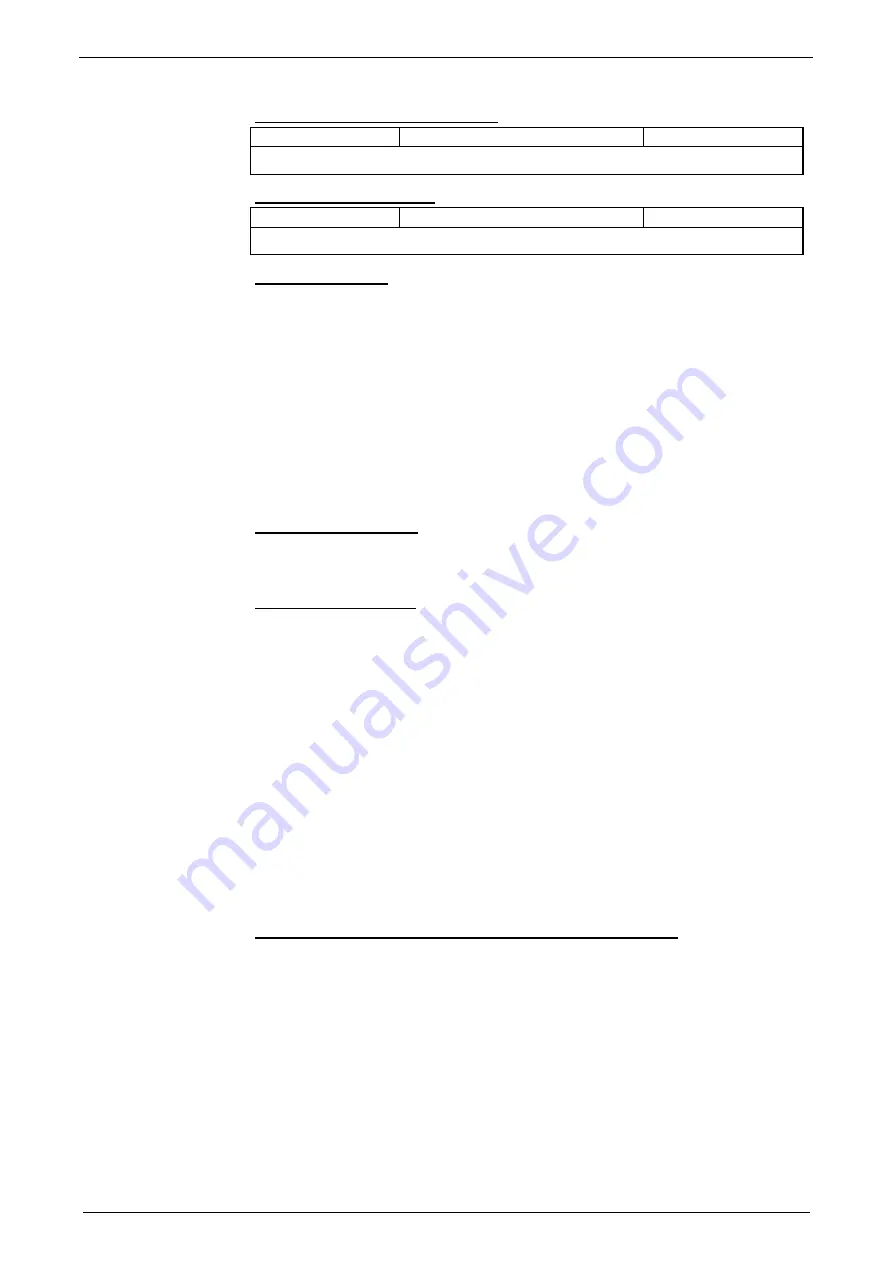
Parker EME
Setting up Compax3
192-120100 N16 C3I10T10 - December 2010
135
Unit: %
2100.6: Filter - Actual acceleration
Range: 0 ... 550
Standard value: 100
Uni
t: %
2100.4: Moment of Inertia
Range: 10 ... 500
Standard value: 100%
For motors with distinct transition from static friction to kinetic friction in connection
with a noisy feedback signal, where a control oscillation is generated at standstill, 3
optimization objects are available:
Position controller
Deadband (Object 2200.20)
Following error filter (object 2200.11) and
Friction compensation (Object 2200.21)
The control oscillation at standstill is eliminated by the deadband.
Please note, however, that the possible exactitude is reduced by the deadband.
The use of the following error filter and the friction compensation can reduce the
deadband.
A noisy feedback signal necessitates to set an unnecessarily large deadband.
Noisy feedback signal:
To avoid this, the time constant of the following error filter can be increased.
The following error can be reduced faster with the aid of friction compensation,
which will reduce the deadband.
Friction compensation
The objects (deadband, following error filter, friction compensation) are stored in
the motor library. Therefore these objects are overwritten when configuring another
motor.
PowerRod
When configuring a PowerRod, the deadband (+/-25µm) and the following error are
preassigned, the friction compensation is switched off.
Remaining motors of the motor library
For all other motors (not PowerRod), the objects are preassigned with "0".
Forward control measures
Forward control of rotation speed, acceleration and current
Minimal following error
Improves the transient response
Gives greater dynamic range with lower maximum current
Application:
Note:
Advantages: