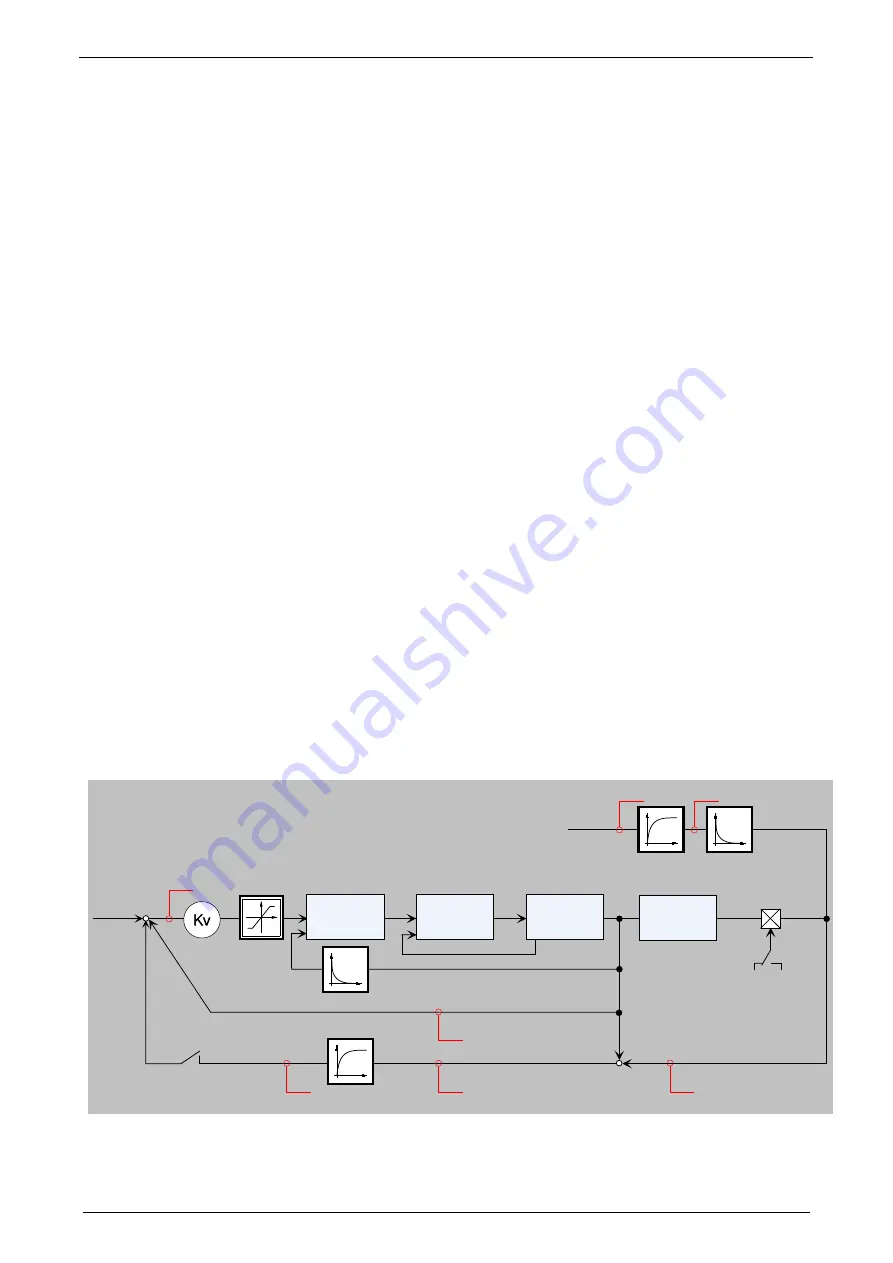
Parker EME
Setting up Compax3
192-120113 N08 C3I12T11 - December 2010
161
There is an
Alignment of the position values
of motor and load under the
following operating conditions (Load position = Motor position):
During a
Machine zero run
the load control is deactivated until the position value
0 (defined via the machine zero offset) was approached.
Then an alignment of the position values is performed and the load control is
activated.
After switching on Compax3.
When writing "1" into object 2201.2
When activating the load control.
Continuous mode
In continuous operation (object 1111.8 <> 0) an alignment of the position values of
motor and load (load position = motor position) takes place upon each new
positioning command.
Application: e.g. roller feed
4.3.2.
Error: Position difference between load mounted and motor
feedback too high
The (unfiltered) position difference between motor feedback and load feedback has
exceeded the "maximum difference to motor position" value (O410.6)
The load position in the position controller is deactivated.
In order to re-activate the function (after eliminating the cause of the error), you
have the following possibilities:
Activate function in configuration and perform configuration download or enter
True (-1) into O2201.1
Perform Ackn and/or Homing (function becomes effective after homing run).
Caution!
The position difference is aligned to zero when switched on again, i.e. the original
position reference is lost. Therefore it is advisable to approach the reference point
again in this case (Machine zero run or Homing).
4.3.3.
Load control signal image
speed
control
681.20
2201.12
681.21
current
control
mechanics
680.6
speed
load
target
position
680.20
position
motor
- -
-
680.13
680.23
2201.11
680.22
load feedback
direction inversion
(configuration)
+1
-1
on
off
2201.1
=1 (active)
=0 (inactive)
motor
position
load
Alignment of the
load control: