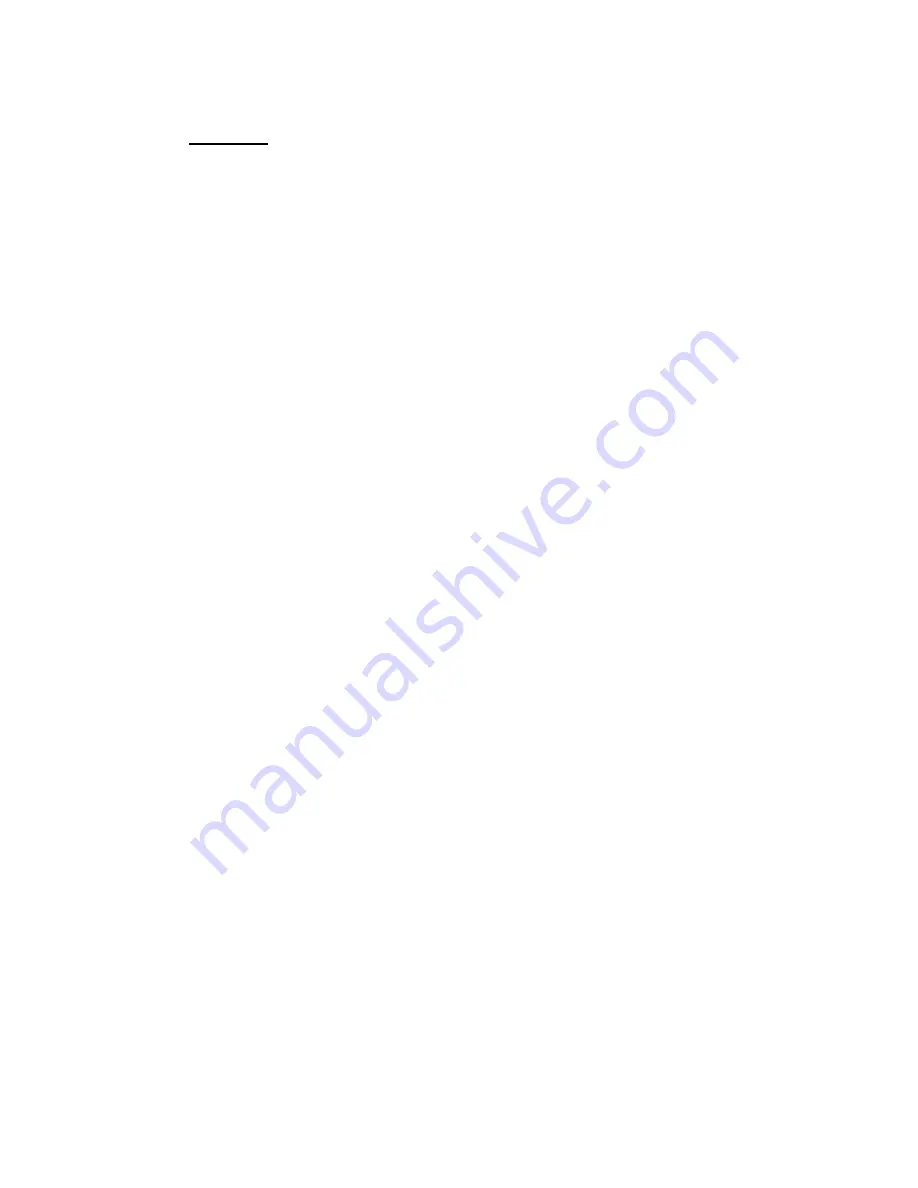
Preface ·
Page vii
PREFACE
Like its human counterpart, robot Sumo was born and thrives in Japan. It was
introduced to the United States in the early 1990's by Dr. Mato Hattori. One of the early
American adopters of robot Sumo was noted Seattle Robotics Society member, Bill
Harrison, who organized some of the first U.S. robot Sumo tournaments.
While things started out very slowly, robot Sumo eventually caught on. Bill created a
"lightweight" class that matched the Japanese physical dimensions of 20 cm by 20 cm,
but reduced the mass from three kilograms (6.6 pounds) to one kilogram (2.2 pounds).
The intention was to reduce the sophistication of the components required to construct a
working Sumo robot. Those early contests didn't have much in the way of corporate
support with prizes, so Bill resorted to offering 30 hours of his own machine-shop
services to the winner.
As luck would have it, Bill's friend Robert Jorgensen won that first contest prize. Since
Robert already had a winning Sumo robot, he suggested that they build a smaller version,
about half the size and weight of the lightweight class to be used as a robot Sumo
demonstrator. The result of their work was a very small Sumo robot that measured just 8
cm by 8 cm and mass about 240 grams. Bill took that first small Sumo to a contest in
San Francisco and actually won the lightweight competition – against bigger and heavier
robots. The Mini-Sumo robot class was born.
The Mini-Sumo dimensions (10 cm x 10 cm) and mass (500 grams) were formalized and
Bill published adapted Japanese robot Sumo rules on his Sine Robotics web site
(mirrored on many other sites, and reprinted with permission in this document). Through
Bill's tireless efforts and nearly ten years of travel – often toting more than 20 robots in
his bags – Mini-Sumo robotics has grown to a favorite activity among robot clubs all
across the United States.
RECOGNITIONS
Many Mini-Sumo designs – especially the dual-wheel-and-scoop concept – can be traced
back to Bill Harrison's early efforts to promote Mini-Sumo robotics competition.
Parallax also recognizes Bill Boyer of the Dallas Personal Robotics Group for his version
of the dual-wheel-and-scoop design that was refined and developed into the Parallax
SumoBot robot described in this text.
Summary of Contents for Boe-Bot
Page 1: ...SumoBot Mini Sumo Robotics Assembly Documentation and Programming VERSION 2 1...
Page 4: ......
Page 9: ...Preface Page ix...
Page 10: ......
Page 20: ......
Page 32: ......
Page 54: ......
Page 74: ......
Page 76: ......
Page 77: ...Appendix D SumoBot PCB Schematic Page 67 Appendix D SumoBot PCB Schematic...