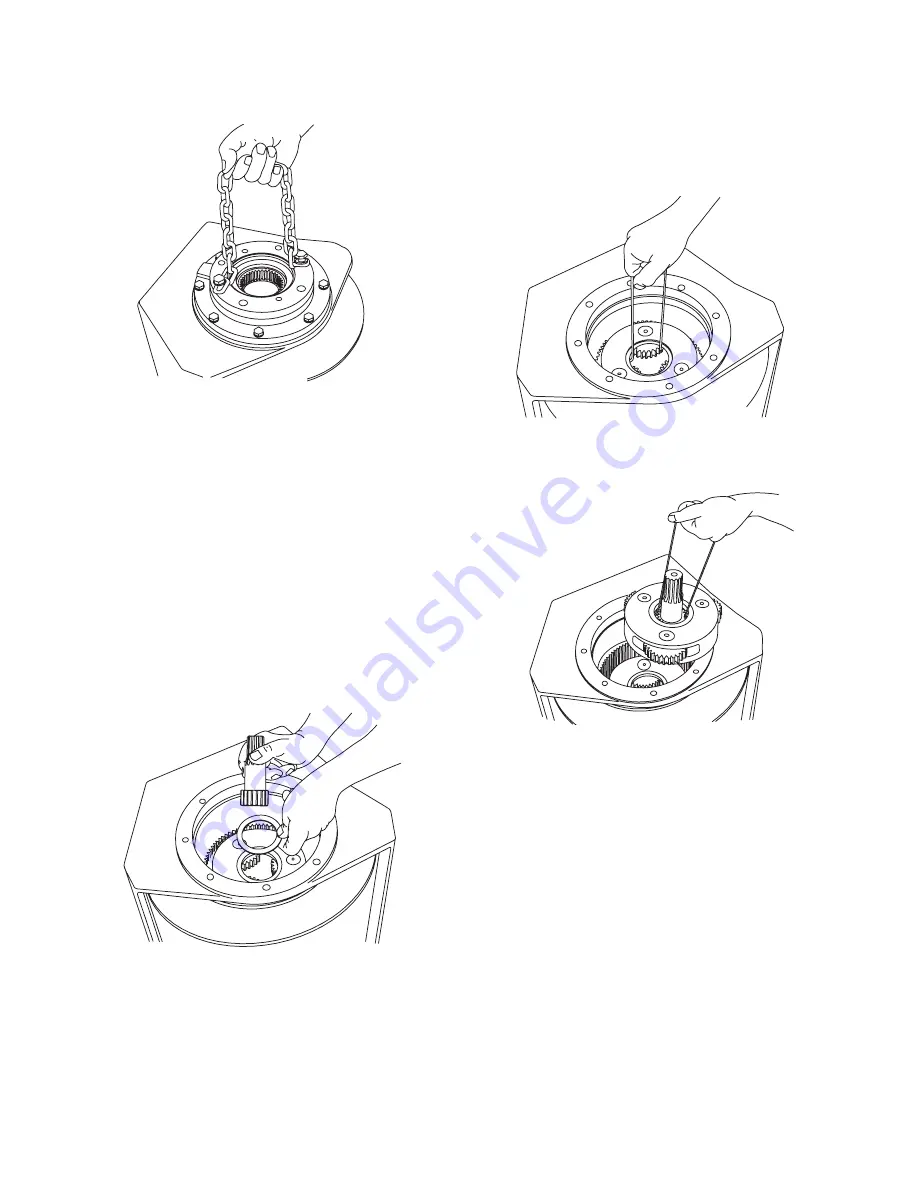
6. Remove the brake cylinder capscrews and install
two (2) capscrews and a short piece of chain into
the motor mounting bolt holes. Using the chain as
a handle, lift the brake cylinder assembly out of the
drum and base, being careful to avoid damaging
the sealing and bearing surfaces. Refer to “Motor
Support — Brake Cylinder Service” for additional
information.
7. (BG8A ONLY) Remove the drum closure. Remove
and discard the O-ring from the inside of the drum.
Remove the seal from the drum closure.
(BG8B) The seal is mounted in the drum. Remove
the seal and drum closure from the drum.
8. Clean and inspect the bearing in the drum closure
and replace if required.
9. Remove the primary sun gear and thrust washer
from the primary planet carrier.
NOTE:
23:1 gear ratio winches have a sun gear
adapter in addition to the sun gear shaft.
10. Remove the primary planet carrier from the drum.
Refer to “Planet Carrier Service” for additional infor-
mation.
11. Remove the output sun gear and thrust washer
from the output planet carrier.
12. Remove the output planet carrier from the drum.
Refer to “Planet Carrier Service” for additional
information.
13. Remove snap ring from bearing support.
14. Stand winch on motor end with bearing support up;
then remove bearing support capscrews and bear-
ing support being careful to avoid damaging the
sealing and bearing surfaces.
15. Slide drum out of base onto a work bench and
remove seal and bearing from support end.
16. Thoroughly clean and inspect drum and base.
Check ring gear (machined into inside surface of
drum) teeth for nicks, spalling or excessive wear.
Replace if wear is greater than 0.015 inch (0.4 mm)
when compared to unworn area of teeth.
16