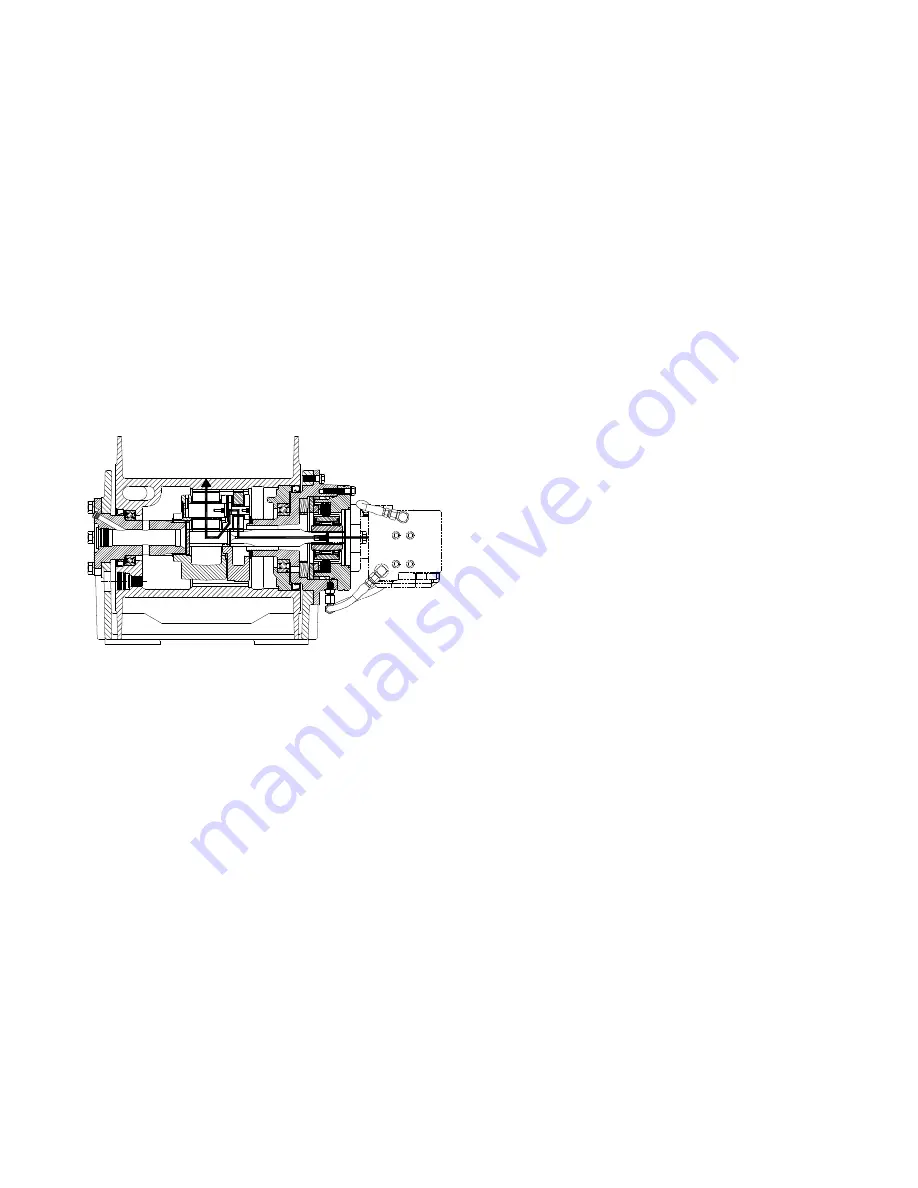
DESCRIPTION OF WINCH
The winch has three basic assemblies:
1. Hydraulic motor assembly and brake valve
2. Cable drum assembly
3. Brake cylinder and motor adapter
The hydraulic motor is bolted to the motor adapter
which in turn is bolted to the brake cylinder and the
winch base. The cable drum assembly is supported
by antifriction bearings which are located by the brake
housing at one end and the bearing support at the other
end. The ring gear for both planetary sets is machined
on the inside surface of the cable drum.
PLANETARY GEAR TRAIN
The hydraulic motor shaft is directly coupled to the
inner brake hub which is connected to the input shaft
which acts as the sun gear for the primary planetary
set. When driven by the input shaft, the primary planet
gears walk around the ring gear machined in the cable
drum and drive the primary planet carrier.
The primary planet carrier drives the output sun gear
which drives the output planet gears. The output planet
carrier is splined to the bearing support and cannot
rotate. As the output planet gears are driven by the
output sun gear, they drive the ring gear/cable drum.
DUAL BRAKE SYSTEM
The dual brake system consists of a dynamic brake
system and a static brake system.
The dynamic brake system has two operating compo-
nents:
1. Brake valve assembly
2. Hydraulic motor
The brake valve is basically a counterbalance valve.
The counterbalance valve is mounted to the hoist port
of the motor on units with 020, 029 and 039 motors.
Units with the 071 motor use a counterbalance valve
cartridge in the brake valve block which is bolted to
the motor. The operational theory of both systems is
the same. A check valve allows free flow of oil to the
motor in the haul-in direction and a pilot operated,
spring-loaded spool valve blocks the flow of oil out of
the motor when the control valve is placed in neutral.
When the control valve is placed in the pay-out posi-
tion, the spool valve remains closed until sufficient pilot
pressure is applied to the end of the spool to shift it
against spring pressure and open a passage. After the
spool valve cracks open, the pilot pressure becomes
flow-dependent and modulates the spool valve opening
which controls the pay-out speed. .
The static brake system has three operating compo-
nents:
1. Spring-applied, multiple friction-disc brake pack
2. Overrunning brake clutch assembly
3. Hydraulic brake cylinder and spring plate
The static brake consists of alternately stacked fric-
tion and steel brake discs. The steel brake discs are
externally splined to the motor adapter and cannot
rotate. The friction discs are internally splined to the
outer brake hub of the overrunning brake clutch. When
compressed by spring force, the brake pack locks the
overrunning brake clutch outer brake hub to the motor
adapter.
The static brake is released by the pilot pressure at a
pressure lower than that required to open the pilot oper-
ated brake valve. This sequence assures that dynamic
braking takes place in the brake valve and that little, if
any, heat is absorbed by the friction brake.
The friction brake is primarily a load holding brake and
will provide dynamic braking only during extremely slow
operation when there is insufficient flow to open the
brake valve.
The sprag type overrunning brake clutch is installed
between the inner brake race and the outer brake hub.
The overrunning brake clutch, allows the inner brake
race and input shaft to turn freely in the direction to haul
in cable and locks up to force the friction brake discs to
turn with the inner brake race and input shaft to pay out
cable. The brake pack remains fully applied when haul-
ing in cable and must be released by pilot pressure to
allow the brake discs to turn freely and pay-out cable.
THEORY OF OPERATION
4
Power Flow
(hoisting)