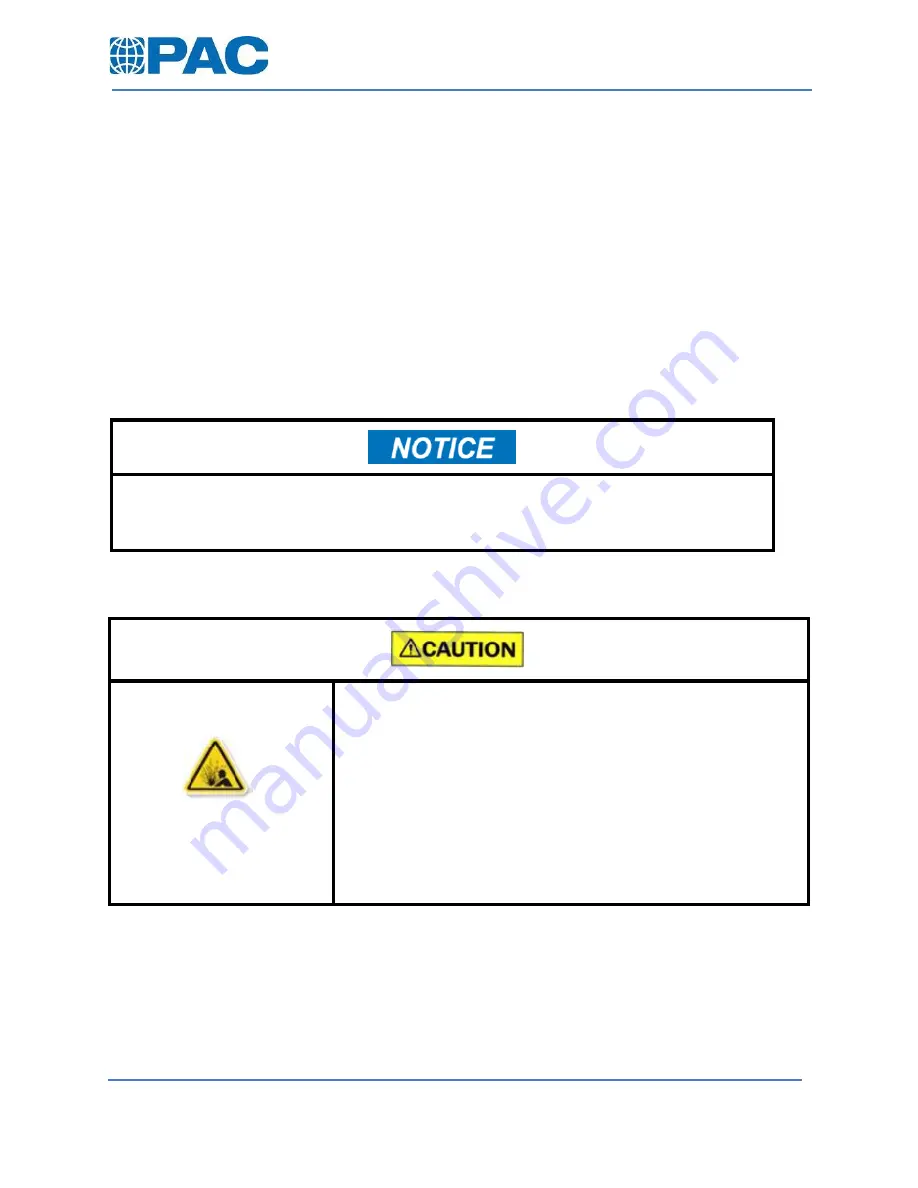
R6000S Operation Manual: Rev. G
PAC L.P., All Rights Reserved, 2015
Page 41 of 92
3. Loosen the two knurled screws on the top of the hinged furnace front panel and allow it to pivot down
to the open position.
4. Clean the outside of the pyrolysis tube with acetone or alcohol and allow it to dry.
5. Slide the pyrolysis tube into the front opening of the furnace until the pyrolysis tube is centered in the
furnace.
6. Place a pair of clay end pieces around the pyrolysis tube and in the furnace hole on both ends of the
furnace and slide a retaining clip over each end piece.
7.
Place the 1/4” fitting (with Teflon ferrule) that is on the tubing to the left (when facing front of unit) on
the pyro oxygen arm of the pyrolysis tube (arm closest to center of the pyrotube).
8.
Place the 1/4” fitting (with Teflon ferrule) on the tubing to the right (when facing front of unit) on the
inlet arm of the pyrolysis tube (arm closest to end of pyrotube).
9.
Install the 1/8” Teflon tubing with the stainless steel 1/4” - 1/8” right angle reducer attached at the
other end into the open 1/8” fitting on the membrane dryer (if not already installed).
10.
Place the 1/4” - 1/8” right angle reducer (with a Teflon ferrule) on the 1/4”outlet tube of the pyrotube.
11. Perform gas leak testing procedure.
POSSIBLE RELEASE OF HIGH PRESSURE HAZARD!
MILD OR MODERATE INJURY COULD OCCUR IF NOT AVOIDED!
A possible high pressure hazard exists.
HOW TO PROCEED: Avoid hazard by performing some or all of the following
actions: 1) depressurize system if needed 2) use system vent valves to release
pressure, and verify to correct pressures using system valves and read outs.
Ensure that all relevant safety precautions are carefully followed and all gas
lines, regulators, gas purifiers, etc. are specified for the intended use. Leaks in
gas lines must be repaired in order to maintain safe operating conditions. If a
safe operating pressure cannot be attained and maintained, the source of the
leak must be determined before continuing with the installation.
Because of availability, some units may be supplied with a straight 1/4” - 1/8” reducer. If the straight reducer is
supplied, the 1/8” Teflon tubing that connects the reducer to the membrane dryer may need to be replaced with a
slightly longer piece of tubing. The tubing that connects the outlet of the pyrotube to the membrane dryer
should not have any sharp bends.
Summary of Contents for R6000S
Page 1: ...R6000S Operation Manual Revision G www paclp com...
Page 4: ...Page 2 of 92 PAC L P All Rights Reserved 2015 R6000S Operation Manual Rev G LEFT BLANK...
Page 6: ...Page 4 of 92 PAC L P All Rights Reserved 2015 R6000S Operation Manual Rev G LEFT BLANK...
Page 12: ...Page 10 of 92 PAC L P All Rights Reserved 2015 R6000S Operation Manual Rev G LEFT BLANK...
Page 44: ...Page 42 of 92 PAC L P All Rights Reserved 2015 R6000S Operation Manual Rev G LEFT BLANK...
Page 50: ...Page 48 of 92 PAC L P All Rights Reserved 2015 R6000S Operation Manual Rev G LEFT BLANK...
Page 80: ...Page 78 of 92 PAC L P All Rights Reserved 2015 R6000S Operation Manual Rev G LEFT BLANK...
Page 81: ...PAGE 79 OF 92 INTERCONNECT DIAGRAM R6000S REF B42175 R3 TP 1 1...
Page 82: ...PAGE 80 OF 92 FLOW DIAGRAM INTERCONNECT DET FURNACE REF B42134 R1 TP 1 1...
Page 86: ...MK DA QM SR PAGE 84 OF 92 ASSY SULFUR DETECTOR W COOLER REF B42025 N TP 1 1...
Page 87: ...LL DGA QM SR PAGE 85 OF 92 WIRING DIAGRAM SULFUR DETECTOR 110 120VAC REF B42146 F TP 1 1...
Page 88: ...LL QM JK PAGE 86 OF 92 WIRING DIAGRAM SULFUR DETECTOR 220 230VAC REF B42145 E TP 1 1...
Page 91: ...PDalbello JBE PAGE 89 OF 92 COMPONENT IDENT REAR PANEL FURNACE SECTION REF B42162 R3 TP 1 1...
Page 92: ...PAGE 90 OF 92 FLOW DIAGRAM FURNACE SECTION WITH OPTIONAL FURNACE BYPASS REF B42163 R1 TP 1 1...
Page 94: ...PDalbello JBE PAGE 92 OF 92 WIRING DIAGRAM FURNACE SECTION 220 230VAC REF B42144 R3 TP 1 1...