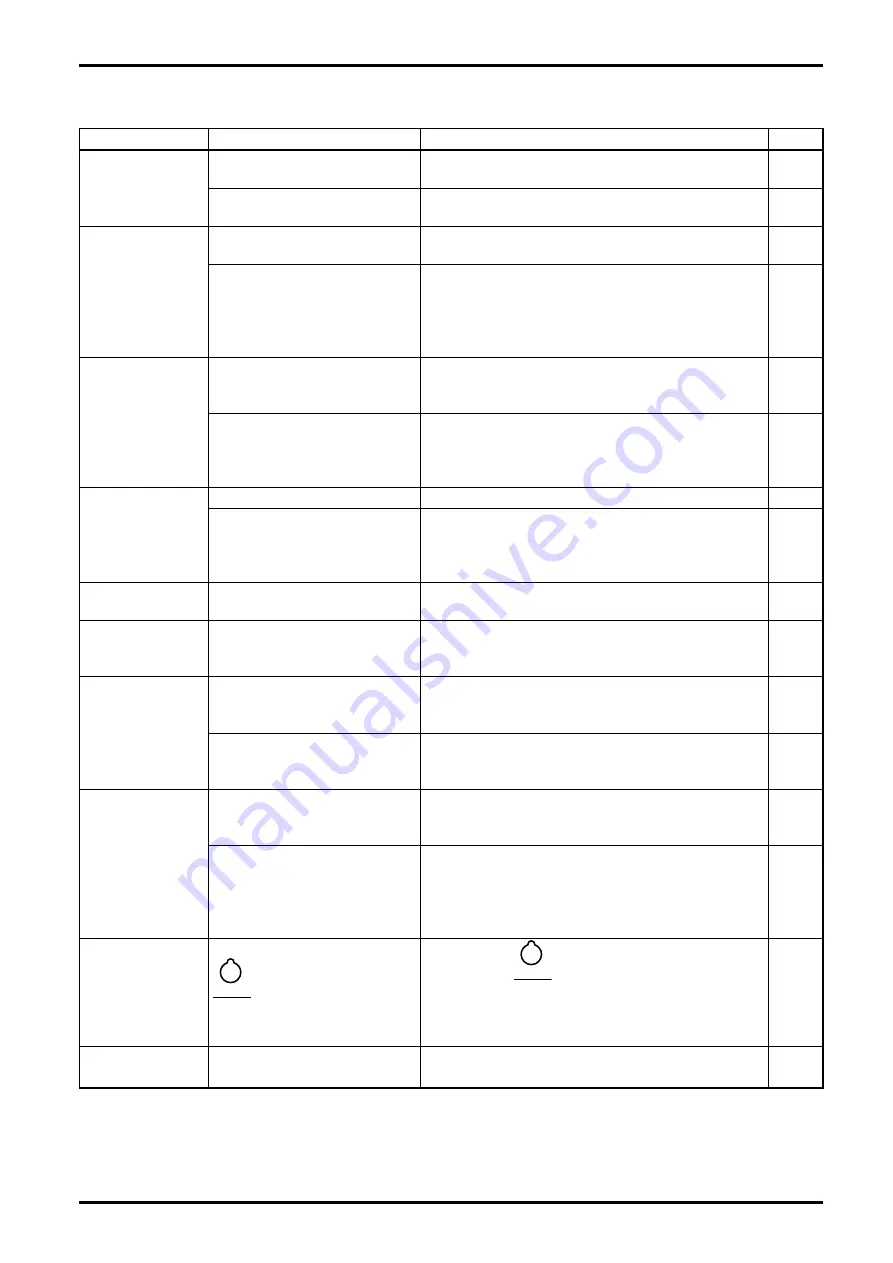
B-320-2-E
39
SYMPTOM
POSSIBLE CAUSE
CHECKOUT AND COUNTERMEASURE
Ref. page
10. Liquid leaks from
the pipeline.
Incomplete seals at pipeline
connections.
Retighten bolts at pipeline connections or replace
gaskets.
-
Incomplete seal in the rear cover
of flowmeter body.
Inspect flowmeter rear cover fitting bolts for tightness or
replace O-ring with new one.
32 to 35
11. Counts while
the shutoff valve
remains closed.
Leaks from shutoff valve or
pipeline connections.
Inspect shutoff valve and pipeline connections for leaks.
-
Air pockets exist between the
shutoff valve and flowmeter body;
the rotors keep a rocking motion
in response to pulsating pump
pressure.
Discharge the air to atmosphere.
-
12. Counter reading
too high.
Pulsation of the fluid causes
the rotors to move in a rocking
motion.
Provide a check valve and accumulator.
Influenced by external magnetic
fields. (The flow sensor picks
up external magnetic fields of a
motor, generator, etc.)
Isolate from external magnetic fields.
13. Counter reading
too low.
Air entrapped.
Discharge the air to atmosphere.
-
Influenced by external magnetic
fields (the flow sensor picks up
external magnetic fields of a
motor, generator, etc.)
Isolate from external magnetic fields.
4. "BATT" alarm
blinks.
Indicates a weak battery.
Referring to Sec. 10.2 "Battery Pack Replacement",
replace the battery pack early.
36
5. "BATT" alarm
blinks and
"ALM" stays on.
A low battery alarm. (The battery
is generally no longer serviceable
in this state.)
The meter is out of service until the battery is replaced.
Referring to Sec. 10.2 "Battery Pack Replacement",
replace with a new one.
36
16. Batch process
fails to stop
at the target
setpoint.
Trouble lies in the internal
assembly.
Does "OUT" go out and "END" light in the LCD at batch
setpoint? Monitor waveshapes according to Sec. 9.1
"Register Inspection.
7
29
Trouble lies in the solenoid valve.
Is the output (air signal) from solenoid valve switched
correctly at batch setpoint?
(With LW76E: OUT 1 OFF, OUT 2 OFF)
5
17. Batch process
stops while
metering is in
progress.
Single-acting shutoff valve:
Shutoff valve operating air
pressure has dropped.
Has the air pressure dropped below the operating
pressure range?
-
Intermittent interruption of the
process fluid flow during a batch
process causes missing pulse
detection and shutoff valve
closure signal generation.
Make sure of process fluid flow.
0
18. Cannot reset the
alarm.
RESET
▲
button is not pushed in as
far as it will go.
If pressing the
RESET
▲
button fails to reset, repeat the
same procedure with internal buttons in the internal
assembly. If this proves to be successful, trouble lies in
the external buttons or in the internal assembly.
16
19
19. LCD display is
dim.
The register is located higher
than the operator's eye level.
You can best view this LCD from above. Adjust its
installation height for best readability.