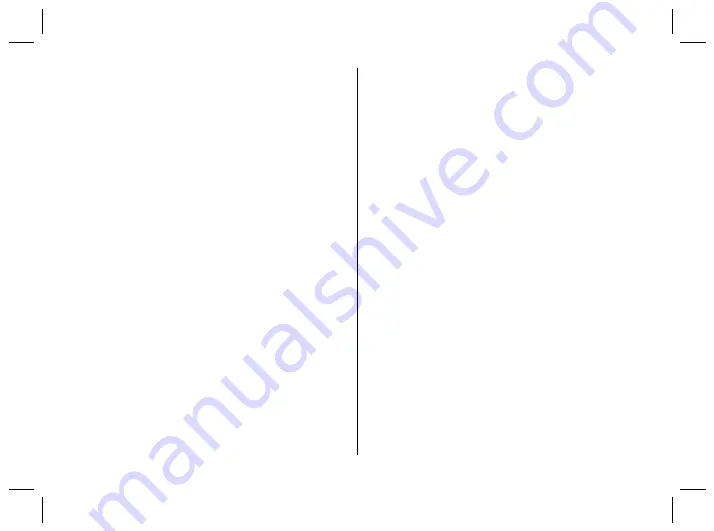
8) Pull a soaked PVA bag over the model.
9) Complete the lamination process with Orthocryl lamination resin.
10) Once the lamination resin has cured, remove the PVA bag.
11)
INFORMATION: Align an anchor arm that has been angled at
the factory in the posterior direction.
Move the lamination anchor arms to the correct
a–p
and
m–l
posi
tion. Never align the threaded clamping in the anterior or posteri
or direction.
12) Place the lamination anchor at the socket end as required for
proper alignment and bring it into position.
13)
Optional
: Adapt the anchor arms of the lamination anchor to the
model with a bending iron.
14) Install the lamination dummy (see Page 18).
15) Stabilise and fix the lamination anchor with a sealing resin/talcum
powder mixture.
16) Pull one layer of perlon stockinette over the model.
17) Place two layers of woven carbon fibre (e.g.
15 cm x 15 cm
) off
set over the lamination anchor arms.
18) Pull one layer of perlon stockinette over the model.
19) Pull two layers of carbon woven stockinette over the model.
20) Pull two layers of perlon stockinette over the model and tie off
below the cap screw.
21) Pull a soaked PVA bag over the model.
22) Complete the lamination process with Orthocryl lamination resin.
23) After the lamination resin has cured, remove the lamination
dummy.
5.2 Laminating the transtibial socket
>
Required materials:
torque wrench (e.g. 710D20), 711S4*
bending iron, 99B81 PVA bag, 623T3 perlon stockinette, 616B1
carbon fibre webbing, 699B1 fibreglass roving, 616G12 woven
carbon fibre, 616G15 woven carbon fibre stockinette, 617H119
Orthocryl lamination resin 80:20 PRO
1)
If the lamination anchor has a threaded connector:
Fully
screw in the screwed insert.
17
2) Tighten the cap screw of the threaded clamping using the torque
wrench (
10 Nm
).
3) Pull a soaked PVA bag over the model. The PVA bag should be
sealed by heat welding at the distal end.
4) Pull two layers of Perlon stockinette over the model.
5) Place three layers of woven carbon fibre (e.g.
15
cm x
15 cm
)
with offset fibre alignment on the distal end of the model.
6) Pull two layers of Perlon stockinette over the model.
7)
INFORMATION: Align an anchor arm that has been angled at
the factory in the posterior direction.
Move the lamination anchor arms to the correct
a–p
and
m–l
posi
tion. Never align the threaded clamping in the anterior or posteri
or direction.
8) Place the lamination anchor at the socket end as required for
proper alignment and bring it into position.
9)
Optional
: Adapt the anchor arms of the lamination anchor to the
model with a bending iron.
10) Install the lamination dummy (see Page 18).
11) Stabilise and fix the lamination anchor with a sealing resin/talcum
powder mixture.
12) Pull the fibreglass roving through the holes in the anchor arms
and allow it to hang in a loop. If there are no holes, allow the
fibreglass roving to hang around the anchor arms in a loop.
13) Place three layers of carbon fibre cloth (e.g.
15 cm x 15 cm
) in an
offset arrangement over the lamination anchor arms.
14) Pull one layer of Perlon stockinette over the model.
15) Pull two layers of carbon woven stockinette over the model.
16) Pull two layers of perlon stockinette over the model and tie off
below the cap screw.
17) Pull a soaked PVA bag over the model.
18) Complete the lamination process with Orthocryl lamination resin.
19) After the lamination resin has cured, remove the lamination
dummy.
Summary of Contents for 4R111
Page 2: ...1 2 3 4 2...
Page 3: ...5 6 7 8 9 10 3...
Page 4: ...11 12 13 4...
Page 148: ...2 4 3 5 3 3 1 3 2 147 148...
Page 164: ...5 3 3 1 3 2 163 164...
Page 169: ...mm 506G3 M8X12 V 12 506G3 M8X14 14 506G3 M8X16 16 6 1 2 3 7 30 169 8 9 9 1 9 2 CE 2017 745 9 3...
Page 173: ...3 3 1 3 2 171 173...
Page 178: ...3 506G3 M8X12 V 12 506G3 M8X14 14 506G3 M8X16 16 6 1 2 3 7 178 30 8 9 9 1 9 2 2017 745 CE 9 3...
Page 202: ...202...
Page 203: ...203...