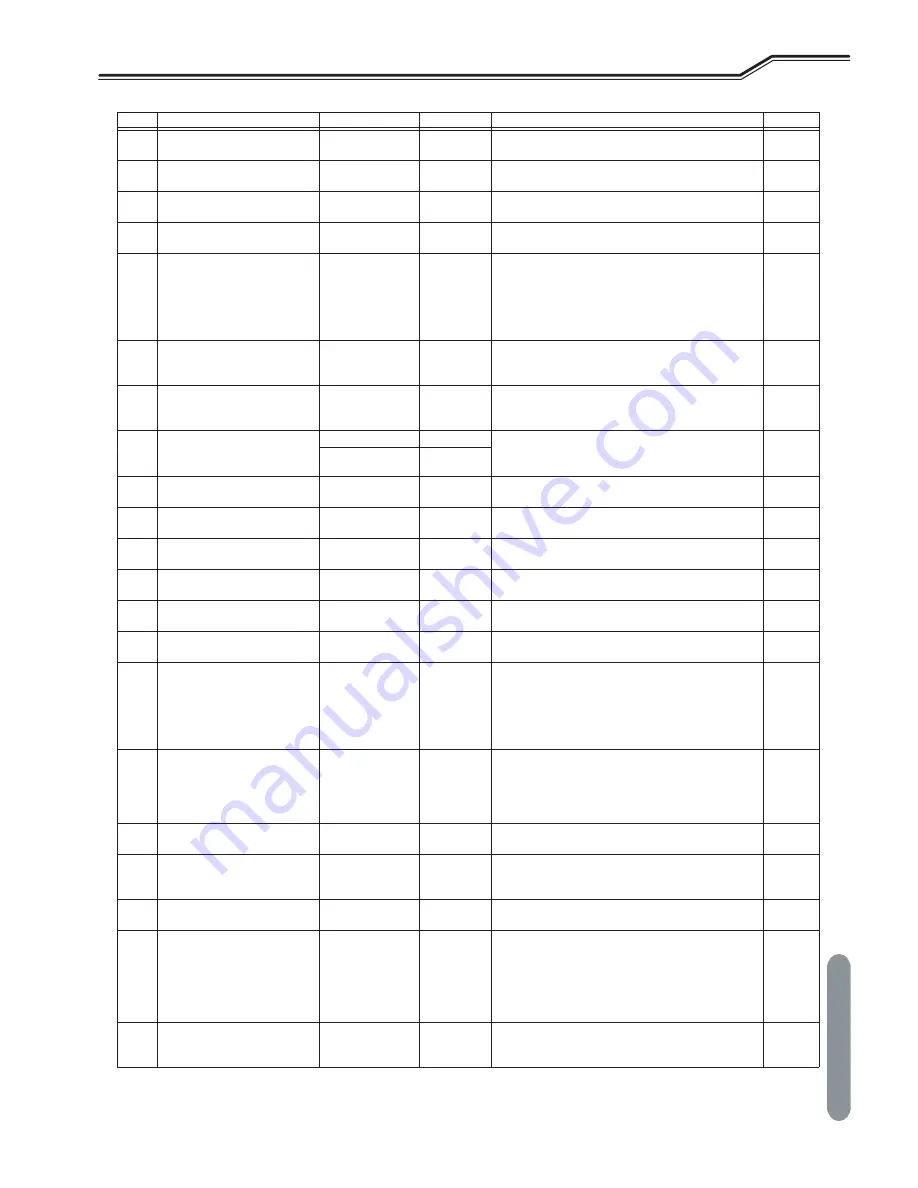
65
Chapter 6
W
elding Condition
L
IST
OF
W
ELDING
C
ONDITIONS
W
ELDING
C
ONDITION
C
HAPTER
6
F63
L pulse peak current fine
adjustment
-150 to 150
0 (A)
Sets the adjustment value of pulse peak current at the
LOW side in pulse welding.
㾎
F64
L pulse peak time fine
adjustment
-1.5 to 1.5
0.0 (ms)
Sets the adjustment value of pulse peak time at the
LOW side in pulse welding.
㾎
F65
L-base current fine adjustment
-60 to 60
0 (A)
Sets the adjustment value of base current at the LOW
side in pulse welding.
㾎
F66
Feeding amplitude ratio
adjustment
0 to 100
50 (%)
Sets the feeding amplitude ratio of wire feeder speed in
wave pulse welding.
㾎
F67
Setting change of current value
(initial condition, crater
condition)
OFF/ON
OFF
When “CRATER ON” is selected, sets the current value of
the initial condition and crater condition in the
percentage based on the current value of the welding
condition.
OFF: invalid
ON: settable with percentage
㾎
F68
Setting of current value (initial
condition)
10 to 300
100 (%)
Sets the current value of the initial condition in the
percentage based on the current value of the welding
condition.
㾎
F69
Setting of current value (crater
condition)
10 to 300
100 (%)
Sets the current value of the crater condition in the
percentage based on the current value of the welding
condition.
㾎
F70
Setting of upper limit of analog
remote control
20 to 400 (*1)
400 (A)
Sets the upper limit (the value when the knob is turned
clockwise all the way) of the welding current adjustable
by the analog remote control (optional accessory).
-
20 to 550 (*2)
550 (A)
F71
Interval welding function
OFF/ON
OFF
This function repeats arc ON/OFF to control the heat
input.
㾎
F72
Setting Arc-ON time (Interval
function)
0.20 to 9.99
1.00 (s)
Sets the Arc-ON time in the Interval welding function.
㾎
F73
Setting Arc-OFF time (Interval
function)
0.20 to 9.99
1.00 (s)
Sets the Arc-OFF time in the Interval welding
㾎
F74 to
F76
No function
OFF (fixed)
OFF
No functions are provided.
-
F77
Welding source identification
numbers
1 to 999
1
Sets whether power source identification numbers of
Welding result control function.
-
F78
Prevention of unintended torch
switch operation
OFF/ON
OFF
An error code is displayed when welding is not
performed for five seconds after the pre-flow.
-
F79
Switching of CAN
communication connection
device
0/1/2/3
0
Sets the connection device to be used for the CAN
communication.
0: Digital Remote Control Box
1: Digital panel (Attached to wire feeder) and Intelli torch
2: Push-Pull torch
3: Inline Assist feeder
-
F80
Switching of CAN
communication speed
0/1/2/3
0
Sets the connection speed of the CAN connection.
0: 500kbps
1: 1Mbps
2: 125kbps
3: 250kbps
-
F81
TIG Mode switch setting
OFF/ON
OFF
During TIG MODE, operating the torch switch can control
the welding start and end.
-
F82
Extended correction for
DC Pulse welding
0 to 30
0
If DC pulse welding is done with the output cable
extended, welding may become unstable. Adjustment of
this parameter may stabilize the welding.
-
F83
Arc length adjustment right after
starting
-20 to 10
0
Adjusts the arc length right after starting the welding
operation.
-
F84
Pulse automatic adjustment
0/1/2
0
Sets the pulse mode that has the pulse automatic
adjustment function.
0: Standard pulse mode
1: Pulse mode for automatic adjustment
2: Pulse mode for automatic adjustment; Fixing of
adjustment value
㾎
F85
Adjustment amount of pulse
automatic adjustment
-9.99 to 9.99
0
The currently retained adjustment amount of pulse
automatic adjustment can be checked. In addition, the
adjustment amount can be changed manually.
㾎
No.
Function Name
Setting range
Initial value
Explanation
Memory