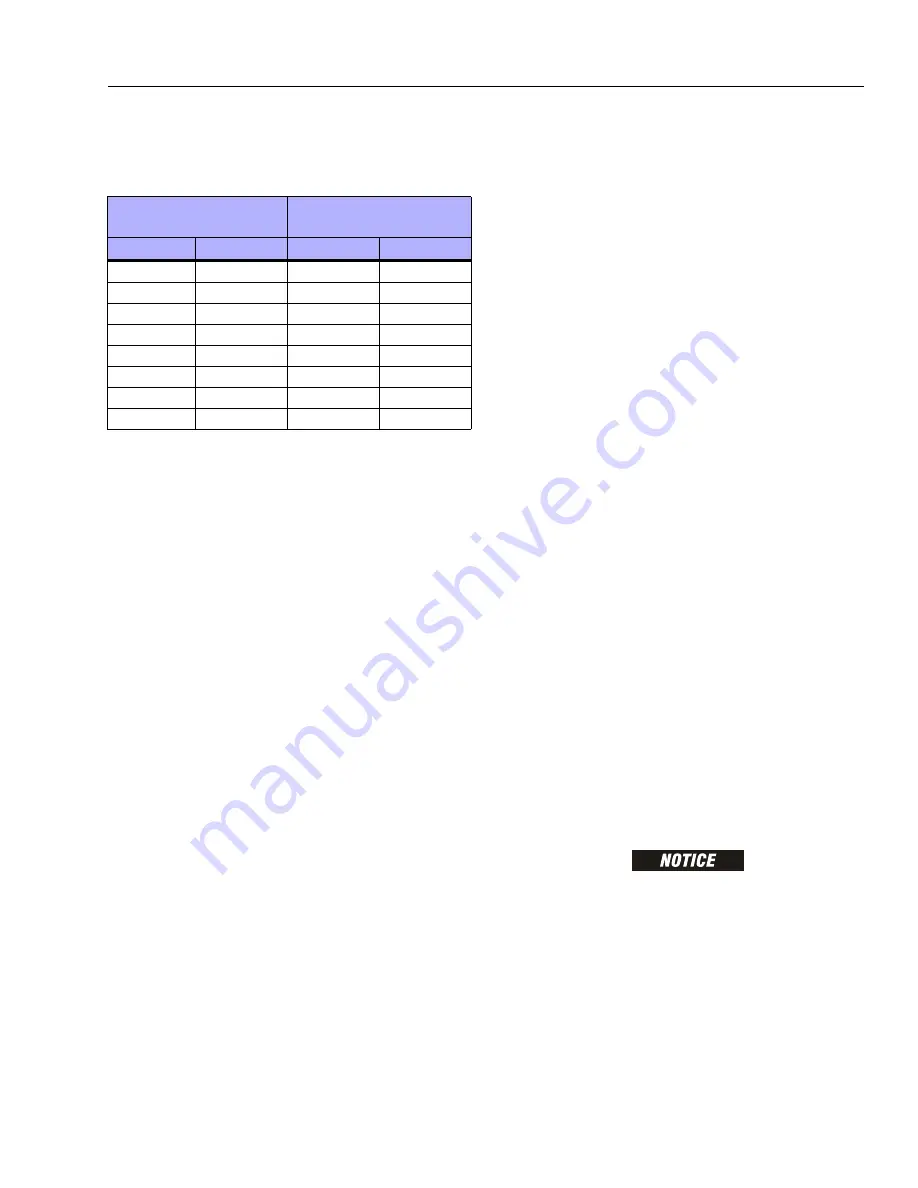
SECTION 2 - GENERAL
3121262
– JLG Lift –
2-5
Cylinder Drift
Drift is to be measured at the cylinder rod with a calibrated
dial indicator. The cylinder oil must be at ambient temperature
and temperature stabilized.
The cylinder must have the normal load, which is the normal
platform load applied.
If the cylinder passes this test, it is acceptable.
NOTE:
This information is based on 6 drops per minute cylinder
leakage.
2.5
PINS AND COMPOSITE BEARING REPAIR
GUIDELINES
Filament wound bearings.
1.
Pinned joints should be disassembled and inspected if
the following occurs:
a.
Excessive sloppiness in joints.
b.
Noise originating from the joint during operation.
2.
Filament wound bearings should be replaced if any of
the following is observed:
a.
Frayed or separated fibers on the liner surface.
b.
Cracked or damaged liner backing.
c.
Bearings that have moved or spun in their housing.
d.
Debris embedded in liner surface.
3.
Pins should be replaced if any of the following is
observed (pin should be properly cleaned prior to
inspection):
a.
Detectable wear in the bearing area.
b.
Flaking, pealing, scoring, or scratches on the pin sur-
face.
c.
Rusting of the pin in the bearing area.
4.
Re-assembly of pinned joints using filament wound
bearings.
a.
Housing should be blown out to remove all dirt and
debris...bearings and bearing housings must be free
of all contamination.
b.
Bearing / pins should be cleaned with a solvent to
remove all grease and oil...filament wound bearing
are a dry joint and should not be lubricated unless
otherwise instructed (i.e. sheave pins).
c.
Pins should be inspected to ensure it is free of burrs,
nicks, and scratches which would damage the bear-
ing during installation and operation.
2.6
WELDING ON JLG EQUIPMENT
NOTE:
This instruction applies to repairs, or modifications to the
machine and to welding performed from the machine on
an external structure, or component,
Do the Following When Welding on JLG Equipment
• Disconnect the battery.
• Disconnect the moment pin connection (where fitted)
• Ground only to structure being welded.
Do NOT Do the Following When Welding on JLG
Equipment
• Ground on frame and weld on any other area than the
chassis.
• Ground on turntable and weld on any other area than the
turntable.
• Ground on the platform/support and weld on any other
area than the platform/support.
• Ground on a specific boom section and weld on any other
area than that specific boom section.
• Allow pins, wear pads, wire ropes, bearings, gearing, seals,
valves, electrical wiring, or hoses to be between the
grounding position and the welded area.
FAILURE TO COMPLY WITH THE ABOVE REQUIREMENTS MAY RESULT IN COM-
PONENT DAMAGE (I.E. ELECTRONIC MODULES, SWING BEARING, COLLECTOR
RING, BOOM WIRE ROPES ETC.)
Table 2-2. Cylinder Drift
Cylinder Bore Diameter
Max. Acceptable Drift
in 10 Minutes
inches
mm
inches
mm
3
76.2
0.026
0.66
3.5
89
0.019
0.48
4
101.6
0.015
0.38
5
127
0.009
0.22
6
152.4
0.006
0.15
7
177.8
0.005
0.13
8
203.2
0.0038
0.10
9
228.6
0.0030
0.08
Summary of Contents for JLG 1500SJ
Page 1: ...Service and Maintenance Manual Model 1500SJ P N 3121262 March 7 2016...
Page 2: ......
Page 24: ...xx JLG Lift 3121262 LIST OF TABLES TABLE NO TITLE PAGE NO This page left blank intentionally...
Page 40: ...SECTION 1 SPECIFICATIONS 1 16 JLG Lift 3121262 NOTES...
Page 62: ...SECTION 3 CHASSIS TURNTABLE 3 12 JLG Lift 3121262 Figure 3 11 Axle Loctite Application...
Page 186: ...SECTION 3 CHASSIS TURNTABLE 3 136 JLG Lift 3121262 Figure 3 72 EMR2 Fault Codes Sheet 1 of 5...
Page 187: ...SECTION 3 CHASSIS TURNTABLE 3121262 JLG Lift 3 137 Figure 3 73 EMR2 Fault Codes Sheet 2 of 5...
Page 188: ...SECTION 3 CHASSIS TURNTABLE 3 138 JLG Lift 3121262 Figure 3 74 EMR2 Fault Codes Sheet 3 of 5...
Page 189: ...SECTION 3 CHASSIS TURNTABLE 3121262 JLG Lift 3 139 Figure 3 75 EMR2 Fault Codes Sheet 4 of 5...
Page 190: ...SECTION 3 CHASSIS TURNTABLE 3 140 JLG Lift 3121262 Figure 3 76 EMR2 Fault Codes Sheet 5 of 5...
Page 202: ...SECTION 3 CHASSIS TURNTABLE 3 152 JLG Lift 3121262...
Page 204: ...SECTION 3 CHASSIS TURNTABLE 3 154 JLG Lift 3121262...
Page 206: ...SECTION 3 CHASSIS TURNTABLE 3 156 JLG Lift 3121262...
Page 216: ...SECTION 3 CHASSIS TURNTABLE 3 166 JLG Lift 3121262...
Page 218: ...SECTION 3 CHASSIS TURNTABLE 3 168 JLG Lift 3121262...
Page 220: ...SECTION 3 CHASSIS TURNTABLE 3 170 JLG Lift 3121262...
Page 222: ...SECTION 3 CHASSIS TURNTABLE 3 172 JLG Lift 3121262...
Page 224: ...SECTION 3 CHASSIS TURNTABLE 3 174 JLG Lift 3121262...
Page 240: ...SECTION 3 CHASSIS TURNTABLE 3 190 JLG Lift 3121262...
Page 244: ...SECTION 3 CHASSIS TURNTABLE 3 194 JLG Lift 3121262...
Page 273: ...SECTION 4 BOOM PLATFORM 3121262 JLG Lift 4 25 Figure 4 6 Boom Assembly Sheet 7 of 7...
Page 305: ...SECTION 4 BOOM PLATFORM 3121262 JLG Lift 4 57 Figure 4 14 Jib Assembly Sheet 2 of 3...
Page 318: ...SECTION 4 BOOM PLATFORM 4 70 JLG Lift 3121262 Figure 4 18 Powertrack Hosing Sheet 2 of 3...
Page 319: ...SECTION 4 BOOM PLATFORM 3121262 JLG Lift 4 71 Figure 4 19 Powertrack Hosing Sheet 3 of 3...
Page 332: ...SECTION 4 BOOM PLATFORM 4 84 JLG Lift 3121262 Figure 4 22 Outer Mid Boom Extend Retract Cables...
Page 333: ...SECTION 4 BOOM PLATFORM 3121262 JLG Lift 4 85 Figure 4 23 Fly Boom Extend Retract Cables...
Page 350: ...SECTION 4 BOOM PLATFORM 4 102 JLG Lift 3121262 Figure 4 29 Rotator Counterbalance Valve...
Page 516: ...SECTION 5 BASIC HYDRAULIC INFORMATION HYDRAULIC SCHEMATICS 5 162 JLG Lift 3121262 NOTES...
Page 536: ...SECTION 6 JLG CONTROL SYSTEM 6 20 JLG Lift 3121262 Figure 6 2 Control System Block Diagram...
Page 545: ...SECTION 6 JLG CONTROL SYSTEM 3121262 JLG Lift 6 29 Figure 6 10 Control Module Location...
Page 704: ...SECTION 7 BASIC ELECTRICAL INFORMATION ELECTRICAL SCHEMATICS 7 60 JLG Lift 3121262 NOTES...
Page 705: ......