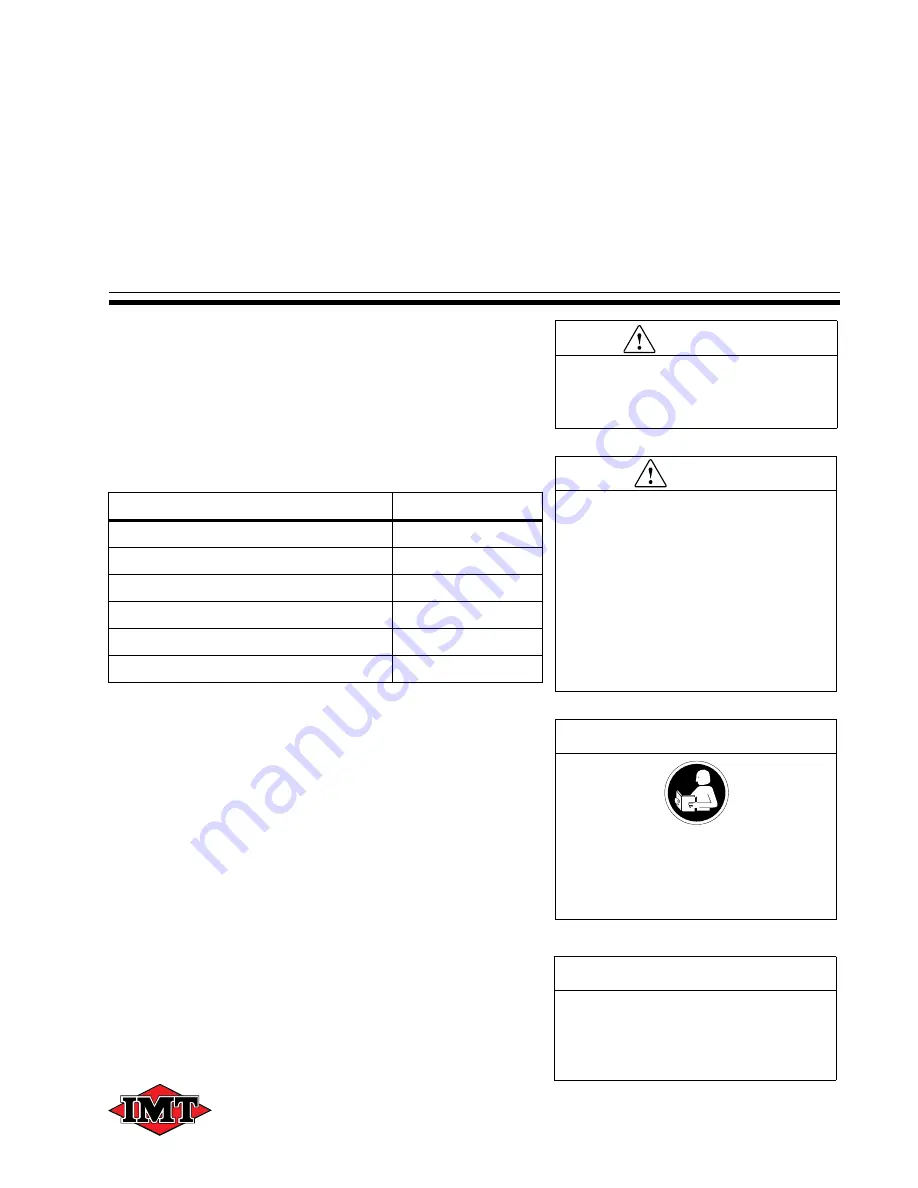
CAS40P 40 CFM / 100 PSIG
SECTION 5: OPERATION
PAGE - 21
®
An Oshkosh Corporation Company
5.1 GENERAL INFORMATION
The CAS40P compressor has a comprehensive array of
controls and indicators. Understanding the correct
operation of the system will help you to understand and
recognize when it is operating optimally. The information
in the Operation Section will help the operator to
recognize and interpret the readings, which will call for
service or indicate the beginning of a malfunction
.
5.2 OPERATING CONDITIONS
•
Operate only in well-ventilated areas.
•
Ensure there are no obstructions of cooling air intakes
and outlets around the machine.
•
Do not leave anything resting on top of the machine. Hot
cooling air will generate high heat and must not be
restricted.
•
Be sure to leave sufficient room around the machine for
cooling air circulation. There must be a minimum of 10
(ten) inches for the cooler intake, and 10 (ten) inches for
the sides and rear. Heated air must be able to vent away
from the intake.
•
Operate machine with the top cover closed, and all
panels secured in place.
•
Refer to specifications for operating parameters.
System Component Group
Manual Section
GENERAL INFORMATION
5.1
OPERATING CONDITIONS
5.2
FIRST TIME START-UP
5.3
SHUTDOWN (FIRST TIME AND ROUTINE)
5.4
ROUTINE START-UP
5.5
EXTREME CONDITION OPERATION
5.6
SECTION 5:
OPERATION
NOTE
The vehicle should be on a level surface
to ensure that the sight glass reading is
accurate. Refer to
Section 6.4.3.1,
Checking the Oil Level
for procedure on
checking the oil.
NOTE
Before starting the IMT CAS40P
compressor, read this section
thoroughly and familiarize yourself with
the controls and indicators - their
purpose, location and use.
WARNING
Before performing maintenance:
Shut down machine, relieve all system
pressure and lock out all power, as per
the Safety Section of this manual. If
machine is hot, allow package to cool
before removing any panel.
NOTE THAT THE SYSTEM CAN BE
STARTED REMOTELY:
Always clearly tag the start-up
instrumentation against accidental
system start-ups during maintenance.
WARNING
Install, operate, and maintain this
equipment in full compliance with all
applicable OSHA, other Federal, state,
local codes, standards, and regulations.
Manual #99905382 Rev 02
(JUNE 2018)
Summary of Contents for IMT CAS40P
Page 119: ...BLANK PAGE...