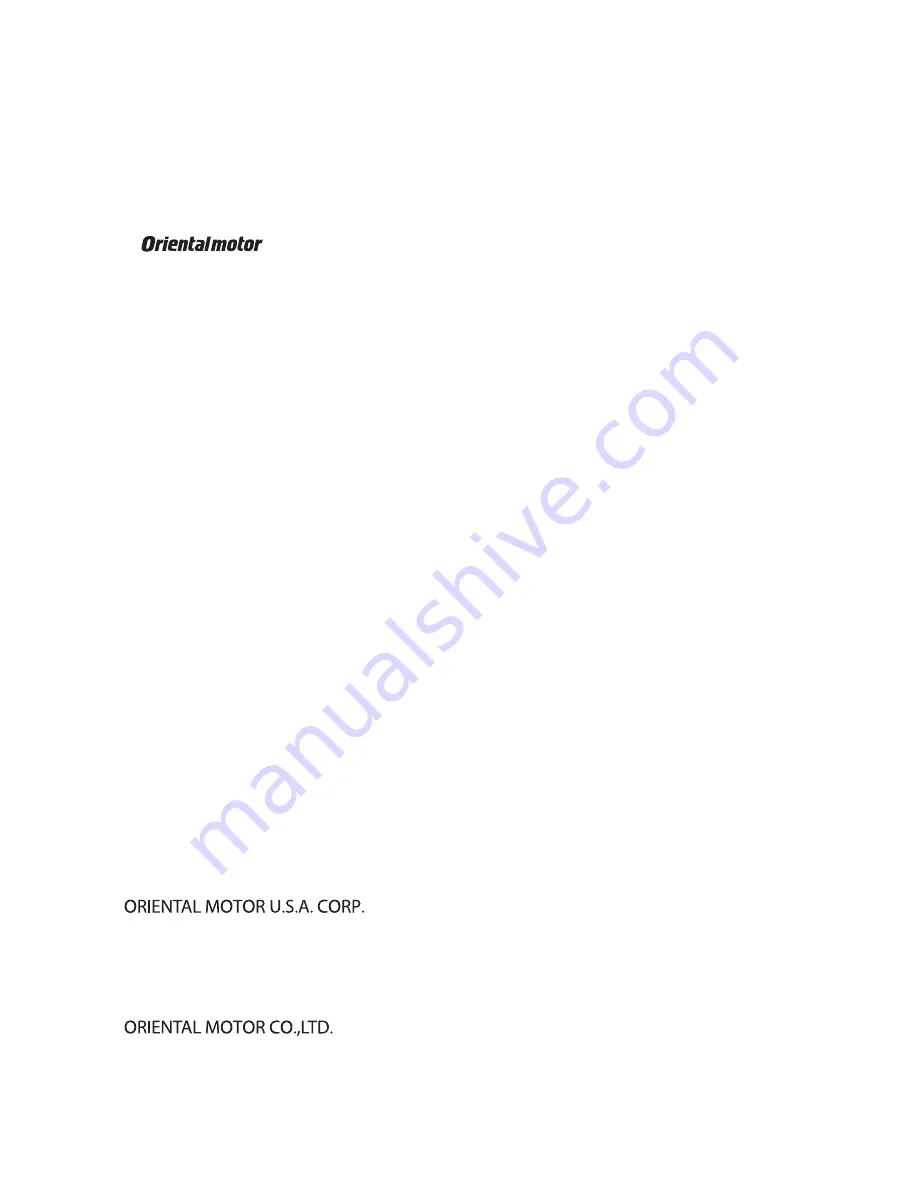
•
Unauthorized reproduction or copying of all or part of this Operating Manual is prohibited.
If a new copy is required to replace an original manual that has been damaged or lost,
please contact your nearest Oriental Motor branch or sales office.
•
Characteristics, specifications and dimensions are subject to change without notice.
•
While we make every effort to offer accurate information in the manual, we welcome
your input. Should you find unclear descriptions, errors or omissions, please contact the
nearest office.
•
is a registered trademark or trademark of Oriental Motor Co., Ltd., in
Japan and other countries.
Other product names and company names mentioned in this manual may be trademarks or
registered trademarks of their respective companies and are hereby acknowledged. The
third-party products mentioned in this manual are recommended products, and references
to their names shall not be construed as any form of performance guarantee. Oriental
Motor is not liable whatsoever for the performance of these third-party products.
© Copyright
ORIENTALMOTOR CO., LTD. 2008
Printed on Recycled Paper
Technical Support Tel:(800)468-3982
8:30
A.M.
to 5:00
P.M.
, P.S.T. (M-F)
7:30
A.M.
to 5:00
P.M.
, C.S.T. (M-F)
E-mail: [email protected]
www.orientalmotor.com
Headquarters Tokyo, Japan
Tel:(03)3835-0684 Fax:(03)3835-1890
• Please contact your nearest Oriental Motor office for further information.